Author |
Message |
Christopher Schimke Samba Member

Joined: August 03, 2005 Posts: 5530 Location: PNW
|
Posted: Thu Jan 21, 2010 11:18 pm Post subject: DIY Wheel Alignment |
|
|
I decided that because we cannot edit our posts after a certain amount of time has past and because I kind of botched up the original post by not including the caster as the beginning of the alignment sequence, I would just start a new post that lists the complete alignment sequence in order so that it is easier to understand than a broken up piece. Most of this is just an edited version of the original with the new material added in the proper place. Here is the link to the original if anyone needs it for anything.
http://www.thesamba.com/vw/forum/viewtopic.php?t=375963
tschroeder0 wrote: |
Hi all,
I just finished up a total front suspension rebuild. It all turned out well. The van goes down the road very good, with the exception of a slight pull to the left(drivers side)
My question is are there any generic measurements/adjustments that can be made prior to an alignment...I'm also thinking if I had a bit more knowledge I may not need to get one.
FYI, I put all the adjustable parts back to the prior measurements with the exception of the rods that go from the lower control arm to the front bulkhead ( the new bushings prevented this, so I snugged them and made them even) |
In response to tschroeder0's question about what alignment operations can be performed at home, I decided to do a little piece on doing a complete alignment at home. I did not invent any of these procedures, but they have been time tested and depending on how much attention is paid to the details, it can actually be more accurate than an alignment done at a professional shop, and can definitely be more accurate than an alignment done by someone who neither cares nor knows about the specifics of the Vanagon. The added benefit is that once you know the ins and outs of the procedures and have established a good baseline alignment for your self, you will be able to do little tweaks to your settings to suit the needs of your van and not have to rely on someone else to do it for you.
I have performed these procedures many times with excellent results. A handful of years ago, I got lazy and didn't want to deal with the alignment that my van needed, so I decided to "treat" myself to a professional alignment. After MUCH frustration and a couple of different alignment shops, I finally found one shop that did a halfway decent job, although it was not anywhere close to perfect. I have resorted to doing it myself from now on.
There are many adaptations and interpretations of these procedures and each one has its own level of accuracy as well its own level of complication. The more attention you pay to the details, the better your results will be, regardless of how complicated (or not) you choose to make your set-up. This is the way that I do it, but there is definitely room for modification and/or improvisation.
Since the Bentley manual does a fine job of showing you what to adjust in order to achieve the alignment specs, this article is only meant to give you an insight into the specifics of the set-up involved in doing an alignment and the tools needed for that set-up as well as how to interpret the specifications spelled out in the manual and is not a full step-by-step alignment how-to.
TERMINOLOGY -
Alignment of the front of the Vanagon is comprised of three main specifications - caster, camber and toe.
Caster angle -
The angle of the axis between the upper and lower ball joint, as viewed from the side, relative to 90º from earth, expressed in minutes, degrees inches or millimeters. If you imagine a line drawn through the upper and lower ball joints, the difference between this line and a line drawn 90º to earth is the caster angle. Caster pointing toward the rear of the vehicle is considered positive while caster pointing toward the front of the vehicle is considered negative.
Negative caster angle makes the steering light but causes the vehicle to wander. Positive caster angle makes the steering heavier but also makes the vehicle track straighter. If the caster angle is different from side to side, the vehicle will pull to the side with the lesser amount of positive caster angle.
Camber angle -
The measurement of the inclination, or tilt, of the front wheels, when viewed from the front, relative to 90º to earth, expressed in minutes, degrees, inches or millimeters. If the wheel(s) are pointing straight up, camber is described as zero. If the wheel(s) tilt inward at the top, camber is described as negative. If the wheel(s) tilt outward at the top, camber is described as positive.
Negative camber promotes tire wear on the inside edge but can also increase positive handling characteristics. Positive camber promotes tire wear on the outer edge of the tire and diminishes the positive handling effects of the suspension.
Toe angle –
The difference in the distance between the front of the tire and the rear of the tire, measured in minutes, degrees, inches or millimeters. Incorrect toe angle can lead to excess tire wear and poor handling. When the measurement at the front of the tire is less than that of the rear, it is considered toe in. If the measurement at the front of the tire is more than that of the rear, it is considered toe out.
Those are the points that we will need to address and adjust when doing an alignment, but there is one other bit of information that we need to be consider and/or address when doing a basic alignment.
Thrust Angle -
Thrust angle is the collective direction that the rear wheels are pointed relative to the centerline of the vehicle. When the collective direction of the rear wheels is pointed straight ahead, thrust angle is said to be zero.
However it is possible for the collective thrust angle of the rear wheels to be pointing either left or right of the vehicle's centerline. When this occurs, the vehicle will want to go down the road sideways. Have you ever seen those pickup trucks that "crab" down the road? That is caused by the rear axle (and thus the rear wheels) pointing out away from the vehicle's centerline. Thrust angle will be mentioned again once we get into the set-up phase.
The proper sequence for doing an alignment is first caster, then camber and lastly, toe. The reason for this is that changing the caster can also change both the camber and the toe settings. Changing the camber can change the toe settings, but will not have an affect on the caster settings. Toe is always left for last since changing it does not have any affect on either the caster or the camber. In the following examples, I will always refer to the vehicle load as "empty" when referring to the specs described in the Bentley manual.
