Author |
Message |
runslikeapenguin Samba Member
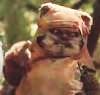
Joined: August 07, 2005 Posts: 4674 Location: Federal way WA
|
Posted: Sat Mar 29, 2008 11:33 pm Post subject: Adjuster installation walk through |
|
|
a few people have been wondering about the installation process of the sway away type adjusters that are typically used in off road applications. they have been concerned about messing up a beam and or installing them wrong. so i hope this will help with any questions people may have regarding this.
for starters this is the adjuster
this is the main piece that you will be welding into the beam, its just a new center section thats clearanced to allow for movement.
this is the aluminum clamp thats one of 2 pieces that work to hold the torsions in place while your off roding
this is the center piece that pivots in the center piece, its what changes the angle of the torsions.
this bolt is to clamp the pivot point to the torsions and to hold the nut that tightens down onto the aluminum clamp.
and this is the final piece, the actual adjustment screw that you use to keep the pre-load from just moving that clamp all the way down. and so you can turn the front end up even with weight on it.
now at this point im going to assume you have your beam off and broken down to just the bare beam. at this point i recommend cleaning it up a little bit. these things tend to pick up a lot of road tar and dirt and fluids from old steering boxes and brakes and what not, so a good wire brush on a grinder will take most of it off. and a hand wire brush will get in the cracks and smaller areas you cant reach. i also took off some thick tar with a paddle wheel, i then used the same paddle wheel to clean the area i would be welding on better and i used it to get a nice clean welding area along the shock tower seams.
now the first thing i would do at this point (because its clean and because you've got the welder out) is to trigger weld the seams all the way around the shock towers, this is not necessary but its a good thing to do if you plan on any heavy off roding, these have a tendency to split and i myself would rather weld them now while the metal is bare and all the stuff is out.
you don't need a big weld just decent penetration to make sure that you get it together.
don't worry if the welds are kind of bubblegumed and not perfect its a hard place to weld, you can grind these down a little bit to clean it up.
now at this point you can start on the adjusters or do what i did and weld in gussets to the towers for some more beam prep.
Adjusters:
when starting the adjusters you want to only do one at a time to make sure the beam stays aligned. so you can do this on a table, the floor or in a vice like i did, just get the beam accessible and then hold up the main adjuster piece and line up the middle with where the grub nut is on the beam and mark either side. with a sharpie and then cut.
for cutting i would recommend a pipe cutter it will work the best but i dident have one so i used a sawz-all and you could also use a chop saw or grinder with a cutting wheel (just make sure you cut "inside" your marks) remember that its better to have to much than to little, you can always take more off if the adjust dosent fit the first time. but you just want a tiny bit of space on both sides for the weld.
now this is the part ive sensed people having a problem with. the angle of installation.
here in this picture if you look inside the main body of the adjuster you can see the pivot point. on the pivot point on the bottom is a grub nut that will hold the piece on the torsions when you install them into the beam with it on them. you want this to be at almost the same placement as the factory grub nut which is almost on the bottom of the beam. because being put there will allow the torsions when installed to give the trailing arms factory angle so you have a starting point to either lower or raise the front end.
its kind of hard to see, bottom left sticking out of the aluminum pivot point.
no to raise you want that grub nut in the stock place and you want to unscrew the adjusting bolt all the way out and move it up to where it meets the bolt that holds the pivot point insertion in place
like this
this allows for the front end to start at stock and you to utilize all 3inches of possible lift/ pre-load.
now if you were to install the adjusters to lower the car you would do this
the adjusting bolt turned all the way in and the grub nut in the stock position and the main body moved up to it, so it starts at stock and instead of screwing in to adjust you would screw out so that it would start at stock and work its way down.
now once your sure of where it goes hold it in place and mark it with a sharpie. just a line on each side going from beam over the gap to the adjuster so you have a reference. then dismantle the adjuster so that you just have the main body, put it in the gap and line it up with your marks and weld it in. start with just a tack on one side so you can make sure it will line up then tack the other side and then do the same on the back side a few times, then finish the weld
now once that one is welded in and cooled down a little bit flip the beam over and repeat on the other tube. and the only thing you have to do this time is just make sure that you get it at the same angle that you installed the first one.
and your finished!
later i can ad to this thread and show you how to install the torsions and then adjust the beam when its in the car. i hope this helped any of you who had questions regarding this. feel free to ask any more questions.
*edit*
due to issues regarding removing needle bearings, the races, the zerks and clearanceing a stock beam off all the junk in there, i recommend that you place the center rotation section into the adjuster as you weld them into the beam, just spray them down with some anti weld splatter stuff and you will be good to go. i always had installed these on custom beams made from raw tubing and i never had issues getting them in with the torsions but this time, ooh god the pain, i basically had to cut this thing back in half to fix it.
luke
Last edited by runslikeapenguin on Fri Oct 17, 2008 1:31 pm; edited 2 times in total |
|
Back to top |
|
 |
bajabugnut Samba Member

