Author |
Message |
Motomazzo Samba Member

Joined: June 02, 2009 Posts: 792 Location: Texas
|
Posted: Tue Jun 09, 2009 1:33 pm Post subject: Dimpling Torsion Bars for Narrowed Beams |
|
|
Hey All,
I narrowed my front beam 4". I have looked and all I have seen are narrowed torsion bars for only 2" jobs. Does anyone have any advice on dimpling their own? I have seen pics on the internet....looks like the dude has them chocked up in a drill press vice, about to go to town with a countersink. I just don't know what angle countersink....what type of countersink, etc. I know those leaves are spring steel and hard as a rock. If you have done this before, please let me know any information you have!
Thank you!! |
|
Back to top |
|
 |
50ate Samba Member
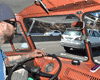
Joined: September 22, 2007 Posts: 1171 Location: PNW
|
Posted: Tue Jun 09, 2009 2:01 pm Post subject: |
|
|
i just take them tape them up good so they dont move around.. then put them in the vice on the drill press and slowly drill the dimples out i think i used a 1/2 in bit or whatever size i read to use (cant remember) oiled them up a bit and just go slow should be cake.. They ended up looking just like the ones i cut off |
|
Back to top |
|
 |
VIN Samba Member

Joined: June 01, 2006 Posts: 941 Location: phoenix
|
Posted: Tue Jun 09, 2009 5:12 pm Post subject: |
|
|
they are easy to drill, but i used standard bit, and the angle is different. they are working thus far, but its in the back of my mind. i couldnt find what to use, either. |
|
Back to top |
|
 |
Culito 11010101
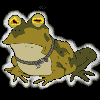
Joined: December 07, 2006 Posts: 5878 Location: Columbia Missourah
|
Posted: Tue Jun 09, 2009 5:18 pm Post subject: |
|
|
There is a tutorial on Airkewled's site about doing this. I'm too lazy to search for it, though. _________________ © CJ Industries, Inc.
'64 standard w/2.0L type 4
'62 bug
johnnypan wrote: |
...dont pay no attention to Culito,he's a cornhole.. |
|
|
Back to top |
|
 |
BUGTHUG Samba's Rented Mule
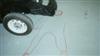
Joined: April 22, 2007 Posts: 833 Location: KANSAS toto's fire hydrant
|
Posted: Tue Jun 09, 2009 5:22 pm Post subject: |
|
|
I haven't done this, but I would say it needs to be the same size and angle as the grub screw that goes in it. _________________ I know you would understand what I'm saying if you could just see my HANDS
Even the middle of the week says W T F
1963 15 window bus
1966 VW bug
1966 21 window micro bus
1969 Dune Buggy
1965 VW bug
1974 VW bug
1972 Kelmark, VW drive line
1948 Chevrolet Hearse |
|
Back to top |
|
 |
50ate Samba Member
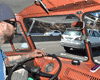
Joined: September 22, 2007 Posts: 1171 Location: PNW
|
Posted: Tue Jun 09, 2009 5:50 pm Post subject: |
|
|
the tech article tells you what bit to use there is also one on CW.. the taper is fine for the bit i used and i really wanna say it was 1/2 or 5/8 |
|
Back to top |
|
 |
Joey Samba Member
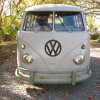
Joined: August 12, 2005 Posts: 5375 Location: Nova Scotia - Canada
|
Posted: Tue Jun 09, 2009 5:52 pm Post subject: |
|
|
When I did my beam I first drilled a 1/8" pilot hole and then used a 90º countersink bit.
_________________ Joey
‘60 Kombi - '74 Bus - '79 Panel - '65 Beetle |
|
Back to top |
|
 |
Reaper Samba Member

Joined: March 27, 2008 Posts: 249 Location: Olympia, WA.
|
Posted: Tue Jun 09, 2009 10:15 pm Post subject: |
|
|
Don't remember the size of the bit I used, but what I did was grind the tip of the bit on a bench grinder, until it matched the angle of the grub screw tip. Cheap, and all I did was sharpen the bit when it went dull. Make sure you use some kind of lubricant to help the bit chew thru the steel.
-Keith |
|
Back to top |
|
 |
Motomazzo Samba Member

Joined: June 02, 2009 Posts: 792 Location: Texas
|
Posted: Wed Jun 10, 2009 11:29 am Post subject: |
|
|
56ovalbug wrote: |
When I did my beam I first drilled a 1/8" pilot hole and then used a 90º countersink bit.
|
Thanks for the replies, guys. Hey 56ovalbug, do you remember how close the 90 degree countersink was to the original dimple angle? any special hardened countersink, etc? |
|
Back to top |
|
 |
Joey Samba Member
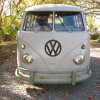
Joined: August 12, 2005 Posts: 5375 Location: Nova Scotia - Canada
|
Posted: Wed Jun 10, 2009 5:55 pm Post subject: |
|
|
The 90º countersink bit I have is spot on with the angle of the original dimples and grub screws. When I bought mine it just said for metal on the package. Though, without the pilot hole the countersink bit does nothing. _________________ Joey
‘60 Kombi - '74 Bus - '79 Panel - '65 Beetle |
|
Back to top |
|
 |
Mr. Unpopular Samba Member

Joined: September 20, 2005 Posts: 3715 Location: Tampa Florida
|
Posted: Thu Jun 11, 2009 6:29 am Post subject: |
|
|
Where did you buy your countersink bit at? _________________ "In any racing engine, the nearer you are to it disintegrating, the better it's performance will be"
-Keith Duckworth, creator of the Ford/Cosworth DFV |
|
Back to top |
|
 |
Motomazzo Samba Member

Joined: June 02, 2009 Posts: 792 Location: Texas
|
Posted: Sun Jun 14, 2009 8:55 pm Post subject: |
|
|
Hey Guys,
I know this is probably not the hottest topic ever, but I thought I would give a quick update. Turns out, I had a 3/8" 90 degree countersink in my shop all along. The OG countersink looked to be about 1/2", but I went with it. A little preparation, and careful measuring and my torsion bars are dimpled like new. I narrowed my beam 4" and completed dimpling the bars today and I couldn't help but stand back and be really happy with the fact that I saved myself close to 500 bucks just doing a little fabrication. I cleaned the front end all up and POR 15'd it. Looks sweet. Just a word of advice for anyone who might be doing their own beam/torsion bars because I haven't seen anyone mention it: When you get ready to dimple your torsion bars, I would recommend installing the leaf springs in the front end, installing the center grub screw, putting the seals on the ends of the front end tubes, then installing the trailing arms. This allows you to mark the location for the dimple through the grub screw hole in the trailing arm. This takes into consideration the width of the beam seals on the ends of the beam. There is a fair amount of error from using chopsaws, etc. when cutting the beam/leaf springs etc. and looking back now.....had I just cut down the torsion bars and dimpled them from the ends the same amount as stock, I would have been off enough that the trailing arm may or may not have been firm up against the front end tube seals when I reassembled everything. This may be common knowledge to everyone, but I if not, I thought I'd share. Hope this makes sense/helps somebody. I'll try to post a pic of the finished product when I get everything re-assembled. |
|
Back to top |
|
 |
|