PREPARATION -
The first order of business is to be sure that your vehicle is ready for an alignment. Worn or loose components all need to be addressed prior to doing an alignment. I don't think that I need to tell you that doing an alignment on a vehicle with worn or loose components is not only a waste of time, but it will also yield inaccurate results. Tire pressures must all be checked and adjusted to specs if necessary.
Once the vehicle is ready, you will need to provide a nice level area for your alignment procedures. Doing an alignment on an uneven surface will lead to false readings. Although garage floors seem relatively flat, there is usually a fair degree of slope in at least one direction. To compensate for any uneven ground and to be sure that the vehicle is positioned on as level of a surface as possible, you can use 12x12 floor tiles or 12x12 Masonite to shim the areas of the floor in which the vehicles tires will be sitting. To demonstrate how to perform this leveling procedure, I have chosen to show you how it is done using my driveway as a semi-extreme example.
Position the vehicle where you want to do your alignment and mark the spot where each tire makes contact with the ground. A sharpie, tape, chalk or whatever will work fine, just as long as you have a reference point for where each tire sits on the ground.
Now you will want to roll the vehicle straight backwards away from the marks. The reason for moving the vehicle backwards, rather than forwards, is that when you move the vehicle forward into position again (you will see what I mean by this in just a minute), any tiny movements in the suspension components (flex in the rubber bushings included) will be taken up and the suspension components will be in nearly the same position as they are when you are traveling down the road.
With the vehicle out of the way, place two shims of whatever stock you choose (I use 12x12 floor tiles) in the exact positions where the tires will sit. Use your marks that you made previously to position your shims. The reason for two shims in each position will become clear shortly.
With two shims placed at all four tire positions, it is now time to find the highest point of your chosen location. To do this, I use a water level consisting of colored water, a bucket, some clear tubing and a carpenter's square.
With your bucket containing at least one inch of colored water, make sure that the height of the water is such that it comes to at least the midway point of your carpenter's square. I raised my container up to achieve this.
Tape one end of the clear tubing into the water and secure it (duct tape) so that the end of the tubing remains submerged.
Attach the opposite end of the clear tubing to the top of the long end of the square with duct tape and then attach the tubing to the square at the opposite end of the square (about 6-8 inches below the height of your water line) so that the tubing runs along the numbers on square and so that the numbers can be seen.
With the end of the square sitting on the ground next to your container of water, you can suck the water into the tubing (by mouth - be sure your water and container are clean) until it is higher than the level of the water in your container.
If you have done this correctly and there are no air bubbles in the tubing, the water level in the tubing will drop to match the exact height of the water level in your container.
With the water level created, you can now place the end of the square in the middle of each of your shims to determine which location is the highest. Remember that the highest location will read the lowest number on the square. My highest location (left front) measured right at 15" on the square and my lowest location (right rear) measured 16 1/4".
Using the 1/8" thick tiles, I stacked them in the three lowest locations until I achieved a level of 15" on the square of my water level at all four locations. Since the tiles are 1/8" each, it was very easy to figure out how many were needed for each location.
Remember that I mentioned placing at least two shims in each tire location? This allows the last tile to swivel on the one underneath it as well as lets the suspension settle easier should you need to jack up the vehicle for access to the suspension components while adjusting things. Being able to rotate the wheels during the caster adjustment procedure is where this comes into play the most.
To reduce the friction between the last two sets of tiles, I use a little talcum powder on the next to the last tile. I have heard of people using grease, vegetable oil, salt, wax paper, etc. Whatever it takes to reduce the friction is fine.
You now have a level surface worthy of doing your alignment on. It's now time to position the vehicle onto your leveled surface. If you only have a few tiles, like I do on the front, it is probably okay to simply drive the vehicle up onto them. However, if your stack is large, like my rears, it is much safer to move the tile stack, position the vehicle next to your marks, jack up the vehicle and place the tile stack under the tire. With the last two tiles lubed, it is very easy to shoot a tile or two out from under the tire while trying to drive up onto them. A flying tile could really cause some damage or seriously hurt someone. Please be careful.
When positioning the jack under the vehicle, it is best to use the control arm as your jacking point. This keeps the suspension loaded while lifting the wheel/tire off of the ground and minimizes any settling of the suspension. Keeping the suspension loaded is important to achieving an accurate alignment.
Now that you have the vehicle all nice and leveled, we can attack the actual alignment procedures. Before proceeding to any of the actual measurements or adjustments, be sure that you load your van in such a way as to represent its typical road going position. For example, at the very least, the van should be half full of fuel and you will want to add weight to the driver’s seat to represent the driver. You can carry this as far as you like really. Just make sure that you present an accurate state of the vehicle on its typical day.