Joined: February 01, 2006 Posts: 90 Location: Pottstown Pa
|
Posted: Sun Mar 30, 2008 1:54 am Post subject: |
|
|
runslikeapenguin,
Thank you for the time that it took you to do that, very informative to those who may need that bit of info, I elect this as a sticky or is it already one.
It makes me feel better that I was able to figure that out on my own, it only took me several hours of just staring at it. Whats weird is I pretty much did what you did. |
|
Back to top |
|
 |
turnaround89 Samba Member
Joined: June 05, 2006 Posts: 493 Location: Rockford, Illinois
|
Posted: Sun Mar 30, 2008 9:19 am Post subject: |
|
|
thank you so much, i second the vote for a sticky. _________________ 1971 Baja Bug
1972 Porsche 914 |
|
Back to top |
|
 |
bajahucks Samba Member

Joined: March 04, 2008 Posts: 733 Location: north sandiego
|
Posted: Sun Mar 30, 2008 9:25 am Post subject: |
|
|
very,very good post man. thanks for the time. a plus |
|
Back to top |
|
 |
jps1145 Samba Member

Joined: March 16, 2005 Posts: 654 Location: Tehachapi, CA
|
Posted: Sun Mar 30, 2008 9:49 am Post subject: |
|
|
Nice work RLP. I would add to draw a line along each tube where the orignial grub screw was that will extend past the section you will cut out. that way you still have a stock reference point. _________________ Tehachapi, CA
'69 Baja
Vintage Funco single seater
My Baja |
|
Back to top |
|
 |
Yellermanx Samba Member

Joined: November 04, 2004 Posts: 1242 Location: Florida
|
Posted: Sun Mar 30, 2008 10:22 am Post subject: |
|
|
On a ball joint beam they are not installed at the same angle as in this picture.
|
|
Back to top |
|
 |
HamburgerBrad Je suis Napoléon!
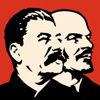
Joined: February 21, 2003 Posts: 6957 Location: SoCal
|
Posted: Sun Mar 30, 2008 10:47 am Post subject: |
|
|
Yellermanx wrote: |
On a ball joint beam they are not installed at the same angle as in this picture. |
right. if you were to look at a fully assembled stock beam, you would notice that the arms are not parallel. if they were, then yes, you would install the adjusters at the same angle to eachother. However, turning the lower adjuster screw just a little bit further than the upper adjuster will accomplish the same thing.
another note i would like to add, is that since the adjuster bodies are made out of a standard steel tubing with that weld going down the inside, i always take the time with a small grinder to clean up the inside and make sure that aluminum pivot piece rotates freely.
Also, do not forget to clean the metal shavings out of your beam once the center is removed add more grease to the beam once you've finished your installation. _________________ OGST | CU05 | OGJHC
1970 baja|1953 oval
Wanted: two beat up, ugly, curb rashed 6" phone dial wheels |
|
Back to top |
|
 |
HamburgerBrad Je suis Napoléon!
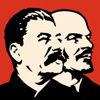
Joined: February 21, 2003 Posts: 6957 Location: SoCal
|
|
Back to top |
|
 |
Dale M. Samba Member

