Author |
Message |
jalopyjockey Samba Member

Joined: June 29, 2005 Posts: 357 Location: avl, nc
|
Posted: Wed May 24, 2006 3:17 pm Post subject: cam/valve/lifter issues once again |
|
|
hey all- heres whats goin on. i was having a problem with cold starting, and a really nasty knocking at start in the morning after running the engine for an extended period. after going thru all the fi stuff i finally decided it was somewhere in the valve train...pulled the covers and low and behold found what i had suspected...#1 exhaust lifter had lost its circlip...this happened once before on the same lifter(new lifter same position though)...which led to me rebuilding the top end to fix a dropped seat...so i get myself a new lifter, install it and run the engine gapped to .006 to get things all pumped up with fresh oil...i had good compression on all cylinders(120-130) and good vaccuum as well(around 17")...yesterday i decided to preload them 1 turn and now its a complete dog...it idles poorly and has a fluctuating vaccuum of 5-9". and now im back to where i was before the rebuild...do you guys think i should just run it gapped, zero lash or .25 in(i get good compression there and around 15" vaccuum), turn them in another half a turn, or just run it for a while and hope things work themselves out...the po had told me he replaced the cam but he also kept calling it an 1800 engine. is it possible for a solid lifter cam to fit and operate in a 2 liter...man i swear why do these things always seem to happen when i have to go 400 miles in a week. well any suggestions are gladly appreciated and hope your lucks going better than mine -sean |
|
Back to top |
|
 |
tencentlife Samba Member
Joined: May 02, 2006 Posts: 10147 Location: Abiquiu, NM, USA
|
Posted: Thu May 25, 2006 8:06 am Post subject: |
|
|
I take it it's a T4 you've got. The T4 standard and hydro cams are physically alike, either one will fit in the block, as will either type of lifter. It's not impossible you've got hydro lifters on a solid cam. I'm not sure what effect that would give you, I've never done that combo, but the principle difference in the cams is that the hydro cam has a soft initial ramp-up and back-down. I think one could run solid lifters against a hydro cam with no problem, but vice versa might cause some.
Running hydro lifters with no preload can result in losing the retaining clips. The plunger that carries the pushrod end isn't supposed to come to a stop, it's supposed to float and be cushioned within the lifter body, but with no preload it's going to come to an abrupt stop against the clip with every cycle. The clip is just not intended to take that hammering.
It sounds like they were pumped up pretty good, but as they were pumped solid, and you increased the preload, the lifters are now able to hold the valves open. But that should correct itself after a bit. Maybe wait overnight, but go out and turn the crank over 180 deg. by hand occasionally, so every valve gets to spend some time parked on the cam, so they can bleed off their excess oil. The fact that you had better vacuum the less preload you tried leads me to believe this is the case. But you need to have some preload to protect the clips, and it is important as well to keep the lifters operating in the range where they self-adjust properly.
I dunno, these things are very dynamically complex, and trial and error is the order of the day, unfortunately. If I were you, I'd probably try 1 turn preload, wait overnight doing like I said, and run it awhile before I start tearing my little remaining hair out. |
|
Back to top |
|
 |
jalopyjockey Samba Member

Joined: June 29, 2005 Posts: 357 Location: avl, nc
|
Posted: Thu May 25, 2006 12:07 pm Post subject: |
|
|
thanks for the tips on the cam differences...im inclined to say that its not a solid lifter cam as compression on cylinder 4 and 2 are pretty decent, but rather a lifter or valve spring issue...after preloading one turn i let it sit over night and then drove it around for about an hour ranging in speeds up to 60, up and down hills, and then checked compression and vaccuum...around 8-10" and 60-95 on 1, 70-110 on 3, 130-140 on 4, and 110-125 on 2...it just makes me curious that i have compression problems on the same cam lobes... maybe coincidence or that i park facing down hill and those lifter wont bleed down any. i have had it running fine gapped and zeroed so i think now im going to try it at .25 preload and see how that does...hopefully its just enough to protect the retaining clip(which i dont understand since at running temp the plunger is forcing itself into the pushrod rather than the clip even when gapped), get the compressions as close to one another as possible, and to get rid of the intake manifold leak. id rather have the engine running more balanced than to burn a valve trying to get normalized....thanks for the reply .10$ and any other suggestions would be a help-sean |
|
Back to top |
|
 |
tencentlife Samba Member
Joined: May 02, 2006 Posts: 10147 Location: Abiquiu, NM, USA
|
Posted: Thu May 25, 2006 9:50 pm Post subject: |
|
|
Seems to me that when there's lash with a hydro lifter, the thing gets filled with oil to its max volume, holding the plunger right against the clip, and it's acting like a solid lifter, like it's supposed to. Except there's got to be a bit of shock as the lash is taken up, and the internal pressure is pushing back against the clip as well without the valve spring counterforce.