CHECKING CASTER ANGLE -
To check the caster in this example, I am going to be using a tool made by RPW. It only costs $39.99 (in Jan.2010) and can check camber and caster angles. This tool is plenty accurate for our usages and will net you an alignment worthy of a high dollar alignment shop…and probably better than some. The operation of the tool will be described later.
http://www.racerpartswholesale.com/product/1934/Caster_Camber_Gauges
The first order of business is to have the vehicle on your leveled pads with the front wheels positioned facing straight forward. If you are confident that you can get the wheels pointed straight ahead using only the steering wheel as your reference, fine, however accuracy pays off here so I would suggest that you set up the string jig as described in the toe section (below) so that you can accurately position the wheels so that they are pointing absolutely straight forward. If you choose to set up the string jig to get the wheels straight, it’s probably best to temporarily remove it to complete the caster and camber work. The string can tend to get in the way and make it difficult to work on the vehicle. If you mark all of the positions of your string jig and don’t move the vehicle, you can put the string jig back into place and not have to go through the entire set-up procedure again, although you should do a quick check just to be sure that nothing has moved.
Once the wheels are facing straight forward, you will need to use something as a straight edge that is tall enough that it will sit up against the tire’s sidewall about 6-10” up from the ground and is long enough that it will give you an accurate measurement. The piece that I used here is a chunk of aluminum plate that measures 6” tall and 23” long. A 2x6 or 2x8 would work well as would a short section of wood shelving.
Place the straight edge up against the tire making sure that it makes contact evenly with both sidewalls. The bulge at the bottom of the tire will prevent the straight edge from standing 90º to the ground, but as long as the upper edge is making contact with the tire evenly, you are good to go.
I used masking tape to mark the ground with a straight line the length of the straight edge. You could use chalk, permanent marker, or whatever gives you a clear line.
Then you will need some type of tool that will help you indicate 20º to the first line on the ground. I used a 12” plastic angle finder. Turn the front wheel until the wheel is 20º to the first line as indicated by both the angle finder and the straight edge. Make a second line on the ground just like you did for the first. Now turn the wheel the opposite direction and repeat, making another line at 20º to the first line.
The reason for making the lines at 20º to the first line is that the Vanagon’s caster alignment specs are based off of rotating the front wheels 20º to the right and 20º to the left (from straight ahead) and measuring the difference between the two different camber angles to help determine the caster angle. If this seems confusing, it should become clearer by reading on and looking at the pictures. And just for the record, 1 1/8 turns of a non-power steering Vanagon’s steering wheel is exactly 20º. While this would be okay to use for a rough alignment, I would not trust it for any real accuracy. Power steering-equipped Vanagons (or non power steering-equipped Vanagons with power steering uprights) would have a different steering ratio. While I don’t know this for sure, my guess is that it would be closer to one full turn for those vans
With the set up completed, we can move on to actually measuring the caster. To do this, we will use our new fancy tool from RPW. This tool is incredibly simple in it’s construction and use. It consists of a piece of aluminum angle that has a fixed peg on one end and a peg on the other end that can be moved to different holes to adjust for varying wheel diameters. The description of the tool on the sales site says that it good for up to 16” wheels, but the newest models are good for wheel sizes ranging from 12” up to 17”. Attached to the aluminum angle is a bubble level with an adjusting knob. On top of the knob are a series of eight lines.
To use the tool, you first adjust the pegs to suit your wheel diameter. My wheels are 16” so the upper peg was moved to the second to the last hole towards the top. To check the caster angle, you must first turn the wheel to the right until it is lined up exactly with your 20º mark. Use your straight edge to be sure. Accuracy is important here as any deviation will throw off your caster calculations. With the wheel in position, place the tool vertically onto the wheel so that the pegs touch both the upper and lower lips of the wheels as shown in the picture. Turn the knob in the direction necessary to center the bubble under the centering line. The bubble will move somewhat slowly, so work carefully. It is sometimes necessary to turn the knob back and forth in order to make sure that the bubble is perfectly centered.
Being careful not to change the position of the knob, set the tool down and proceed to move the wheel to the left until it lines up with your other 20º mark, again making sure that you are being accurate. Now place the tool up against the rim lips just as before, but this time you will notice that the bubble is way off from the centering line. You will need to count the number of marks that pass as you turn the knob clockwise until the bubble is centered again. On my van, it took 40 marks to center bubble. Write this number down. I suggest that you do this procedure a few times so that you can be sure that you are being accurate with your placement of the wheels as well as with your counting of the marks. The more accurate you are here, the more accurate your final alignment will be.
With the number of marks accurately counted, you need to convert the number of marks to number of full turns of the knob. The knob has eight marks on it, so we just need to divide the total number of marks that we counted by eight. In my case, 40 ÷ 8 = 5. In order to find out the angle of caster in degrees, we then have to multiply that last number by 1.5. So in my case, the complete number sequence looks like this:
40 ÷ 8 = 5, then 5 x 1.5 = 7.5º of positive caster.
If you look in the Bentley manual, you will see that the caster specs for an empty 2WD Vanagon are +7º 15' ± 15'. This translates to a perfect caster of 7º 15' with a tolerance of plus or minus 15 minutes. In other words, a caster angle of anywhere between 7º and 7º 30' is acceptable. (Thanks for catching my mistake, mwsnow)
The ' symbol after the 15 indicates minutes. Minutes are 1/60th of one degree. To convert these to degrees, divide the number of minutes by 60. 15' equates to 0.25º. This gives us a caster angle tolerance of 7º to 7.5º.
