Author |
Message |
skyto Samba Member
Joined: November 24, 2003 Posts: 177 Location: Finland
|
Posted: Mon Oct 03, 2011 5:45 am Post subject: Torlon 4435 vanes for Judson |
|
|
Promotional info wrote: |
Not only is Torlon 4435 particularly suited to applications where lubrication is impossible or undesirable, it provides an additional margin of safety for lubricated systems in the event that lubrication is lost. |
Link to Mercedes 190SL site, Judson modifications
I think this is the right way to increase the reliability and performance of a Judson. It won't turn into a Shorrock but friction could be diminished. A temporary oiling problem shouldn't end up like this.
The stock vane dimensions are 129 x 42 x 4.6mm. Torlon material is sold by 305 x 101.6 x 4.7mm plates that's enough for one supercharger. Price for that is $128.
Question: as machining will be required, do you know of any Judson restorer / seller who is already offering torlon vanes as an option? |
|
Back to top |
|
 |
John Moxon  Samba Moderator
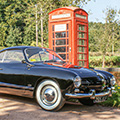
Joined: March 07, 2004 Posts: 14165 Location: Southampton U.K.
|
Posted: Mon Oct 03, 2011 8:56 am Post subject: |
|
|
Yes Torlon is definitely the way to go with the Judson and I've had long discussions with the main Judson restorers about just what it would take to change over entirely to replace the old Phenolic Linen.
The main problems are the Torlon sheets supplied are just fractionally too thick to fit the original Judson rotor slots and the cost.
The cost factor isn't too much of a deal breaker but the thickness of the material is...each sheet would need to be planed to the correct thickness before cutting to size.
Add to this the fact that most of the restorers carry a large stock of Phenolic Linen vanes ready cut to size and to the correct thickness. Changing over to Torlon would involve them throwing out large stocks of perfectly serviceable vanes and involve them in a lot of time consuming work in cutting and planing the new stock to size.
That's why the change over to Torlon hasn't happened up 'til now. However if someone out there has the tooling to cut and plane Torlon to the size needed, the market for this superior product is there. _________________ John.
Judson Supercharger Information on The Samba
My 1958 Shorrock Supercharged Karmann Ghia
Stop dead photo links! Post your photos to The Samba Gallery! |
|
Back to top |
|
 |
skyto Samba Member
Joined: November 24, 2003 Posts: 177 Location: Finland
|
Posted: Sat Dec 03, 2011 5:12 am Post subject: |
|
|
It's here.
Here's the torlon with the vanes my restored Judson came with. I somehow got a thicker plate, 6.4mm instead of the 4.7mm. That's not bad as the raw material isn't perfectly flat and needs to be trued anyway, so now there's some safety margin.
Here's some advice I got from the manufacturer, Drake Plastics
..we work hard to deliver the flattest plate possible, but in Torlon in thin sections that can be a challenge.
4435 in thin sections will take a 'set' if flexed. We use a small arbor press to straighten vanes and vane stock, or flex them by hand. This will make your machining go much easier. To get to final thickness you will probably have to flip them from side to side several times, taking small passes on each side.
When I get the new rotor from Ricardo I'll check the dimensions and have the vanes made. |
|
Back to top |
|
 |
John Moxon  Samba Moderator
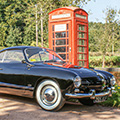
Joined: March 07, 2004 Posts: 14165 Location: Southampton U.K.
|
|
Back to top |
|
 |
avus Samba Member

Joined: November 11, 2005 Posts: 271 Location: Drain, Oregon
|
Posted: Sat Dec 03, 2011 11:52 am Post subject: oversize vanes |
|
|
The vanes in my Judson have been machined for oversize vane material (nominal .250"), so I would be interested in purchasing enough of the thicker (6.4mm) to replace the phenolic ones. I don't recall the exact dimension to which we machined the slots, so not sure of the exact thickness I need.