Have you read this?
http://www.ratwell.com/technical/HydraulicLifters.html
This is the best article by far on the subject I've seen yet.
Weird how the back lobes aren't working as well. Could you have a difference in oil pressure further from the pump? I still think if you give them a bit more time and run it some more they'll straighten out. |
|
Back to top |
|
 |
jalopyjockey Samba Member

Joined: June 29, 2005 Posts: 357 Location: avl, nc
|
Posted: Fri May 26, 2006 9:06 am Post subject: |
|
|
it is an odd thing...im inclined to think that the lifters further from the pump would normalize sooner because of less pressure allowing them to purge ecxess oil easier...i dunno...and yeah i have seen richs article as well as anything else i could find on the subject. the lash thing makes me curious as bentley states that vw considers preload optional and that it can be run gapped to .006. when i first got the van i went thru everything in bentley to see that it was up to speck and when i got to adjusting the valves i ran into the same problem...i would go to this bug shop in virginia for parts and free advice and discussed the lifter issue with the owner...he said that many times he would run into lifters that just wouldnt take any sort of adjustment and would have to run it at zero lash...yesterday i changed my preload to a quarter turn in and it ran much better...not as good as its been before but better...vacuum increased to a 2" flutter at 15" and i increased my compression by 55 lbs on #3 and around 40 on #1...now im contemplating running #s 1 and 2 at an eigth preload, 3 at a quarter and 4 at maybe somewhere past 1 turn just to try and balance the compressions...right now it still has a problem with maintaining idle at cold start and sounds as though its laboring a bit...im thinking this is due to the imbalance...i guess well see what happens...do you happen to know what exactly can be determined with a leak down tester...for example can you distinguish which valves arent seating or will it only allow you to determine that its rings versus valves...i almost want to adjust exhaust and intake differently depending on how well each is sealing. as far as letting them go and straingtening themselves out...i have to drive 800 miles next week and im nervous about burning a valve if i let them stay open(or cause valve float)...ive driven a good bit on them and i dont see why it should take more than a 100 miles to normalize...anyways its altleast running a little better. thanks for the helpful ear $.10 |
|
Back to top |
|
 |
tencentlife Samba Member
Joined: May 02, 2006 Posts: 10147 Location: Abiquiu, NM, USA
|
Posted: Fri May 26, 2006 10:43 am Post subject: |
|
|
True, Atwell says changes should sort themselves out in about 10 min. of running, so I can see you'd be wary of making a long drive if everything isn't right. On the other hand, I just rebuilt my wbx to a 2.2 liter with a new cam and hydro lifters, and it took driving to Albuquerque and back, plus about 50 mi. of test driving while I was down there, before the engine got strong. That was over 170 mi. of driving, and those were new lifters with sano-clean oil and filter. I had another problem which was compounding things, but it seems to have sorted itself out at about the same time, and now the performance is awesome. So, like I said, trial and error, wait and see. I hate approaching engineering that way, it's not how I usually address problems which is scientifically, logical process of elimination and all, but those little lifters.....
I am on board with Atwell that there should be at least a small preload for extended running, other than having some lash for a break-in period, because of the clip issue. I wouldn't want to take a chance with one coming loose inside my mill. Your idea of a quarter-turn may be good for you. That gives you .023" of preload, enough to respond to normal expansion while keeping the valves tight.
Leakdown test is supremely useful for pinpointing compression containment. You hook up the gauge to each plug hole, and to your compressed air tank. I tells you what percentage is leaking out. A good tight engine will lose around 3% of the air normally past the rings, maybe a minute amount around the valves (they aren't a PERFECT seal, after all). If there's more you start finding out where it's coming out. You're doing each cylinder individually, so only dealing with the rings and valves on that one. You can put your hand over the exhaust tip, or over the intake throat, wait a few seconds and see if a puff of air escapes. That tells you which valve is letting air past. If it's rings you do the same on the crankcase breather hose. Of course you can do the same tests with just compressed air, but the gauge tells you how much is escaping so you know if it's not sufficiently tight. No point in tracking down leaks if they're within normal specs.
