Author |
Message |
nlorntson Crazy VW Lady
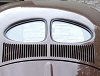
Joined: March 13, 2004 Posts: 3783 Location: Twin Cities, MN
|
Posted: Sun Feb 17, 2013 5:00 pm Post subject: DIY door bottom repair with replacement panels |
|
|
I thought it might be nice to put together a post on how to replace the rusty, crusty bottom of a split door using the repair panels from Mika Virtanen. Mika sells these pieces separately which is a good thing because they need to be installed separately.
http://www.thesamba.com/vw/classifieds/detail.php?id=1258109
Here is what we are starting with. Probably the typical look for the bottom of a split door.
Sight down bottom edge
Crusty lower hinge area
Rear bottom corner
Front bottom corner
Here is the inner repair piece. You can see about how far this goes up the side of the door.
The inside of inner repair piece is just as nice as the outside.
The first order of business is to mark where to cut. By lining up the bottom edge of the new inner panel with the original panel we can scribe a line across the front and rear edges of the door. We'll also take a measurement between the trim panel holes on the original door so we can see if the new replacement panel is in the right spot.
Next we'll use a sawzall to cut through sides
Rear edge cut
Once both sides are cut at our mark we need to separate the inner and outer pieces of the original door along the bottom seal channel We used a sharp, flat blade to cut between the spot welds holding inner and outer door pieces.
Separation between old inner and outer
separating bottom spot welds
Once all the spot welds are separated, the old bottom can be removed.
Old bottom
You'll want to clean up the bottom of original door so the new inner panel will fit flush against the old outer skin
Initial fit
With just a little minor grinding to replacement piece, we were able to get the replacement piece to line up perfectly with the old outer skin and inner panel.
It helps to clamp one side in place while fitting the other.
Measuring between the holes should be 5 15/16" from the bottom of one to the bottom of the next one here.
We also need to be sure the panel is in line with the inner rib. We use a long straight edge to check for straight.
Now that the panel is in the right spot, we'll clamp it in several places,
Next we'll tacked the panel in place on both sides.
After one final check of position, we'll finish the welds on each side
Then we'll so some light grinding and let the body work take care of the rest.
Now we can flip the door over and finish the outer panel. Here is a comparison of the two pieces. We found that the replacement piece did need to be trimmed along the center bottom (the edge touching the old skin) to get a more concave shape to match the contour of the door opening. You can see that it is perfectly straight to begin with.
We'll line up the new piece to scribe a line
Each side needs to be cut to allow the shear to make the cut across the face of the door.
Next we use an air powered shear to follow scribed line on the outer skin
With the outer skin cut off, we can flip the door over and slip in the replacement panel. It has a bend across the top to allow a nice overlap.
We will use some 3M panel bonding adhesive for this piece. It is used widely in the industry today as it is stronger than the metal it is bonding and will not cause any warp or distortion as would be the case with welding.
All surfaces must be scuffed up prior to gluing.
We created a pair of oak boards contoured to the final concave shape we expect for the door. These will be used to hold the seam together.
We'll use a series of other clamps across the bottom to hold the bottom joint together
We'll apply the glue to both surfaces of each piece.
After fitting the piece in place, we lined up our contoured boards and used clamps to hold it all in place.
The panel bonding adhesive sets up within 4 hours and is cured in 24.
Here is the door test fit in the opening.
We'll reinstall the lower hinge and finish the body work on the rest of the door. |
|
Back to top |
|
 |
johnshenry  Samba Member

Joined: September 21, 2001 Posts: 9364 Location: Northwood, NH USA
|
Posted: Sun Feb 17, 2013 5:23 pm Post subject: |
|
|
Nice writeup! Thanks for taking the time to take all the pics and describe the details (I know all about that!).
So the outer lower skin is flanged, right? How will you address the outside of the door seam where the new panel is? I know about the bonding adhesive, it really is strong. But I'd be concerned about using filler over that seam on the outside skin? And I guess you can't run a weld bead there because you'd burn the adhesive?? _________________ John Henry
'57 Deluxe
'56 Single Cab |
|
Back to top |
|
 |
nlorntson Crazy VW Lady
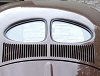
Joined: March 13, 2004 Posts: 3783 Location: Twin Cities, MN
|
Posted: Sun Feb 17, 2013 9:17 pm Post subject: |
|
|
John, with the flange allows the original skin and the new piece to line up flat with a seam of about 1/16". The adhesive cures hard like filler and can be sanded so we'll scuff up the adhesive and metal on either side so the filler will stick.
No worries at all about any bonding issues. |
|
Back to top |
|
 |
BryanNunes Samba Member
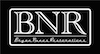
Joined: November 19, 2010 Posts: 88 Location: Hollister
|
Posted: Sun Feb 17, 2013 9:41 pm Post subject: |
|
|
I hope you weld the seam across the skin because that stuff isn't suppose to be used like that, its fine on the edges and glueing a bed side on, but not across or in the middle of the panel. If you put body filler to close the seam up (especially if you use that metal to metal crap) it while show a line or could crake up later when your car is painted setting in the sun, the heat moves metal expanding and contracting and the body filler in the seam moves differently. i've have fixed many doors and tailgates that people have "shaved" with that glue.  _________________ https://www.facebook.com/BNRestoration
http://www.thesamba.com/vw/classifieds/detail.php?id=1723384 |
|
Back to top |
|
 |
johnshenry  Samba Member

