Author |
Message |
baxsie Samba Member
Joined: August 09, 2005 Posts: 606 Location: Eastern Washington State
|
Posted: Mon Sep 17, 2012 11:22 pm Post subject: Farm boy hinge pin puller . . . cutting and welding only |
|
|
I was struggling to get the hinge pins out of the 1975 LaGrande Super Beetle. I went looking for tools but there appear to be none available for anything near a reasonable cost. As I thought about it, all you really need is to push a punch up from the bottom, while holding it perfectly aligned.
How hard could that be? Well, it would be this hard:
This VW door hinge pin puller can be made in short order using:- cutoff saw
- welder
- drill
- flat file
- common hardware, locally available
Please note that nothing is measured with calipers or a tape. It is all done by sight. Hey, I said I was a farm boy. By the way, all the photos were taken with an iPhone 4. I bead blasted many times during the build, mainly because I have a bead blaster. It makes things look pretty, but is not necessary.
I rummaged around in the scrap pile to get ideas:
I did not want to ruin a good punch, plus it was not quite long enough. For $6.99 HFT comes to the rescue. As a bonus, I later found that the pin can be pulled out of this punch, so it could be removed during the welding to make sure it does not lose its temper:
The Hillman display at Lowes supplied some beefy flat stock:
I got a 1/4 inch drive 7/16 inch deep socket from the clearance rack at Ace. This will provide the place for the pin to push into:
The socket needs to be spaced out from the body of the tool. I used some 1/2 by 1/2 keystock I had. Here I am measuring the length of the keystock:
Cutting the keystock spacer:
We need to clear the 8mm hinge pin where it will push up into the socket. I used a 3/8 drill. The socket is tough, so use a good bit, go careful and use lube. Come to think of it, that advice works for many situations, not all involving drills:
The 5/16 pin punch is 7.9375mm nominally, but that would be a really tight fit in a rusted, painted 8mm hole. I used a DA with 180 grit and the drill to make it slightly smaller. You could use a flat file or sandpaper:
Marking the length of pin punch that is needed:
Line it up and clamp it in the cutoff saw:
And let the sparks fly:
Looking at the travel, scratching my head:
Decided that the handle of the punch should be this long:
I cut that at a 30 degree angle. Mainly because I could:
A mock up, looking at the travel. The bolt is a 1/2" fine thread "spring bolt" that I happened to see at NAPA while I was at the parts counter. Basically a long grade 5 bolt with very long threads. I got some 1/2" fine thread Grade 8 nuts at ACE:
Some more cutting with the cutoff saw (some "safe cutoff saw use" rules may have been broken). Also test placing of the beefy blocks that will take the brunt of the force:
Test fit of the beefy side plates, which the nut will push against:
My very first TIG weld (this could have been done with a MIG, or maybe even a stick, if you were really good, but I was itching to try the TIG out):
Preparing to TIG on the punch. If I had to do it again, I think I would just drill a hole in the steel to accept the pin of the punch. At this point tin the project, I still did not know that the pin of the punch could be disassembled from the handle:
Back to the MIG. Those welds in the center are plug welds filling 3/8" holes pre-drilled through the side plate that increases the rigidity:
Cleaned up with the bead blaster makes it almost look like a good weld:
Prepping the outer part that will hold the socket and slide over the inner part:
The socket and its 1/2" keystock welded to the outer sliding portion. There is a chunk of the flat stock inside to enforce the fit:
Getting ready to weld on the beefy chunks of flat stock that the nut will push against. The stock inside and the C-Clamps are an attempt to minimize the warpage from the heat of the welding. It was a challenge to get that chunk of stock out. Once it was out a little flat filing and sanding made the pieces fit well with no detectable slop. (Not shown: I covered my C-clamps with tape so I did not ruin the threads with spatter.):
Some sanding and filing later . . . the two pieces fit together. By cocking them, I could get access to weld the bolt in place. That is actually a bit of dumb luck . . . there were a couple moments of panic when I thought there would be no way to weld the bolt to the sliding part! Once that weld is in place, the two pieces cannot be separated. Be sure to mask off the sliding parts so welding spatter messes up your nice sliding parts (he says with perfectly clear 20-20 hindsight):
Four views of the finished project. Lots of thick grease on the slides and threads:
Action shots:
Here you can see that the tool's pin punch is pushed in almost all the way. Looking down into the socket you can see the hinge pin getting pushed up:
We used this to remove 3 pins. We did spray the pins with PB Blaster a few hours before. The first one we did gingerly with the hand wrenches, some careful taps with the hammer, etc. The second pin we stuck a deep socket on the impact wrench and let it go . . . worked a charm
The clearance is not great, but it does clear. If the paint is precious, please put something between the tool and the paint to protect the paint (2 places). Maybe one of those really thin plastic cutting mats from the kitchen?
Things I would do differently:- use only the pin of the punch, seated in a blind hole drilled in the sliding metal. This would also keep the welding from possibly ruining the hardening of the pin, and make the clearance from the body better.
- use 1/2 inch stock for the slide, so the 1/2" bolt does not make the assembly permanent. Could probably go without the triangle bits then.
- laser/waterjet cut the parts (f you were gonna make more than one)
- come up with a stationary bolt, moving nut design so an impact wrench could be used
- maybe use the bolt from a gear puller . . . I do not know how long my hardware store bolt and nut arrangement will wear. Well, it certainly seems to have lasted through three operations so far
 In all, the parts cost was less than $100, labor maybe 4-8 hours depending on skill and "design" time.
The best thing? My hinge pins are OUT! |
|
Back to top |
|
 |
far rider  Samba Member
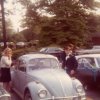
Joined: August 30, 2005 Posts: 932 Location: Rutland, VT
|
Posted: Tue Sep 18, 2012 9:16 am Post subject: |
|
|
Very clever. thanks for posting - especially the pics. _________________ 67 zenith blue sunroof
Contentment; when what you have is what you want. |
|
Back to top |
|
 |
far rider  Samba Member
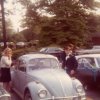
Joined: August 30, 2005 Posts: 932 Location: Rutland, VT
|
Posted: Tue Sep 18, 2012 9:17 am Post subject: |
|
|
Very clever. thanks for posting - especially the pics. _________________ 67 zenith blue sunroof
Contentment; when what you have is what you want. |
|
Back to top |
|
 |
vaughn bros. Samba Member
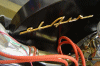
Joined: October 13, 2003 Posts: 2398 Location: Hickory, NC
|
Posted: Tue Sep 18, 2012 9:51 am Post subject: |
|
|
PERFECT!  |
|
Back to top |
|
 |
pfcmooney Samba Member
Joined: December 07, 2011 Posts: 219 Location: New Brockton, AL
|
Posted: Fri Sep 21, 2012 5:41 am Post subject: |
|
|
Damnit, wish the pictures were still showing.  |
|
Back to top |
|
 |
baxsie Samba Member
Joined: August 09, 2005 Posts: 606 Location: Eastern Washington State
|
Posted: Fri Sep 21, 2012 7:29 am Post subject: |
|
|
The pics should still be working. Try reloading and wait. I think that FTP service may be a little flakey  |
|
Back to top |
|
 |
talljordan Samba Member