I was at Harbor Freight the other day and they had one, I don't remember how much but everything there is so cheap anyway. I was tempted, just to have it around. Maybe it'll go on sale (I doubt it). If you have a diesel this is a required tool. |
|
Back to top |
|
 |
jalopyjockey Samba Member

Joined: June 29, 2005 Posts: 357 Location: avl, nc
|
Posted: Tue May 30, 2006 6:03 am Post subject: |
|
|
thanks for all the info...yeah i been crunching the numbers as well to see what different preloads and gaps will do. is it true that the valves initially stretch and then return to their original lengths when at operating temp. the other day i set them at 1/8 turn and it still has a lack of power in the low end and has a difficult time on the cold start and idling. i drove it pretty hard for a good while and it did ok, sort of. i just set them at a tight zero this morning so i guess well see how that does...its always responded well to being gapped other than losing the circlip...maybe its time for me to invest in the leakdown and really see whats going on in there...there is also the other issue that i recently removed the cat(it went south so i smashed the comb out of it) and im thnking that maybe part of my problem is from the lack of backpressure/backfiring/valve warpage...well at least i got new cabinets for it finished this weekend |
|
Back to top |
|
 |
tencentlife Samba Member
Joined: May 02, 2006 Posts: 10147 Location: Abiquiu, NM, USA
|
Posted: Tue May 30, 2006 8:08 am Post subject: |
|
|
I've never heard that about valve shrinkage, but it makes no sense. They're solid steel, so like everything else in the motor they will expand in every dimension when hot and shrink back when cool. Physics, y'know. There is some permanent stretching in the stem after some heat cycling with new valves, and minute amounts more as engine hours accumulate, but it is very small and doesn't retract.
You don't need the backpressure the cat provides. I run with no cat at all, and my valves are working nicely, thank you very much. Backpressure is mainly about not letting the still-burning exhaust gases escape at such high speed that they burn the rim of the valve. When gases speed up around an obstruction they expand (this is how an airplane wing generates lift), but when you expand a gas, it becomes hotter. Once again, physics, y'know. But a little backpressure is sufficient to prevent this if mixture is within a reasonable range. Backfiring and warpage are caused when you have an exhaust leak right at the head port, and pressure fluctuations pull some cool fresh air into the port.
I don't think the leakdown is going to help you much with these valve dynamics. To do it right, you almost want to relax all the valves or remove the rocker gear on engines like ours, so that you don't get confused because a cylinder with valves on the overlap is next to one with a leaky intake, for instance. If you're looking for small leakage you kind of need to isolate the cylinders that way. Plus hydros don't open accurately at hand-turning speeds or statically, unless they're pumped up solid, but if yours were you wouldn't be having this problem. Didn't you say you rebuilt the heads already? You shouldn't have any problems there if you did, and you already know your rings and valves are good because you already had a good compression test when you had .006" lash.
When you set the valves, are you sure you're setting each pair at firing TDC? Sorry, dumb questions, but gotta make sure. When you are at TDC, and you back off the adjusters 'til there's lash, how do the lifters feel? Pushing on the lower rocker end, are they spongy? They should be solid, not able to be compressed, and when you add preload, the valve should be seen to open. If they're still spongy, or some are (more likely), then you gotta figure out why they're not getting pumped up. Do you have good oil pressure? Maybe try a lighter grade, new filter, bla bla bla. At this point I don't think I can add anything helpful that you don't already know.
Maybe you have a solid cam in there, and they need the longer ramping of a hydro cam to work right. I have trouble with this notion, since in Atwell's article he points out that it's the inertial reaction that makes the ball pop off the seat for an instant when the lifter starts to climb the lobe that lets more oil into the lifter if there's room, just at that instant before valve spring pressure builds up and shuts it off with reverse inertia. I would think a sharper cam rise would amplify this effect. But maybe it gets it open too much in that case (there's gotta be a reason hydro cams are ground differently), and the valve spring is actually able to make oil escape the lifter and go flatter before the ball gets back on its seat. If that were true, then more preload on the plunger spring would be your friend. Are you using heavier valve springs?