CHECKING CAMBER ANGLE -
We can use the RPW tool to check the camber, but I will also show you how to make a simple camber checking device just in case you choose not to purchase the RPW tool and only plan to tackle the camber and toe adjustments or plan to use a digital angle finder to take the place of the RPW tool.
While I do not have pictures of the entire process, using the RPW tool to check the camber is really easy. With the tool adjusted to fit your wheel diameter, you need to zero out the bubble level. You do this by lining up the center portion of the bubble level bracket with the outer portion of the bracket so that the two pieces are parallel and the arrow is pointing toward the bubble, like this:
Then it is a simple matter of positioning the pegs on the tool onto the rim lips so that the tool is held vertically. Then turn the knob in the direction necessary to allow the bubble to be centered, counting the marks that it takes to do so. If you have to turn the knob counter clockwise to level the bubble, you have negative camber and if you have to turn the knob clockwise, you have positive camber.
Each one of the marks on the knob represents 1/8 of a degree. If you had to turn the knob three marks to achieve a level bubble, you would have 3/8 of a degree camber. Since the camber specs are not given in a fractional number, we need convert the 3/8 of a degree into a decimal number. Just Google “fraction to decimal chart” and you will be greeted with many options for this. In our example, 3/8 would be converted to 0.375. In other words, we have 0.375 degrees of negative camber.
If you decide not to buy the RPW tool, but still want a way to check your camber, here is how to build a simple too to do so. (Note, this explanation was done at an earlier time and was done using millimeters and includes a similar description for obtaining the camber angle in degrees)
First, measure the distance between the rim lips on your wheels and mark this on a length of metal rod, bar, angle or tube. Anything perfectly straight and easy to handle will do. Then cut this bar approximately 3/8-1/2" longer than your mark. Find a bolt that is long enough to go all the way through the bar and protrude out the other side by at least one inch. Drill a hole straight through the tube, right at your rim distance mark, just small enough to allow you to thread the bolt through the holes. If your bolt spins too freely in the bar, add a lock nut to the outside so that you can keep it secure after you taking your measurement (to be explained further on).
Now get yourself a bubble level that will fit onto the bar that you made without making any contact with the tires, the ground or the vehicle bodywork. That is all that you need for tools to take camber measurements.
Some wheels have center spokes or center caps that protrude past the rim lips. In these cases, you will need to improvise in order to get your bar to clear these obstacles. A simple way of doing this would be to cut short section of the same material that the bar is made from and tape them in place where the bar contacts the rim lips. There are many other options so just choose one that works for you. Just make sure that whatever you add to spacer the bar out, the bar always remains parallel to the rim lips. This means that your spacers will each need to be exactly the same thickness or it will through off your measurements.
If you have a digital angle finder, you can forgo the bolt in the bar and simply read the camber angle off of the angel finder. Since not everyone has a digital angle finder (typical needle and weight style angle finders are not accurate enough for precision alignments, but they are better than nothing), I will show you how to find the camber angle without one. If you choose to use a digital angle finder (and I highly recommend it), make sure that your bar rests on the rim lips and does not get hung out on the tire. You want to have a perfectly parallel line from wheel lip to wheel lip.
The bar shown in the photos below does not exactly fit the wheel as properly as it should. It was built for another set of wheels. Even so, as long as one was careful to be sure that the bar was positioned correctly, it could be used just as it is.
Using the bar with the bubble level held tightly against it (taping the level to the bar helps), rest the bar up against the rim lips making sure that the bar points straight up and down. Adjust the bolt in the bar out until the bubble in the level shows perfectly level.
Note that if your vehicle shows positive camber at the time of measurement, you will have to invert the bar so that the bolt is on the bottom and the resulting calculations for camber angle will be for positive camber, not negative camber.
Now it's just a matter of measuring how far that bolt sticks out past the edge of the bar and doing some calculations to find the camber angle.
The Bentley manual calls for 0' (minutes) camber plus or minus 30' (minutes) front wheel camber. One minute is 1/60th of one degree. Plus or minus 30' means that the front wheel camber can be anywhere between -30' and +30' to be considered within specs. In other words, the specs call for the front wheels to be within -0.5º and +0.5º (30' ÷ 60 = 0.5º).
In order to know what the camber angle is in the example portrayed in the picture above (exaggerated to 4mm), we will have to convert the measurement into degrees. Since I am an absolute math idiot, I have to rely on some of the many online calculators for help. Using the right triangle angle calculator on this page, http://www.csgnetwork.com/righttricalc.html , and converting my 9mm measurement to inches (9 ÷ 25.4 = 0.157"), I can plug in my numbers and it will spit out my camber angle in degrees.
Enter the length that the bolt protrudes past the rod in inches (0.157) into the slot labeled “Side A” and the overall length of my rod as measured from the two contact points on the rim lip (end of rod to the center of the bolt in this case), 17.5, into the slot labeled “Side B” and push “Calculate”. The slot labeled “Angle A or B” is where you read the camber angle. In this case, the camber angle will read 0.51º.
That’s it for camber! Now you can probably see why it is easier to use a digital angle finder, but the math method is accurate and works well too.
CHECKING TOE ANGLE -
With the caster and camber out of the way and the vehicle on a properly leveled surface, it's time to lay out the string network that will allow you to take accurate measurements off of the wheel locations in order to set the toe. These measurements are what you will use to adjust your suspension into the correct position for a proper alignment.