Do you plan to mill the entire sheet to thickness, or blank out the vanes before machining individually?
skyto wrote: |
It's here.
Here's the torlon with the vanes my restored Judson came with. I somehow got a thicker plate, 6.4mm instead of the 4.7mm. That's not bad as the raw material isn't perfectly flat and needs to be trued anyway, so now there's some safety margin.
Here's some advice I got from the manufacturer, Drake Plastics
..we work hard to deliver the flattest plate possible, but in Torlon in thin sections that can be a challenge.
4435 in thin sections will take a 'set' if flexed. We use a small arbor press to straighten vanes and vane stock, or flex them by hand. This will make your machining go much easier. To get to final thickness you will probably have to flip them from side to side several times, taking small passes on each side.
When I get the new rotor from Ricardo I'll check the dimensions and have the vanes made. |
|
|
Back to top |
|
 |
skyto Samba Member
Joined: November 24, 2003 Posts: 177 Location: Finland
|
Posted: Sat Dec 03, 2011 12:55 pm Post subject: |
|
|
If it's cut in two there'll be minimal surface curvature. So two vanes would be milled to thickness at the same time. |
|
Back to top |
|
 |
TomSimon Samba Member
Joined: January 13, 2004 Posts: 751
|
Posted: Mon Dec 05, 2011 10:54 am Post subject: |
|
|
My Torlon machining experience is more than 25yrs old, but the principle is the same. If I remember right, the formula I was working with was very abrasive compared to most other plastics and metals. It did not transfer heat very well, either, remarkably slow transfer when compared to other plastics. Maybe as abrasive as PVC plastic, but much tougher, like it has silica in it (which would explain the high modulus, slow heat transfer, and abrasiveness). Once the tool dulled, the heat generation went up, and warping increased. At least, that is what I remember.
Most plastic sheet has a notoriously stressy skin on both sides direct from the mill, similar in that way to stainless steel plate. The Torlon plate I machined, had a stressed 'skin' on it. I'd advise flycutting the 'skin' off of one side, letting it do it's thing (warp), flip it over and hold it from the edges in it's new warped state, then flycut side #2. I would plan to cut a minimum of .015" off of each side, flipping the parts over before the next progressive cut. If you force it flat and cut, it will just spring when you release it.
Tool: I'd use a very sharp, single point HSS or Cobalt (better) tool bit with a small nose radius <.025", ground with a lot of top and side rake, as to keep generated heat to a minimum and encouraging the chip to curl and go away. I'd probably use a spray-mister set up to reduce heat at the cutting edge and the part as a whole.
If I could get plate that came was flat enough from the mill for use as vanes, I'd look into the feasibility of milling the rotor slots wider to accept the plate I could buy. Just an idea. |
|
Back to top |
|
 |
John Moxon  Samba Moderator
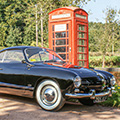
Joined: March 07, 2004 Posts: 14165 Location: Southampton U.K.
|
Posted: Mon Dec 05, 2011 11:39 am Post subject: |
|
|
There was an Austin Healey Sprite Judson owner I know who bought and machined a set of Torlon vanes about 8 years ago. I've passed on his email address to "skyto" so he can call on his cutting experience and how he got on running the vanes in his Judson. That was before I realised we had some first hand experience so close at hand Tom.
I don't recall his judgement on the outcome...either cutting or performance-wise. I do remember at that time the cost of a set of vanes ran to about $120 which wasn't a problem but today "skyto" tells me the sheet of Torlon supplied ran to $350. At that price you don't want any mishaps when cutting to size.
Certainly cutting the rotor slots to accommodate the width supplied has always seemed the best option and if you were buying a new rotor from one of the Judson restorers/suppliers you would also be buying a new set of vanes.
However the restorer/suppliers also keep a large stock of traditional Phenolic linen vanes which are cheap and easy to work. It's easy to understand why they're not highly motivated to change to Torlon and create a new set of problems for themselves.