Good luck. Done that 800 mile trip yet? |
|
Back to top |
|
 |
jalopyjockey Samba Member

Joined: June 29, 2005 Posts: 357 Location: avl, nc
|
Posted: Tue May 30, 2006 1:35 pm Post subject: |
|
|
as far as the valves initially stretching and then returning comes from kenneth ball's book on the t1 engine...im not sure where he gets his info but sure enough i read it just the other night...i didnt think the lack of backpressure could have anything to do with my issues but when i saw the other post on backfiring it got me to thinking about valve or seat warpage...once you start to get stumped you begin to believe you might need to change your turn signal fluid...as far as setting the valves...assuming the po installed the cam timed properly with the crank im good...my fan is clearly marked and when im feeling particularly anal i pull the plugs and watch the pistons reach tdc...i agree with you on richards description on how the check ball works...if a solid cam were causing the lifter to lose oil my compression would raise...as far as the valve train goes i would be inclined to say that its all stock although i have no way of knowing for sure...i could have rockers with a different ratio and a mismatch of different springs...one of the heads is using springs that are from a salvage vehicle(the head number is right but who knows about the springs)...ive often thought mine might be weak...the vacuum readings slighly indicate this...or it could also be saying its worn valve guides, or it could just be from an engine out of balance because the valves arent adjusted properly... i find the worn guides hard to believe when everything was well within spec 2000 miles ago when i had it on the workbench...so that leaves me back at square 1...im now starting to get the itch to buy a new motor so that i can tear this one all the ay down and see whats goin on in there...maybe first ill just get som solid lifters...oh do you know, if i were to do that wold i have to replace my pushrods as well...anyways, i leave on thursday evening and ill have enough tools and parts with me to fix darn near anything that could occur; but some additional luck never hurts, thanks and ill let you know my progress |
|
Back to top |
|
 |
tencentlife Samba Member
Joined: May 02, 2006 Posts: 10147 Location: Abiquiu, NM, USA
|
Posted: Tue May 30, 2006 2:07 pm Post subject: |
|
|
Well, I got a whole case of that turn signal fluid settin' on the shelf. Got a good price on it awhile back, but didn't need it as it turned out. It's still pretty fresh. I'll give ya a real good price if you take it all....
Good luck on the trip. |
|
Back to top |
|
 |
jalopyjockey Samba Member

Joined: June 29, 2005 Posts: 357 Location: avl, nc
|
Posted: Wed May 31, 2006 5:43 am Post subject: |
|
|
well its either that or maybe i need to change the air in my tires, new muffler bearings....well i went and set the valves at the tightest zero i could get with my fingers...those edges on the slot really can do a number on your finger tips...i havent done a compression test but it seems to have the pep back and the fuel pickup seems smoother...im still having the cold start issue which just started when i replaced the afm...i havent swapped back to the old one to see if thats the problem so who knows...maybe the mixtures a little too lean...the vw shop up here told me that the new ones are factory set and i shouldnt worry about adjusting it...the plate in the new one did seem to have alittle more resistance like the spring were stronger but i dont think thats the issue...er maybe it is a combination of the two...not running strong enough and shutting off the fuel pump...im gonna try and stop in the shop and get the mixture checked before i leave, hopefully thatll get the bugs worked out...do you get any sort of exhaust popping/backfiring since your not running a cat...im wondering if i blew a whole somewhere when the cat went bad since i get backfiring in overrun and when shifting on occasion...well time to make the donuts |
|
Back to top |
|
 |
tencentlife Samba Member
Joined: May 02, 2006 Posts: 10147 Location: Abiquiu, NM, USA
|
Posted: Wed May 31, 2006 8:00 am Post subject: |
|
|
Backfiring?absolutely never. If your exhaust flanges aren't leaking at the ports, then you have an overrun problem. I don't know the year of your van, but I assume it's an 80-83 T4 AFC-FI.
The AFM doesn't even work during starting and idling, so it can't be your starting problem. And if your O2 sensor is working the CO setting on the AFM has very little effect anyway, so your mechanic is right, leave it alone.