The parts that I used for this string network are two stick of conduit (must be at least 7' long), string, four jack stands and four clamps. You will also need a quality ruler to set up the string network, but we will get to that in a minute.
Starting with the two sticks of conduit, I drilled holes in each end exactly 73" apart. The exact distance is not important as long as the strings are positioned wider than the widest part of the vehicle and at least 2" wider than the distance between the outer edges of the tires. What is important is that the holes are drilled at exactly the same distance from each other. Place two jack stands at each end of the vehicle at the corner of the vehicle. Try to position each jack stand the same distance from the vehicle as the one next to it. Position each conduit piece on top of two jack stands (one front, one rear) and secure one clamp on each jack stand in such a way that it prevents the conduit from coming off of the stand but still allows the conduit to be moved side to side.
With the conduit in place, you can then tie a string between each conduit through the drilled holes. Tying through the drilled holes ensures that the strings stay exactly the same distance apart. Pull the strings as taught as possible without tipping over the jack stands.
Please look at the pictures below for reference while reading the above descriptions.
With the strings in place, you will now need to raise or lower the position of the conduit in order to position the string at the exact centerline of the wheel hubs. Again, use whatever means you have to accomplish this. Refer to the photos above for two different approaches.
It is now time to square the strings with the chassis of the vehicle. People use various methods for this, but in the interest of keeping things as simple as possible, I like to measure off of the centers of the hubs. Even though it shows it in the pictures below, it is not perfectly accurate to measure off of the front grease caps. The caps are so easily damaged and distorted over time that they are not suited for precise measurements. The best practice is to remove the grease caps and measure from the end of the spindle.
It's now just a simple matter of making sure that the strings are the same distance between the left and right front hubs and between the left and right rear hubs. This distance will not be the same front and rear, but making the distances the same left to right will set the strings so that they are parallel with the chassis. Being parallel to the chassis is important because it helps set the thrust angle as described above.
It must be noted that it may take several tries in order to get the strings sitting exactly where they should be. I like to do a quick set-up first just making sure that the strings are kind of close. That way, when I do my final settings, the movements that I do to the string at the front of the vehicle does not have too much affect on the measurement at the rear. It usually takes me about three trips around the vehicle to get it right, but if you are not paying attention or don't do an initial setting to get the strings close, you could make many more trips back and forth.
It should also be noted that the string that I used has a thickness of just about 1mm. I like to use the inside edge of the string for my measurement points. String with a lot of fuzz is not going to be very helpful to you as smooth string gives you a crisp line of sight measurement.
Now we can move on to actually measuring the toe angle. Again, this is where the thrust angle can come into play. Toe angle adjustments can be performed without the use of the string jig. All it takes is a simple flat bar across each front wheel and a tape measure. Measure in front of the tire and in back of the tire. The difference is your toe angle. There are two problems with this method.
One is that without the strings, when checking/setting the rear wheel toe angle, there is no way to reference to the centerline of the vehicle. This means that even though the left and right rear wheels have the correct toe angle relationship, they still could be pointing off to the left or off to the right of the vehicle’s centerline. This would result in the vehicle going down the road like a crab as described in the definition of thrust angle.
The second problem is that when checking/adjusting the toe on the front without the strings for reference, there is no way to tell where the steering wheel will be positioned relative to the wheels pointing straight ahead. While the car could still go down the road straight (assuming that the rear toe is set correctly), the steering wheel could end up way off center.
Setting up the strings eliminates both of these issues.
Luckily for us, the Bentley manual spells out the front wheel total toe angle in minutes, millimeters and inches and the rear toe angle is spelled out at zero minutes so as long as it measures equal, your good. Total toe needs to be divided in half to know the single wheel toe angle.
The rest is all very simple. The Bentley manual describes how to center the steering wheel. Once this is done, it’s a simple matter of measuring from the front lip on the wheel at string height and the rear lip on the wheel and again, the difference is your single wheel toe angle. Combine the measurement differences for the left and right wheels to know the total to angle.
The pictures below show the right front toe angle at 3mm (26mm at the rear lip of the wheel and 29mm at the front lip of the wheel). Assuming that the left front wheel shows the same 3mm toe angle, this would result in a total toe angle of 6mm. An adjustment of 1mm toe out per side (or 2mm total toe out) would be needed in order to adjust the toe angle into specs. Guess I need a minor adjustment!
The pictures below show the real world measurements of the right rear wheel of my van. You can see that both front and rear lips measure 37mm (actually one of the photos looks like 37.5mm, but the ruler is angled slightly making it look that way. Taking pictures while holding rulers is hard) resulting in zero toe angle for the right rear.
