Author |
Message |
blacka1vw Samba Member

Joined: September 11, 2013 Posts: 89 Location: N. Central PA
|
Posted: Thu Jan 25, 2024 5:12 am Post subject: Re: Rusty 65 SC restoration |
|
|
Hey Ken Great build! Your work is spectacular. I’m working on a truck project myself and I’m looking for a dimension I was hoping you could pull if not too late? I’m just looking for the length from bottom hinge bolt to the bottom lip of the a-pillar on the extended lip part. If you haven’t already closed that area up. Thanks for posting all your work up like this it’s a great help to others!! _________________ 64 SC truck.
71 Beetle -Skyy
71 Super -Sweet pea
73 Bus
79 Bus -Tic Tak
86 Cabriolet |
|
Back to top |
|
 |
Kb65single Samba Member
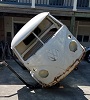
Joined: July 24, 2019 Posts: 273 Location: Obxnc
|
Posted: Thu Jan 25, 2024 12:14 pm Post subject: Re: Rusty 65 SC restoration |
|
|
blacka1vw wrote: |
Hey Ken Great build! Your work is spectacular. I’m working on a truck project myself and I’m looking for a dimension I was hoping you could pull if not too late? I’m just looking for the length from bottom hinge bolt to the bottom lip of the a-pillar on the extended lip part. If you haven’t already closed that area up. Thanks for posting all your work up like this it’s a great help to others!! |
blacka1vw
I would be happy to get that info that you requested except... I am currently in Tuscon AZ and will be there until late Feb. sorry. The other except... is that I have already closed that area up, sorry again.
What I can tell you is that the " length from of the bottom hinge bolt to the bottom lip of the a-pillar on the extended lip part" will ultimately be determined by the inner valance AND the inner valance "ends" that help form the bottom closing triangle of the 3-part a-pillar. I was worried about that length also, but when I got the inner valance in, I knew that I would either have to shorten or lengthen that part to make the inner valance "ends" fit. Hopefully it will be too long, cutting it shorter is easier than adding length. I used funky green panels, so I didn't have control of the size of the panel, and I was making the assumption that they are the correct size as the original (sometimes there not). You can compare the dogleg and a-pillar in that picture to see if you are in the ballpark. I don't have a picture of where you are at in this process, but I hope that explanation helps, if it doesn't continue to ask me questions and send pictures. Since you are located in central PA, I'm assuming major rust, hopefully I'm wrong.
Ken |
|
Back to top |
|
 |
Kb65single Samba Member
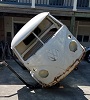
Joined: July 24, 2019 Posts: 273 Location: Obxnc
|
Posted: Fri Jan 26, 2024 11:09 am Post subject: Re: Rusty 65 SC restoration |
|
|
The inner valance was frustrating me because the aftermarket replacement was protruding past the front nose skin. Didn't want to make a cut that I would regret later so I decided to avoid the area all together. With that, I decided to revisit an area that I avoided a while ago, the rear apron.
My rear apron had some issues that I thought I could handle with a little effort. It was not original to the bus but was included in the sale of the bus. The rear apron was made in 3 large pieces and a few smaller sections.
The most obvious damage was a dent that was behind the level of the engine lid. Luckily my engine lid was not dented and is original to the bus. Don't know how the dent happened but it's there.
The other issue/dent was that someone beat the piss out of the inner panel of the apron. I guess that metal provides a heat barrier that protects the exterior paint. Don't know the reason for the beating, maybe an aftermarket header or muffler that needed more clearance.
The only and easiest way to solve both panel problems was to separate the inner panel from the outer. The spot welds were pretty small and more importantly easy to get to.
When the inner panel was removed, I could beat the piss out of the panel in the opposite direction to straighten it back up. With all of the first (ball peen) pounding on this panel the metal was really getting stretched when I started to straighten, and I realized that I would have to make a new one. Replicating the stamped holes that would trap the cylinders was met with multiple failures. It was at that time that I abandoned/avoided the apron restoration only to pick it back up later with new eyes now.
Found out the secret of how the bolts that attach the rear apron, don't collapse the two layers when it gets bolted to the bus. The metal cylinders in the picture are not welded in place but trapped in between the two layers of metal. Both layers of the apron have the hole metal stamped toward the cylinders; sort of like making drain holes in the doglegs.
With the two layers separated, I removed the black paint with a wire wheel on an angle grinder followed by a fiber disk on a drill. The clean-up time gave me hours to plan the dent straightening and the extra exhaust cutout repair. There was also rust damage on the rubber seal channel that needed attention.
|
|
Back to top |
|
 |
blacka1vw Samba Member

Joined: September 11, 2013 Posts: 89 Location: N. Central PA
|
Posted: Sat Jan 27, 2024 7:59 pm Post subject: Re: Rusty 65 SC restoration |
|
|
Hey Ken. My truck is definitely a rust project although I don’t think a salt truck. It’s got a good solid frame but it needs most the typical metal replacement on the body Luckily I got the truck with a bunch of funky green metal with it. I don’t got my a pillar close out panels yet but you have perfectly explained how that comes together and that makes perfect sense to me now. It’s so awesome to have a thread to follow along. Thanks again keep up the great work and posting it! _________________ 64 SC truck.