Test ALL these items per Bentley:
Decel valve 24.7
Head temp sensor II 24.13
Thermo-time switch 24.6 (don't miss this one, they fail all the time)
Cold-start valve (5th injector) 24.5
I'm finding that the EEC sys is contributing to a lot of the starting and idling problems with these vans, due to excessive wear in the throttle bodies. It's barely mentioned in Bentley (20.3 and 20.16 show schematics). Since you have a vacuum meter, you can see if this is giving you trouble. Check for vacuum at normal idle on the distributor vacuum advance line, which is the same signal as the purge valve gets. If you have 1mm Hg., and your throttle basic stop is set correctly, then you'll need to get a tighter TB. I can describe how I did cosmetic surgery on mine with JB weld and got it nice and tight again. The starting and idle are now perfect! It's an amazing difference.
You can test the O2 sensor with a VOM between the unplugged connector and ground, warm engine. At any steady speed it should produce a voltage of 0.7-0.8V if CO is within range. You can actually tune CO reasonably well using this. While you have it disconnected, slide the rubber cover up the ECU signal wire aways. You'll see that the O2 sensor signal wire is actually a coax cable. Make sure that the shielding braid is continuous to ground, and not to the signal wire. Make sure the frayed braid wires can't contact the signal wire, and trim them back to make sure.
Do these checks so you can rule them out at least, but chances are you'll see improvement in your FI performance. Let me know if you want to do the fix on the TB, I'll tell you how. |
|
Back to top |
|
 |
wolfej1 Samba Member
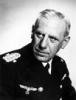
Joined: August 15, 2005 Posts: 679 Location: North Royalton, Ohio
|
Posted: Wed May 31, 2006 8:25 am Post subject: |
|
|
Quote: |
I can describe how I did cosmetic surgery on mine with JB weld and got it nice and tight again. |
Tencentfile - can you elaborate on your issues with the TB and the associated fix? _________________ 1982 Westy
2004 KDX200
2008 Kawasaki KLR 650
1979 Yamaha DT 175
1995 Toyota 4Runner |
|
Back to top |
|
 |
tencentlife Samba Member
Joined: May 02, 2006 Posts: 10147 Location: Abiquiu, NM, USA
|
Posted: Wed May 31, 2006 9:24 am Post subject: |
|
|
Sure. I think most of these old vans can benefit from fixing the wear in the TB.
While it's still in the car you can get an indication of this by how far in your idle bypass screw has to be set to keep idle down to 800rpm. Mine was like half a turn. If you take out your TB and hold it up to the light, you'll probably see plenty of light around the butterfly. By the way, on a Digifant, it's a lot easier to get the TB switch set just right by removing the TB and doing it on the bench, and this is a very critical setting for that injection. But they all have EEC (Evap. Emission Control) and if it isn't working right I believe it has a lot to do with the erratic idle and especially warm starting problems you get when you park for a little while.
So you want to make the butterfly a tight fit again when it's closed. Mix up about two nickel-sized blobs worth of JB Weld. Clean the inside of the TB really well with Brakleen, and if you want you can rough up the bore with some medium grit paper to get really good adhesion. Run the idle bypass screw in all the way. Get it all very clean and dry afterward. Adjust the basic closed position by backing out the stop screw and running it in 'til it just touches the stop, plus 1/4 turn. Then carefully apply a light smear of grease to the trailing edge as it opens of each side of the butterfly, right around to as near to the cross shaft as you can get it without getting ANY on the body itself. The grease is so the JB won't adhere to the butterfly at all. Grease the tip of the idle bypass screw as well. You're going to form up a thin stop of epoxy right against the butterfly itself when it's closed, just like the wooden stop around a door frame. If you have a very thin putty knife or something similar you should use it as an applicator. I used a 3/4" wide strip of some thin stiff cardboard, folded over lengthwise for stiffness.
So with the butterfly closed spread a thin layer of JB around 1/2 of the bore right against the face of the butterfly where it comes to a stop. You can make it about 1/8" thick right up against the butterfly, and feather it back for maybe 3/4". Since there are two trailing edges of the butterfly, of course you'll be doing each side from opposite ends of the TB. One side of the butterfly is a wedge shape and it's a bit trickier here, but go ahead and work the epoxy right down in the gap under the wedge. Be sure you greased in there. Don't worry about putting on too much, you're going to file it away after it sets. Wipe off the excess, especially if there's any on the sealing taper of the TB so you don't have to file it off later.
I stood the TB on end with the wedged side up so the epoxy would flow down into the gap better, but flipped it after awhile to assure the other side didn't flow away. Just monitor the flow of the epoxy for awhile and turn over the TB as needed until it firms up. You can test the remainder of your mix for firmness without touching your work, so don't throw it in the trash yet. Don't open the butterfly at all until the epoxy is fully set. Don't worry, if you greased it carefully it will come free.