That it …really! Honestly guys, I know that it looks like a lot because of all of words, but once you have the string jig and you purchase the RPW tool (or build the camber bar), the rest is really very simple. Any weekend warrior should be able to perform these operations without any real difficulty (frozen nuts and bolts not included). _________________ "Sometimes you have to build a box to think outside of." - Bruce (not Springsteen)
*Custom wheel hardware for Audi/VW, Porsche and Mercedes wheels - Urethane Suspension Bushings*
T3Technique.com or contact me at [email protected]
Last edited by Christopher Schimke on Fri Jan 22, 2010 8:28 am; edited 1 time in total |
|
Back to top |
|
 |
mwsnow Samba Member
Joined: November 13, 2007 Posts: 266 Location: Alton, NH
|
Posted: Fri Jan 22, 2010 5:35 am Post subject: |
|
|
Quote: |
If you look in the Bentley manual, you will see that the caster specs for an empty 2wd Vanagon are +7º 15’ ± 15’. This translates to a perfect caster of 7º with a tolerance of plus or minus 15 minutes |
You have obviously spent a lot of time refining these procedures and the how-to for our benefit. For the sake of correctness, the "perfect" caster is +7º 15’. The range of allowable measurements is +7º 0’ to +7º 30’. |
|
Back to top |
|
 |
Christopher Schimke Samba Member

Joined: August 03, 2005 Posts: 5530 Location: PNW
|
Posted: Fri Jan 22, 2010 7:56 am Post subject: |
|
|
mwsnow wrote: |
Quote: |
If you look in the Bentley manual, you will see that the caster specs for an empty 2wd Vanagon are +7º 15’ ± 15’. This translates to a perfect caster of 7º with a tolerance of plus or minus 15 minutes |
You have obviously spent a lot of time refining these procedures and the how-to for our benefit. For the sake of correctness, the "perfect" caster is +7º 15’. The range of allowable measurements is +7º 0’ to +7º 30’. |
Thank you for catching my mistake. I guess it doesn't pay to power on through when I'm tired. Glad you caught it. If anyone else finds a mistake, PLEASE let me know asap so I can edit the original post instead of having to add more posts explaining the mistake. Thanks again! _________________ "Sometimes you have to build a box to think outside of." - Bruce (not Springsteen)
*Custom wheel hardware for Audi/VW, Porsche and Mercedes wheels - Urethane Suspension Bushings*
T3Technique.com or contact me at [email protected] |
|
Back to top |
|
 |
Raynor Shine Samba Member

Joined: November 07, 2005 Posts: 552
|
Posted: Fri Jan 22, 2010 8:15 am Post subject: |
|
|
WOW! I nominate for a sticky if it isnt already. This is fantastic detail, any chance you can come over to my house next week to complete this on my van?
Good work loogy. |
|
Back to top |
|
 |
aquaboxa Samba Member
Joined: August 30, 2009 Posts: 96 Location: Upstate NY
|
Posted: Fri Jan 22, 2010 8:33 am Post subject: |
|
|
so how much DO you charge for the perfect alignment?  _________________ '89 Vanagon Bluestar
a.k.a. "The Bermuda Rectangle" |
|
Back to top |
|
 |
deprivation Samba Member
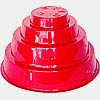
Joined: September 14, 2006 Posts: 1220 Location: Austin, Texas
|
Posted: Fri Jan 22, 2010 9:55 am Post subject: |
|
|
Holy freaking wow. _________________ 1986 Westy 2WD auto a.k.a. "The Old Girl"
www.kittenfart.com |
|
Back to top |
|
 |
MarkWard Samba Member
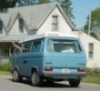
Joined: February 09, 2005 Posts: 18823 Location: Retired South Florida
|
Posted: Fri Jan 22, 2010 11:15 am Post subject: |
|
|
Chris, this is how I check and adjust the alignment on the race car. Great right up and photos. Thank you for sharing. mark |
|
Back to top |
|
 |
izzydog Samba Member
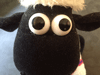
Joined: April 28, 2005 Posts: 666
|
Posted: Tue Jan 26, 2010 12:25 pm Post subject: |
|
|
Fantastic write up, but I have a few dumb camber-related questions:
If the camber needs to be set to "0", then why can't you just find vertical level with a level against the wheel by adjusting out the difference from the top and bottom of the wheel? In other words, adjust the camber until you are at vertical level?
And... the related adjusting question: When you adjust for correct camber, is the van on the ground or in the air?
Thanks,
Jeff |
|
Back to top |
|
 |
Christopher Schimke Samba Member

Joined: August 03, 2005 Posts: 5530 Location: PNW
|
Posted: Tue Jan 26, 2010 12:42 pm Post subject: |
|
|
izzydog wrote: |
Fantastic write up, but I have a few dumb camber-related questions:
If the camber needs to be set to "0", then why can't you just find vertical level with a level against the wheel by adjusting out the difference from the top and bottom of the wheel? In other words, adjust the camber until you are at vertical level?
And... the related adjusting question: When you adjust for correct camber, is the van on the ground or in the air?
Thanks,
Jeff |
Not a dumb question at all. You can most certainly use a level against the wheel lips to measure the camber at zero. However, there are circumstances where zero camber can be difficult to achieve, like when lift springs are installed. You want a way to make sure that the camber is even on both sides, even if it is out of spec slightly. Also, there is a tolerance from zero that would be difficult to judge using just a level. Again, as long as your level can be positioned so that it rest squarely on both the upper and lower wheel lips without contacting the tire or hub, you would be fine so long as you can actually achieve zero camber on both wheels.