Joined: September 21, 2001 Posts: 9364 Location: Northwood, NH USA
|
Posted: Sun Feb 17, 2013 9:45 pm Post subject: |
|
|
BryanNunes wrote: |
I hope you weld the seam across the skin because that stuff isn't suppose to be used like that, its fine on the edges and glueing a bed side on, but not across or in the middle of the panel. If you put body filler to close the seam up (especially if you use that metal to metal crap) it while show a line or could crake up later when your car is painted setting in the sun, the heat moves metal expanding and contracting and the body filler in the seam moves differently. i've have fixed many doors and tailgates that people have "shaved" with that glue.  |
That would be my concern. "if it isn't welded, it will eventually show crack" is my rule.... _________________ John Henry
'57 Deluxe
'56 Single Cab |
|
Back to top |
|
 |
chthemonkey Samba Member
Joined: July 30, 2008 Posts: 105 Location: united kingdom
|
Posted: Mon Feb 18, 2013 12:57 am Post subject: |
|
|
Quote: |
That would be my concern. "if it isn't welded, it will eventually show crack" is my rule.... |
what about lead or would the whole lenght of the door be to much |
|
Back to top |
|
 |
joshbuchan Samba Member
Joined: April 12, 2007 Posts: 712 Location: victoria bc canada
|
Posted: Mon Feb 18, 2013 7:11 pm Post subject: |
|
|
I know guys use this stuff all the time but I would also be concerned about the expansion/contraction.
I attempted butt welding a door skin on a ribbed door a while ago.....warped the piss out of it and finally gave up to find a better set.......Aint no easy task!!! Just finished metalworking using a shrinking disk getting creases out of "better" ones. Chasing Oil can dents all over the bloody things
I HATE DOORSKINS!!! |
|
Back to top |
|
 |
ZwitterND Samba Member
Joined: September 08, 2005 Posts: 1451 Location: Fargo, ND
|
Posted: Mon Feb 18, 2013 7:18 pm Post subject: |
|
|
My paint supplier told me they have seen a lot of problems with that panel glue and it showing through the paint. So much so that some paint companies will void the warranty. In an unrelated subject I also heard some paint suppliers void warranty if the vehicle has been soda blasted due to bonding issues. It pays to spend some time "bs'ing" with the paint boys. _________________ Bill |
|
Back to top |
|
 |
splitjunkie Samba Member

Joined: April 04, 2006 Posts: 4095
|
Posted: Tue Feb 19, 2013 5:46 am Post subject: |
|
|
One concern about an overlapping seam is moisture getting into the seam. Since the bottom panel is seamed the seam is open at the top inside the door. Some water will get inside the door, the water will go into the seam. If you utilize the flanges so you have the seam they should be sealed over on the inside with something like fiberglass to seal the seam up water tight.
I have some of those panels and they are really nice. My plan is to cut off the flanges and butt weld the joint. _________________ Chris
You know, a lot of these scratches will buff right out... Jerry Seinfeld |
|
Back to top |
|
 |
johnshenry  Samba Member

Joined: September 21, 2001 Posts: 9364 Location: Northwood, NH USA
|
Posted: Tue Feb 19, 2013 7:30 am Post subject: |
|
|
splitjunkie wrote: |
One concern about an overlapping seam is moisture getting into the seam. Since the bottom panel is seamed the seam is open at the top inside the door. Some water will get inside the door, the water will go into the seam. If you utilize the flanges so you have the seam they should be sealed over on the inside with something like fiberglass to seal the seam up water tight.
I have some of those panels and they are really nice. My plan is to cut off the flanges and butt weld the joint. |
Is the thickness of Mika's panels the same as the doorskin? I thought he once said it was 1mm, and that would be thicker than the original, making butt welding tricky. Nancy, can you mic' the panels for thickness?
I agree that if flanging is used, the seams must be well sealed on the backside. A good autobody seam sealer is needed for this and available... _________________ John Henry
'57 Deluxe
'56 Single Cab |
|
Back to top |
|
 |
virtanen Samba Member

Joined: January 08, 2006 Posts: 1463 Location: Finland
|
Posted: Tue Feb 19, 2013 10:16 am Post subject: |
|
|
Both inner panel and outer skin are made of 1 mm thickness (original ~0.75 mm), the idea is you have material to grind down after welding and get stiffer construction.
I have spot welded outer skin with flange successfully. Start middle. _________________ Mika
Split beetle restoration panels
Oval beetle restoration panels
New projects |
|
Back to top |
|
 |
johnshenry  Samba Member