Wait overnight, and open the butterfly. It'll break free of the JB. Clamp the lever open with a small C-clamp. Using a half-round file and/or a Dremel with a small drum sander on it, shape down the epoxy ridges you formed until they're smooth, nicely feathered down to the inner surface of the TB bore, and most importantly until you have left about a 1/16" stop that each edge of the butterfly come to rest against when closed. On the wedged side, the stop will be tapered to match the wedge shape closely. The forming should have taken care of that part, you'll just do the feathering back. A ight hand sanding will finish making it smooth, and blow it all out good with compressed air.
Hold it up to the light again and you should see very little light around the edges anymore. This means that there won't be vacuum at the EEC control valve port at idle, so it won't be drawing air thru the charcoal canister with its varying concentration of gas fumes, and you'll be much better able to set and control idle speed and CO.
Let me know how it works out. |
|
Back to top |
|
 |
jalopyjockey Samba Member

Joined: June 29, 2005 Posts: 357 Location: avl, nc
|
Posted: Wed May 31, 2006 1:23 pm Post subject: |
|
|
thanks for the suggestions...when i say it has a hard time starting i mean it fires right up but then quickly fades unless i press onthe accelerator a bit and then will idle fine when its up to running temp...maybe its just coincedence that the problem occurred when i got the new afm...ive been thru the ts2/thermo time/cold start/aux air reg....and all work properly...the only exception might be that i adjusted the aux air reg so that the valve is as open as it can be however it still closes completely...also no o2 sensor...no egr...ill check the dizzy vacuum and see what it does....what do you mean by an overrun problem...as per the exhaust flanges i retorqued them last night and everything was right on with fairly new gasket however i didnt run it while i was under there so im not sure if theres a leak...well i gotta run to get myself organized for the trip and check some more things out...oh yeah its an 80 t4 afc fi....thanks for all the help once again-sean |
|
Back to top |
|
 |
tencentlife Samba Member
Joined: May 02, 2006 Posts: 10147 Location: Abiquiu, NM, USA
|
Posted: Wed May 31, 2006 2:34 pm Post subject: |
|
|
edited. see next.
Last edited by tencentlife on Wed May 31, 2006 2:43 pm; edited 1 time in total |
|
Back to top |
|
 |
tencentlife Samba Member
Joined: May 02, 2006 Posts: 10147 Location: Abiquiu, NM, USA
|
Posted: Wed May 31, 2006 2:42 pm Post subject: |
|
|
By overrun problem I meant that you should do the test on the decel valve. If you have a non-California manual trans car, it should have one. It helps to lessen backfiring on sudden throttle closure at hi revs. To get backfiring from just an exhaust leak, it has to be a pretty big leak. Of course with your lifters, we're still not positive your exh. valves are closing all the way, but let's assume they are allright with the new valve settings.
I thought you had an O2 sensor but you're right, in those years only Cali cars had it. My bad. Yours should have had EGR, but by now all those have been removed I thought, so I didn't mention it.
And on a closer look at the book I see that your EEC sys isn't likely to be your idle problem since the earlier ones attached the charcoal canister line to the air filter box, upstream of the TB. Although that can still throw mixture off some if it's open at idle, but it's more likely to be noticeable with hot starting. Try clamping it off and cold starting. I haven't worked on an earlier AFC in so long my memory is a bit foggy. I just fix my own car anymore. But you can check vacuum at the dizzy anyway to make sure your adv/retard signals are correct.