Joined: April 12, 2006 Posts: 20805 Location: Just a tiny bit west of Yosemite Valley
|
Posted: Sun Mar 30, 2008 12:11 pm Post subject: |
|
|
One point and maybe I just did not see it in tutorial is to scribe a line along beam (horizontally) at center of grub screw (before cut) .... It is simply a line of reference so you can orient grub screw (in adjuster) to same location as "stock" grub screw.... this will also assist in determining if you are getting a lower position ( most of oval opening in adjuster tube below line) or a raised position (most of oval opening in adjuster tube above line). This only works for K&L front end....
Dale _________________ “Fear The Government That Wants To Take Your Guns"
"Kellison Sand Piper Roadster" For Street & Show.
"Joe Pody Sandrover" Buggy with 2180 for Autocross (Sold)
============================================================
All suggestions and advice are purely my own opinion. You are free to ignore them if you wish ... |
|
Back to top |
|
 |
runslikeapenguin Samba Member
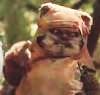
Joined: August 07, 2005 Posts: 4674 Location: Federal way WA
|
Posted: Sun Mar 30, 2008 12:42 pm Post subject: |
|
|
HamburgerBrad wrote: |
Yellermanx wrote: |
On a ball joint beam they are not installed at the same angle as in this picture. |
right. if you were to look at a fully assembled stock beam, you would notice that the arms are not parallel. if they were, then yes, you would install the adjusters at the same angle to eachother. However, turning the lower adjuster screw just a little bit further than the upper adjuster will accomplish the same thing.
another note i would like to add, is that since the adjuster bodies are made out of a standard steel tubing with that weld going down the inside, i always take the time with a small grinder to clean up the inside and make sure that aluminum pivot piece rotates freely.
Also, do not forget to clean the metal shavings out of your beam once the center is removed add more grease to the beam once you've finished your installation. |
yeah cleaning the inside will be kind of an issue, i have a round paddle wheel that i use to hone out the inside of these gate bearings i make for a friends dad that i was going to use, i just need to make an extension. _________________ never forget 1-31-07 |
|
Back to top |
|
 |
Yellermanx Samba Member