Joined: January 10, 2012 Posts: 1066 Location: San Francisco, CA
|
Posted: Wed Jul 23, 2014 4:37 pm Post subject: |
|
|
Perhaps you should consider mirroring the pictures on thesamba or imgur and providing a link. Your FTP site may not be around in 15 years, but these forums probably will be. _________________ 1972 Super Beetle, Parked until adequate restoration funding is acquired in restoration!
Wanted: Male computer diagnostic plug end |
|
Back to top |
|
 |
baxsie Samba Member
Joined: August 09, 2005 Posts: 606 Location: Eastern Washington State
|
Posted: Wed Jul 23, 2014 5:17 pm Post subject: |
|
|
Bagged that FTP server. Have a real server in a real colo, that I can touch. #cloudfail |
|
Back to top |
|
 |
Dauz Samba Member

Joined: January 05, 2010 Posts: 1861
|
Posted: Thu Jul 24, 2014 4:39 pm Post subject: |
|
|
Do '75s not have bolt plates behind the hinge pillars in which to remove mounting bolts for the doors? Just curious as to why you'd want to remove all of the hinge pins. I'd have thought you'd only remove the top hinge pins to install side view mirror mounts. |
|
Back to top |
|
 |
baxsie Samba Member
Joined: August 09, 2005 Posts: 606 Location: Eastern Washington State
|
|
Back to top |
|
 |
Dauz Samba Member

Joined: January 05, 2010 Posts: 1861
|
Posted: Thu Jul 24, 2014 9:51 pm Post subject: |
|
|
baxsie wrote: |
They have the bolt plates, but the screws in the bolt plates were rusted frozen and the heads stripped.
Plus the hinges were very stiff.
We ended up removing the hinges first, then removed the screws on the bolt plate by using the weld-inside-a-nut technique, which worked great,
Had I known that technique, we might have avoided removing the hinge pins. |
I had the same problem. A $14 pack of easy-outs from Home Depot provided the resolution. :shrug: |
|
Back to top |
|
 |
|