Good trip! |
|
Back to top |
|
 |
jalopyjockey Samba Member

Joined: June 29, 2005 Posts: 357 Location: avl, nc
|
Posted: Wed May 31, 2006 5:07 pm Post subject: |
|
|
yeah ill try pluggin the line at the air box from the charcoal canister and see what happens...if it changes anything does that mean a leak somewhere from the airbox to canister or from the canister to the expansion tank mumbojumbo...wow i hope it would be something that easy...hoses are cheap and sometimes duct tape works just as well when your in a rush. as far as the egr goes it did have one but the po had the elbow from the crossover rust out on him and he did a cheapy fix thus removing the egr filter, its since been covered at the plenum and i detached the connecting rod from the tb...anyways i swapped out the afm and no change..searched for air leaks...no luck...i adjusted the aar so that its slightly more closed, maybe a slight change but really no improvement...im gonna check the decel and dizzy vac tonight as well ...maybe it jsut wants to stop trotting around and get up to a full gallop for a little while to knock all the cobwebs loose...wouldnt that be nice...thanks for all the help...every time ive brought this up in the past people seemed to get wearisome of the lack of improvement...with all this climbing around underneath and hunched over the back itll be great to remind myself how much i enjoy driving it |
|
Back to top |
|
 |
tencentlife Samba Member
Joined: May 02, 2006 Posts: 10147 Location: Abiquiu, NM, USA
|
Posted: Wed May 31, 2006 10:43 pm Post subject: |
|
|
Yeah, when you're deep into a problem and the solution is elusive, if it actually runs it's probably good to just go out and drive around a bit to remind yourself why your back hurts and your hands are bleeding and you've trashed ANOTHER set of clothes. Maybe give it an Italian tune-up and see if you can blow the shit out of there.
Sounds like it got the standard treatment on the EGR sys: hack that crap off, plug the holes and never let me see it again!
What I was getting at about the EEC charcoal canister is that with the age of these cars all the TB's are worn, so there's a vacuum signal at idle when there shouldn't be, which holds the purge valve open at idle, letting extra air in from the canister past the butterfly on the late model cars, but on your earlier AFC it would only be letting extra air into the air cleaner box. That won't throw off idle speed per se, because it's before the butterfly, but the extra air will sometimes be laden with gas fumes from purging the canister which could throw off the idle mixture somewhat. But I really don't believe it would upset the idle cold, since a cold engine likes extra enrichment at idle. It's possible though. I haven't experimented to see if that's the case.
I do think it could upset a hot idle mixture enough to cause hard starting and poor idling on a hot restart, when the engine wants a much leaner mixture. So I'm not saying there are big leaks in the lines, just that the system may be operating at idle, when it should only operate above idle. Plus the same idle vacuum signal from the worn TB may be advancing the timing a bit, or canceling out the retard, but in my experience motors aren't so sensitive to small changes in timing that they won't idle, they'll just idle at a different speed.
Hope that clarifies the matter some. I have to say I'm about out of ideas myself. |
|
Back to top |
|
 |
jalopyjockey Samba Member

Joined: June 29, 2005 Posts: 357 Location: avl, nc
|
Posted: Sun Jun 04, 2006 3:58 pm Post subject: |
|
|
whew...i made it...kinda nerve wracking for a bit there but i was finally comfortable enough to turn on the music 6 hours in...the trip was great excluding losing a windshield wiper in a storm...the oil gettin thrown all over the place and the typical starter issues....so heres the low down, before headinng out i checked the dizzy vac(0 at idle but starts to register somewhere around 100 rpms i think), the carcoal canister(no change with it disconnected and plugged), and the decel valve(theres suction i guess...i feel something but im not sure if its as strong as it should be...any ideas how many " hg this thing should pull...youdda thunk bentley would be wise enough to quantify the test)...after all that i got on the road...with all the same issues...on the 1st tank i put in 93 and got ~18 mpg(there was some stop and go though), the 2nd was 87 + techron and i got ~19 mpg, the third tank was only 87 and i got ~21 mpg(not too shabby for an engine that sounds like a sick locomotive), im not sure yet on the 4th tank...it was 87 and felt as though it might be around 23 mpg. at the moment its running so i just dont feel like dealing with valves and cold starts but rather this idea that i just remembered i think alot about while driving distances....my brother was driving a 450 aircooled motorcylce on a major interstate and like lots of other drivers(i do this all the time) he tucked in behind a semi to get pulled along as well as have someone block the wind for him...however because of doing this the engine overheated and seized and got left on the side of the road....has anyone ever heard of this happening with vws... ive been trying to figure out which is better or worse...beating the engine up fighting a headwind or losing some of its cooling air...also does anyone have suggestions about why on long trips the van always likes to throw oil all over the engine compartment...ive replaced the rear(pulley) seal twice and it never fixes it....am i overfilling because of a short dipstick or is the breather not doing its job...im thinking i should figure this one out in the summer so i dont go blowing that oil stink into my heater hoses....well time to take a good sit...amazing how you want to sit after just having sat for so long(thats kinda funny sounding now that i reread it)...good to be back-sean |
|
Back to top |
|
 |
|