Joined: November 04, 2004 Posts: 1242 Location: Florida
|
Posted: Sun Mar 30, 2008 1:03 pm Post subject: |
|
|
Just another way.
I wanted mine to adjust up and down equally from stock height. I counted how many turns it took to move the adjuster from one extreme to the other. I believe it was 14 but it was a long time ago. If it was 14 I did half of that, 7 and locked the adjuster.
Before I took the leaves out of the beam I placed a piece of tin between the center leaves at the end and marked the tube where it was. I did it at both ends just to be sure.
I cut the center out and placed the adjusters in then put the leaves in then put tin in between the leaves and lined it up with the marks then tacked it.
I did it this way because the first set I did I measured twice then welded wrong anyways.  |
|
Back to top |
|
 |
runslikeapenguin Samba Member
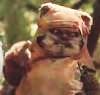
Joined: August 07, 2005 Posts: 4674 Location: Federal way WA
|
Posted: Sun Mar 30, 2008 2:20 pm Post subject: |
|
|
Yellermanx wrote: |
Just another way.
I wanted mine to adjust up and down equally from stock height. I counted how many turns it took to move the adjuster from one extreme to the other. I believe it was 14 but it was a long time ago. If it was 14 I did half of that, 7 and locked the adjuster.
Before I took the leaves out of the beam I placed a piece of tin between the center leaves at the end and marked the tube where it was. I did it at both ends just to be sure.
I cut the center out and placed the adjusters in then put the leaves in then put tin in between the leaves and lined it up with the marks then tacked it.
I did it this way because the first set I did I measured twice then welded wrong anyways.  |
couldent you have just put the grub nut on the center piece in stock location like i was saying and then just install the adjustment screw half way screwed in instead of all the way up or down. _________________ never forget 1-31-07 |
|
Back to top |
|
 |
dustymojave Samba Member
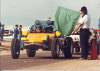
Joined: January 07, 2007 Posts: 5820 Location: Lake LA, Mojave Desert, SoCal
|
Posted: Fri Oct 17, 2008 9:12 am Post subject: |
|
|
Hey RLAP! Some of the photobucket links are broken from your nice little tutorial. _________________ Richard
Offroading VW based cars since 1965
Tech Inspection 1963 - 2012 SCCA/SCORE/HDRA/MORE/MDR +
Retired from building Bajas, Fiberglass Buggies and Rails in the Mojave Desert. Also Sprints & Midgets, Dry Lakes, Road Race cars. All types New and Vintage
SoCalBajas Member
Kicked Cancer's A$$...1st and 2nd round...Fight ain't over yet. |
|
Back to top |
|
 |
runslikeapenguin Samba Member
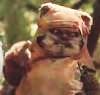
Joined: August 07, 2005 Posts: 4674 Location: Federal way WA
|
Posted: Fri Oct 17, 2008 1:22 pm Post subject: |
|
|
dustymojave wrote: |
Hey RLAP! Some of the photobucket links are broken from your nice little tutorial. |
shoot i was messing with my photobucket, ill fix that. _________________ never forget 1-31-07 |
|
Back to top |
|
 |
xirxious Samba Member
Joined: November 12, 2007 Posts: 665 Location: Seattle
|
Posted: Sun Oct 19, 2008 3:43 am Post subject: |
|
|
I've seen people widen beams and use 2 on each tube. Is that because they have to use 2 sets of bars and cut them a little longer than in half? |
|
Back to top |
|
 |
HamburgerBrad Je suis Napoléon!
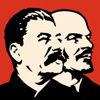
Joined: February 21, 2003 Posts: 6957 Location: SoCal
|
Posted: Sun Oct 19, 2008 9:22 am Post subject: |
|
|
xirxious wrote: |
I've seen people widen beams and use 2 on each tube. Is that because they have to use 2 sets of bars and cut them a little longer than in half? |
that's it. I do it by cutting the stock leaves exactly in half and re-locating the inner dimple on the torsion leaves, that way you don't need an extra set of torsion leaves. _________________ OGST | CU05 | OGJHC
1970 baja|1953 oval
Wanted: two beat up, ugly, curb rashed 6" phone dial wheels |
|
Back to top |
|
 |
redcavyguy Samba Member
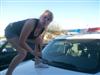
Joined: February 17, 2008 Posts: 91 Location: Houghton Lake, MI
|
Posted: Sun Oct 19, 2008 12:43 pm Post subject: |
|
|
hows the ride quality compared to using 2 sets of leaves and using the stock dimples. i have not ever tried just using one set and re-drilling the dimples. |
|
Back to top |
|
 |
runslikeapenguin Samba Member
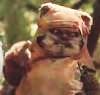
Joined: August 07, 2005 Posts: 4674 Location: Federal way WA
|
Posted: Sun Oct 19, 2008 1:57 pm Post subject: |
|
|
redcavyguy wrote: |
hows the ride quality compared to using 2 sets of leaves and using the stock dimples. i have not ever tried just using one set and re-drilling the dimples. |
ive heard that its a bit better, i had a 6 over balljoint beam on a car for a short time that was done like that and it rode pretty well, until i put it into a wall but i dident even have i adjusted up and it stood up well and it seemed to cycle a lot smoother. but seeing as it dident last me a day i never did any more testing  _________________ never forget 1-31-07 |
|
Back to top |
|
 |
HamburgerBrad Je suis Napoléon!
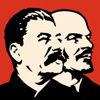
Joined: February 21, 2003 Posts: 6957 Location: SoCal
|
Posted: Sun Oct 19, 2008 8:05 pm Post subject: |
|
|
redcavyguy wrote: |
hows the ride quality compared to using 2 sets of leaves and using the stock dimples. i have not ever tried just using one set and re-drilling the dimples. |
i wouldn't be able to compare, since i've never used the same suspension components on a stock with setup vs a re-drilled. I would think it's comparable since the torsion leaves aren't really being shortened much (only about 1/2") _________________ OGST | CU05 | OGJHC
1970 baja|1953 oval
Wanted: two beat up, ugly, curb rashed 6" phone dial wheels |
|
Back to top |
|
 |
VIN Samba Member

Joined: June 01, 2006 Posts: 941 Location: phoenix
|
Posted: Mon Oct 20, 2008 11:23 am Post subject: |
|
|
when you guys re-drill the dimples, do you use a standard taper drill bit?? the factory dimples are alot sharper angle than the standard drill bit. i noticed that when i was narrowing my beam on the street car. |
|
Back to top |
|
 |
|