Sadly I think anyone who wants to use Torlon for their Judson will for some time yet, be working on their own or in a small number. That's why in 2011 we're still using old technology when something better exists...but isn't that the ethos of "Vintage Speed."  _________________ John.
Judson Supercharger Information on The Samba
My 1958 Shorrock Supercharged Karmann Ghia
Stop dead photo links! Post your photos to The Samba Gallery! |
|
Back to top |
|
 |
skyto Samba Member
Joined: November 24, 2003 Posts: 177 Location: Finland
|
Posted: Tue Dec 06, 2011 1:44 pm Post subject: |
|
|
Thanks alot Tom, this is just what is needed. It's sure anyone round here who'll take this cutting job has no previous experience in Torlon.
The plastics company advertises this:
If your design is still changing or quantities do not justify the tooling expense of injection molding, let us provide machined parts from one of our standard or custom Torlon or PEEKshapes. For complex geometries, assemblies or industry-specific parts, we can recommend a qualified fabricator that specializes in the production of parts from our materials.
We provide many standard parts such as bushings, bearings, balls and seals, operating the latest CNC machine tools. We utilize diamond tooling to optimize surface finishes and to deliver the most dimensionally consistent parts.
All parts are delivered with inspection reports.
Torlon wear parts and parts designated for harsh chemical service can be re-cured after machining as required.
Not a bad idea, if the price is right. Re-curing as extra bonus. Maybe the other way would be to order a rotor from Ricardo with slots made for the 4.7mm standard material thickness. |
|
Back to top |
|
 |
John TC Samba Member
Joined: August 14, 2010 Posts: 117 Location: Jersey UK
|
Posted: Fri Dec 09, 2011 12:38 am Post subject: |
|
|
skyto wrote: |
Thanks alot Tom, this is just what is needed. It's sure anyone round here who'll take this cutting job has no previous experience in Torlon.
The plastics company advertises this:
If your design is still changing or quantities do not justify the tooling expense of injection molding, let us provide machined parts from one of our standard or custom Torlon or PEEKshapes. For complex geometries, assemblies or industry-specific parts, we can recommend a qualified fabricator that specializes in the production of parts from our materials.
We provide many standard parts such as bushings, bearings, balls and seals, operating the latest CNC machine tools. We utilize diamond tooling to optimize surface finishes and to deliver the most dimensionally consistent parts.
All parts are delivered with inspection reports.
Torlon wear parts and parts designated for harsh chemical service can be re-cured after machining as required.
Not a bad idea, if the price is right. Re-curing as extra bonus. Maybe the other way would be to order a rotor from Ricardo with slots made for the 4.7mm standard material thickness. |
Have they been contacted for a quote? maybe a group buy would help with costs |
|
Back to top |
|
 |
skyto Samba Member
Joined: November 24, 2003 Posts: 177 Location: Finland
|
Posted: Wed Jan 11, 2012 5:28 am Post subject: |
|
|
Some progress. I got the new rotor from Ricardo. Looks excellent, and a nice surprise: the slots were 4.80 - 4.82mm wide.
The readily available Torlon thickness, .187'' / 4.75mm would be a perfect match if it's flat or can be straightened easily. |
|
Back to top |
|
 |
skyto Samba Member
Joined: November 24, 2003 Posts: 177 Location: Finland
|
Posted: Wed Jan 18, 2012 2:39 pm Post subject: |
|
|
In the meantime I'm trying to improve the air filter. Special vanes are not an improvement if dust can enter the blower. There'd be the same grinding friction eating away the rotor and chamber.