Joined: September 21, 2001 Posts: 9364 Location: Northwood, NH USA
|
Posted: Tue Feb 19, 2013 10:54 am Post subject: |
|
|
My concern is with butt welding panels that are of two different thicknesses. You can't use typical panel alignment clamps, and you will likely not get a perfectly "planar" surface after you grind down.
I suppose you could use magnets to align the panels on the "good" side, but welding around/near magnets is tricky... unless you are doing gas welding.
Also, one panel will be a better weld than the other. Set the heat for 1mm and you will burn through the .75 panel. Set heat for .75mm and you will not get good penetration on the 1mm panel. _________________ John Henry
'57 Deluxe
'56 Single Cab |
|
Back to top |
|
 |
splitjunkie Samba Member

Joined: April 04, 2006 Posts: 4095
|
Posted: Tue Feb 19, 2013 6:33 pm Post subject: |
|
|
I really don't think there is enough of a difference to cause a problem with penetration. We are only talking about .25 of a mm. If we were talking about very thick metal, then 25% difference would make a difference but when you are talking about 1 mm thick it's not like you are getting to that level of precision with penetration in the first place. _________________ Chris
You know, a lot of these scratches will buff right out... Jerry Seinfeld |
|
Back to top |
|
 |
eurodub Samba Member

Joined: August 05, 2007 Posts: 1321
|
Posted: Tue Feb 19, 2013 11:43 pm Post subject: |
|
|
i have successfully welded a beetle's roof , a secret was to have a cold wet rag near , using it to shrink metal as i was welding small sections at a time. _________________ 1960 1200 model 117 deluxe ragtop
1974 T2 Westfalia Campmobile
1976 MK1 Golf |
|
Back to top |
|
 |
ZwitterND Samba Member
Joined: September 08, 2005 Posts: 1451 Location: Fargo, ND
|
Posted: Wed Feb 20, 2013 5:39 am Post subject: |
|
|
I have welded a lot of panels. You just tack, tack, tack ..tack it ...Happy Gilmore style...then you just tap tap tap it out. Patience. _________________ Bill |
|
Back to top |
|
 |
usariemen Samba Member

Joined: August 28, 2004 Posts: 1745 Location: Germany
|
Posted: Sun Oct 06, 2013 2:50 pm Post subject: |
|
|
Today I started with the same repair.
Using the nice panels of Mika Virtanen.
As you see, this door needed help.
After measuring ten dozend times you have to cut.
Well, now it was welding time.
I´m not the most experienced welder. But learning by doing never was wrong to me. Though a Heb door is something special for training.
Then flipping the door and do the lower skin.
Refixing the hinge can be done now.
I choosed screws instead of rivets.
I stopped now after fixing the panel just with two little tacks.
I wondered if a number of spots and body filler will do the job or if I should weld it all the way. I am a bit afraid of warping when I weld it completely.
What would you guys think? _________________ Master of my domain! |
|
Back to top |
|
 |
BDSBSS23 Samba Member
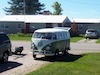
Joined: January 03, 2008 Posts: 1817 Location: Colorado
|
|
Back to top |
|
 |
johnshenry  Samba Member

Joined: September 21, 2001 Posts: 9364 Location: Northwood, NH USA
|
Posted: Sun Oct 06, 2013 5:05 pm Post subject: |
|
|
You should absolutely weld it all the way across. Tack it about every 40mm or so, go all the way across. Then go back and tack in between those, all the way across, then go back and in between those, keep doing that until you have filled it all the way in.
Inspect the back side and make sure you have good weld penetration. This is very important because you are going to be grinding all of the face of the weld off.
Leaving pin holes and then using filler on the outside would be very bad. The filler will eventually absorb moisture and swell. It is very important that you close up the weld completely. Turn off the lights and pass bright light along and view it from the other side to make sure it is completely welded up.
Looks good so far!! _________________ John Henry
'57 Deluxe
'56 Single Cab |
|
Back to top |
|
 |
VEE DUB BOYS Samba Member
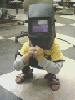
Joined: August 30, 2011 Posts: 146 Location: Greenville, SC
|
Posted: Sun Oct 06, 2013 6:17 pm Post subject: |
|
|
usariemen wrote: |
Today I started with the same repair.
Using the nice panels of Mika Virtanen.
What would you guys think? |
 |
|
Back to top |
|
 |
beetleseb Samba Member
Joined: November 09, 2006 Posts: 430 Location: Cheltenham UK
|
Posted: Mon Oct 07, 2013 6:13 am Post subject: |
|
|
Gas or Tig would make a better weld on the butt joint. It is also not as brittle as mig due to the heat/cool cycle and easier to work/less prone to crack when ground down. You can do it with mig but take your time. Plenty of tea breaks and keep it cool.
I would flange spot/plug weld and lead load. The lead will really creap in the joint and keep out the moisture.
Got to agree Mika's panels are great,
Seb _________________ Wanted - OG 50 split bug door panels, brown mats and old running boards |
|
Back to top |
|
 |
|