All alignment measurements should be checked with the vehicle at ride height and loaded in a typical fashion including driver weight. All measurements are taken with the vehicle "on the ground" and if adjustments are necessary, the vehicle must be lifted into the air, adjustments made and then let back down to re check the measurements. This is where the lube between the two last tiles comes into play. When you let the vehicle back down, you will want to bounce on vehicle a bit to help settle the suspension. The lube between the two tiles helps the suspension settle easier by allowing the tires to move freely both left and right as well as front to back. If you don't settle the suspension, you will get false readings for whatever measurement you are taking. _________________ "Sometimes you have to build a box to think outside of." - Bruce (not Springsteen)
*Custom wheel hardware for Audi/VW, Porsche and Mercedes wheels - Urethane Suspension Bushings*
T3Technique.com or contact me at [email protected] |
|
Back to top |
|
 |
MarkWard Samba Member
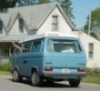
Joined: February 09, 2005 Posts: 18823 Location: Retired South Florida
|
Posted: Tue Jan 26, 2010 12:47 pm Post subject: |
|
|
I bought a digital torpedo level at HD when I needed some exact angle measurements. It was less than $40. It is very sensitive, but could give you a digital value to compare side to side. |
|
Back to top |
|
 |
Christopher Schimke Samba Member

Joined: August 03, 2005 Posts: 5530 Location: PNW
|
Posted: Tue Jan 26, 2010 1:11 pm Post subject: |
|
|
Absolutely! A digital level/angle finder would work great too. I wrote the above scenerio trying to keep the effort and cost as low as possible. They don't always play nice with each other though. Case in point, if you didn't have much money, but needed to find your camber angles, the bolt, bar and level as described above works great, but it is more effort. On the other hand, a digital level/angle finder or the camber/caster gauge is much easier to use, but they cost more. Your choice! _________________ "Sometimes you have to build a box to think outside of." - Bruce (not Springsteen)
*Custom wheel hardware for Audi/VW, Porsche and Mercedes wheels - Urethane Suspension Bushings*
T3Technique.com or contact me at [email protected] |
|
Back to top |
|
 |
izzydog Samba Member
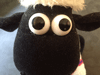
Joined: April 28, 2005 Posts: 666
|
Posted: Tue Jan 26, 2010 1:21 pm Post subject: |
|
|
Thanks, Loogy.
I have a year-old set of VanCafe springs on my Syncro Westy so I don't know if there's camber adjustment left or not. I noticed just yesterday that the outside of my front passenger tire is wearing faster than the rest of the tire so I need to check it.
My garage is anything but level. Now where did I put that extra box of floor tiles...? |
|
Back to top |
|
 |
JustBuggy Samba Member

Joined: August 01, 2010 Posts: 851 Location: SF Bay Area, Ca.
|
Posted: Fri Jun 10, 2011 6:18 am Post subject: |
|
|
This may be an old topic but I think it's worthy of a "Bump".
Thanks for taking the time to put this all together. Awesome writeup! |
|
Back to top |
|
 |
Bassyaks Samba Member
Joined: October 06, 2010 Posts: 1140 Location: S.E. Connetitcut
|
Posted: Fri Jun 10, 2011 7:49 am Post subject: |
|
|
Great write up, but spend the $40 and have it done on a Hunter Machine
You have too much free time
Steve |
|
Back to top |
|
 |
ALIKA T3 Samba Member

Joined: July 30, 2009 Posts: 7216 Location: Honolulu,Hawaii and France
|
|
Back to top |
|
 |
gimpy60 Samba Member
Joined: May 09, 2007 Posts: 668 Location: Just down the road
|
Posted: Tue Aug 30, 2011 1:54 pm Post subject: |
|
|
Ok, I'm trying this diy on my ghia. New ball joints, tie rods etc. I have a digital level & self leveling laser. Checked the camber for s&g, came up with 89.15* both sides which seems just beyond the limit. So ran the laser, & rolled the car on some floor tiles to level it. Now I have 88.90* on right & 89.30* on left. I shimmed 3/8" on right & 1/2" on the left. Should I try to get the right closer to the left which seems to be in tolerance (based on the bently specs) or go ahead with the strings to set the toe? I'm lowered about 3" in front w/adjusters, & put one set of caster shims. New tires, car drives decent, but seems it needs some tweeking. Looking for ideas from experienced alignment gurus. thanx _________________ How the hell ya spost ta fix it, ya don't even know how it works boy |
|
Back to top |
|
 |
ihurley Samba Member
Joined: May 10, 2010 Posts: 12
|
Posted: Tue Dec 20, 2011 3:57 am Post subject: |
|
|
There is one very BIG error in the math in the CAMBER ANGLE section. Using the RPW tool, the 3/8 of a degree camber is already in degrees. There is no need to use the right triangle calculator at the link you provided. Entering the 3/8 degrees (or decimal equivalent) in the "SIDE A LENGTH" slot is a big no no. it is not a length. It's a degree. You have already found the degree. You just need to convert it to minutes.
It is actually WAY more simple.
It is already a degree (or 3/8th of one to be precise) so simply multiply by 6O and you get minutes.