This one is a K&N. Not the best in filtration, but "adequate", at least it's a filter. The rubber ends seem to seal well. It'll look different - as it ought to. Form follows function.
|
|
Back to top |
|
 |
John TC Samba Member
Joined: August 14, 2010 Posts: 117 Location: Jersey UK
|
Posted: Wed Jan 18, 2012 11:37 pm Post subject: |
|
|
That looks like it will do the job
what K&N part munber is it? |
|
Back to top |
|
 |
skyto Samba Member
Joined: November 24, 2003 Posts: 177 Location: Finland
|
Posted: Thu Jan 19, 2012 1:43 am Post subject: |
|
|
RU-0400, 3''d x 4''h, free shipping from/within UK, search Ebay.co.uk for the vendor. The threaded bar holding the endcap will have to be extended with anything taller than 4''.
I cut the rubber flange off, widened the hole to 52mm and cut the rubber top for the endcap boss to fit in the center.
Here's the final version, RU-0410. 5'' tall. I decided to extend the stud. Original threads were alien technology, like m6 with 1.17mm pitch. So I just cut it and made M6 threads at the other end.
With time, I suspect the filter could lose it's original length and a gap might appear at the ends, especially on bumpy dirt roads. I didn't want to use any sealants or glue, instead I made a collar for the intake end (a modified sprinkler collar) with a foam filter donut insert (cutout of a pipercross foam sheet). The collar has the same diameter as the carburetor top, shouldn't be too restrictive. The filter cap was stuffed likewise.
There are two K&N formulas to calculate the filter size, search internet for these
- in relation to effective filtering area, engine size and max rpm
- flow: engine CFM and CFM of filter
Results were the same using both formulas. Boost factor for 6PSI would be 1.4 for the effective filtering area.
Filter height calculations: 3'' filter diameter, shape=round straight, including .75'' for rubber end caps, max rpm 4500, displacement 73CID (1200cc):
Without boost: minimum height 2.4'', dusty conditions 3.3'', severe dust 4.1''
With 6PSI boost: minimum height 3.1'', dusty conditions 4.3'', severe dust 5.5''
Last edited by skyto on Wed Feb 01, 2012 8:42 am; edited 1 time in total |
|
Back to top |
|
 |
skyto Samba Member
Joined: November 24, 2003 Posts: 177 Location: Finland
|
Posted: Tue Jan 24, 2012 5:45 am Post subject: |
|
|
What's the vane endplay I should aim for? Cast iron and torlon expansion rates are fairly close.
Don't know who did the previous restoration, but the vanes that came with it had 0.3mm endplay. |
|
Back to top |
|
 |
John Moxon  Samba Moderator
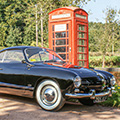
Joined: March 07, 2004 Posts: 14165 Location: Southampton U.K.
|
Posted: Tue Jan 24, 2012 5:56 am Post subject: |
|
|
skyto wrote: |
What's the vane endplay I should aim for? Cast iron and torlon expansion rates are fairly close.
Don't know who did the previous restoration, but the vanes that came with it had 0.3mm endplay. |
Sami, did you contact Dean Hedin...the guy who conducted his own experiments in 2007? I remember him writing in the old Judson Register Forum at the time about clearances but unfortunately that was lost when the old forum was discontinued.
If you could make them less than for Phenolic linen vanes it will give more boost. _________________ John.
Judson Supercharger Information on The Samba
My 1958 Shorrock Supercharged Karmann Ghia
Stop dead photo links! Post your photos to The Samba Gallery! |
|
Back to top |
|
 |
skyto Samba Member
Joined: November 24, 2003 Posts: 177 Location: Finland
|
Posted: Tue Jan 24, 2012 7:26 am Post subject: |
|
|
Did some calculations, 0.10mm endplay would still be 0.06mm at 120 celsius. Thermal expansion is about halved. Just thinking what might get ingested and the consequences with close endplay. Anyway, the vane slots are already a close tolerance.
Alright, enough of this, I'll contact him.
EDIT:
The MG Midget & Austin Healey Sprite High Performance Manual:
The clearance between the endplates and vanes is 0.015-0.020''. |
|
Back to top |
|
 |
|