3/8*60 (3 divided by 8 multiplied by 60)
which equals 22.5'
So you were actually within the specs of 0 plus or minus 30'
I hate to point out errors, but this would really mess some people's alignment up pretty bad. If someone was only 4 marks or 4/8 of a degree off (which is 30' and right on the limit) using the method described in your post, they would get a value of 1.63 and think they were over 1 whole degree off. and it gets worse the bigger the number. 8 marks or 1 degree on the RPW tool (which is 60') using the triangel calculator as described would return a value of over 3.3 degrees... when in fact they were only over by half a degree or 30'. The bigger the first number the more extreme the error.
Another way to make it even easier is to to see that 30' is simply 1/2 a degree or 0.5 degrees.
If the RPW tool measures in increments of 1/8 of a degree, then 4 marks is 4/8 which is 1/2 or 0.5 degrees which is 30' which is the limit for camber.
Therefore to make sure you are within the limit for camber, all you need to do is make sure you are less then 4 marks off. If you turn it more than 4 marks, you need to make an adjustment to get it less than that.
You can use the list below for quick reference to find minutes for any amount of marks. Each time you make a full turn, just add a full degree and start counting the minutes again, or you can just think of the dial like a clock and read it accordingly, adding a degree for every full turn or hour. Too bad the dial doesn't have an hour (degree) hand to keep track for us.
1 mark is 7.5'
2 marks is 15'
3 marks is 22.5'
4 marks is 30' or half a degree (or hour if that helps)
5 marks is 37.5'
6 marks is 45'
7 marks is 52.5
8 marks is 60' or one full degree (think hour).
Side note: if anyone ever wants to find the decimal equivalent of a fraction, just divide the top by the bottom in any regular calculator. No need for any special faction calculators.
Sorry this was so long. Just trying to be thorough and throw in a little extras to help people out. Just a couple different ways to look at it because everyone one is different in how they get things... I just happen to be uber mathematical... love the stuff...
P.S. Totally off topic, but thank you guys at T3Technique.com. you have been so helpful in geting my new wheels set up to work... You really were helpful with all my questions and emails. I only have one wheel on so far, but that's because I am still finishing putting in new lift springs, new shocks and I'm redoing all joints and bushings while I'm at it, plus new oversized brakes (if I knew it was going to be this much work...) One wheel down, 3 to go. Hopefully tomorrow I'll be riding on 4 new wheels. So excited... though I'll be in need of an alignment with all the new mods and suspension parts... hope I can try your technique out soon. Thanks again, for that and for this alignment tutorial. |
|
Back to top |
|
 |
Christopher Schimke Samba Member

Joined: August 03, 2005 Posts: 5530 Location: PNW
|
Posted: Tue Dec 20, 2011 8:24 am Post subject: |
|
|
ihurley, thank you SO much for taking the time to read and correct that mistake. I re-read what I wrote and even I can't figure out why it was written that way. Actually, I think that it was simply an editing error...a big one! If you notice at the top of the page, it was stated that this was supposed to be a cleaned up version of the original post. I am certain that I just neglected to edit properly and what resulted are the mistakes that you pointed out. That's the only reasoning that I figure that would explain such a gross error. I am a self admitted math idiot, but even I know that what was written is wrong.
Since I can't edit this post any longer, I will have to ask one of the moderators to do it for me. It may take a while, but I will fix that. _________________ "Sometimes you have to build a box to think outside of." - Bruce (not Springsteen)
*Custom wheel hardware for Audi/VW, Porsche and Mercedes wheels - Urethane Suspension Bushings*
T3Technique.com or contact me at [email protected] |
|
Back to top |
|
 |
FNGRUVN Samba Member

Joined: October 27, 2007 Posts: 2237 Location: Fort Collins, CO
|
Posted: Tue Dec 20, 2011 7:41 pm Post subject: |
|
|
Bassyaks wrote: |
Great write up, but spend the $40 and have it done on a Hunter Machine
You have too much free time
Steve |
Sure, you can take it to a tire shop where some dude that's probably hung-over, making $10/hr and hates your stupid foreign car will beat on it.
Do it yourself and you at least know you tried to do it right. That's more than I can say about a lot of "professional" alignments I've seen. _________________ "Democracy is two wolves and a lamb voting on what to have for lunch. Liberty is a well-armed lamb contesting the vote." - Benjamin Franklin |
|
Back to top |
|
 |
rubbachicken Samba Member

Joined: October 05, 2004 Posts: 3058 Location: socal
|
Posted: Wed Oct 03, 2012 12:36 pm Post subject: |
|
|
Bassyaks wrote: |
Great write up, but spend the $40 and have it done on a Hunter Machine
You have too much free time
Steve |
FNGRUVN wrote: |
Sure, you can take it to a tire shop where some dude that's probably hung-over, making $10/hr and hates your stupid foreign car will beat on it.
Do it yourself and you at least know you tried to do it right. That's more than I can say about a lot of "professional" alignments I've seen. |
X2 i've paid out for someone to do an alignment in the past, it came back little or no better, i argued they said i must have hit something to knock it out of alignment
money wasted
now i have seen how, i will be happy to do the job myself
and know it's done right
thank you loogy _________________ lucy our westy
lucy's BIG adventure
meet 'burni' |
|
Back to top |
|
 |
|