71 Beetle -Skyy
71 Super -Sweet pea
73 Bus
79 Bus -Tic Tak
86 Cabriolet |
|
Back to top |
|
 |
Kb65single Samba Member
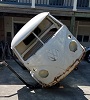
Joined: July 24, 2019 Posts: 273 Location: Obxnc
|
Posted: Sun Jan 28, 2024 11:56 am Post subject: Re: Rusty 65 SC restoration |
|
|
blacka1vw
Thanks, glad I could help.
First thing to repair was the dent near the mounting holes on the driver's side of the apron.
That area had three 20-gauge thicknesses of metal. The bottom section (where the exhaust exits) has a 90deg bend. The top section (where the rubber seal channel is) has a 90deg bend that is folded over the 90deg bend on the bottom. Getting all that stretched metal to move with hand pressure alone was difficult/impossible. Decided to make a couple of cuts. Didn't cut all the way through the exterior leading edge so I could monitor the movement with a straight edge. Used the Dremel 1/16" disk. Sandblasted the weld areas.
With that all welded and ground flat, I was happy with the improvement. Had to recut one area because it shrunk the metal too much.
Exhaust hole repair, which I see from the apron for sale section of the classifieds, is a popular feature. Mark out a full metal thickness section of what appears to be a hastily manufactured pee shooter exhaust port.
Make a repair section and tack it in.
Supported the repair section with a straight bar and weld/grind smooth.
The engine rubber seal channel was badly damaged from rust in one section. If you have seen the other repairs/replacement sections of the other engine compartment seal channels (page 5 and 6), this was a new twist (bending in a different plane). Made a straight section first then took a 1/2" long bar that slid inside the channel. Pinned that in the vise carefully and gradually bent the straight channel to match the repair area. Cut the rusty metal out and fit the new section in.
Sandblast and rustproof the mating surfaces. Then weld them in.
|
|
Back to top |
|
 |
Kb65single Samba Member
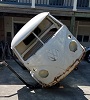
Joined: July 24, 2019 Posts: 273 Location: Obxnc
|
Posted: Wed Jan 31, 2024 11:15 am Post subject: Re: Rusty 65 SC restoration |
|
|
After those repairs, I sandblasted the inner and outer pieces of the apron. The outer section had one questionable area that was thinned by rust. Sand blasting would reveal how good or bad that area was. The inner section needed to be cleaned up because I wanted to use parts of the original to make a new inner panel. Eastwoods Afterblast was applied after the blasting.
Made a new inner panel. Very easy straight bends and a great original piece to copy. The most frustrating part was the total length of the piece laid out flat was 39". Once again, my choice of a 3-foot metal brake instead of a 4 foot, came back to haunt me. I solved the problem by welding on one of the ends instead of it being bent all in one piece. If you want to see the distortion of the panel, look at the picture of the original, the bottom edge is bowed off the plywood in the middle.
The stampings problem was solved by harvesting them from the original panel and grafting them in the new.
The sandblasting of the outer panel showed pin holes and paper-thin metal.
Cut out the area and made a donor section.
In order to weld a flat piece of metal flat, it needed the correct support.
Traced the butt weld area and used my router to make a channel so the wood wouldn't burn when I welded.
Pinned the whole area down on a thick flat piece of metal and welded away. Then grind and smooth. Bolted the inner to outer while welding to help keep things straight.
Next was welding the inner to the outer. Tacked the metal cylinders to the outer so they wouldn't move around. Then rustproofing and assembled the pieces.
Welded the inner panel flange that welds close to where the rubber seal is first. Clamped a piece of angle iron to the exhaust portion of the outer section to help keep it straight.
Then I bolted the apron to the bus. I could then make any adjustments to the outer skin of the apron if necessary. Glad I did it because it made the apron contours match the d-pillar areas better. Tried in the rubber seal also.
Final product from a metal standpoint.
|
|
Back to top |
|
 |
BarryL  Samba Member
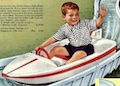
Joined: November 01, 2004 Posts: 14274 Location: Casa de Oro, California
|
Posted: Wed Jan 31, 2024 6:48 pm Post subject: Re: Rusty 65 SC restoration |
|
|
Majestic work. I love the anti-burn-wood trick. |
|
Back to top |
|
 |
Kb65single Samba Member
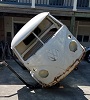
Joined: July 24, 2019 Posts: 273 Location: Obxnc
|
Posted: Wed Feb 07, 2024 2:29 pm Post subject: Re: Rusty 65 SC restoration |
|
|
BarryL
Thanks for the comment. The trick works pretty well, and I don't like the wood smoke inside the garage (wintertime).
Next up is the Inner valance; can't avoid it anymore. I attempted to fit the inner valance many times. Back on page 15 of the build was the first time trying it in. The holes for bumper brackets were to narrow. On the driver's side the valance stuck out further than the front nose skin metal. After all the bracing of the cab, the dogleg work, the horn bracket repair, I still had the same problem. Searched the forums for solutions and one person had a similar problem. His solution was to pie cut and reweld the valance to match the contour of the nose skin. That sounded like a good idea if it would solve the problem. Matching those contours would help (or wouldn't hurt) the final step of welding the lower 6 inches of the front nose skin. It made sense to me.
Made a cardboard template first.
Transferred that to a piece of underlayment (1/4" plywood)
Sanded the wood to fit the skin.
Compared the profile to the aftermarket replacement. Passenger side was fair but the driver's side had a 6mm change of contour from the middle centerline to the outside of the valance flange. That flange would eventually be welded to the outer valance, inner valance ends, and a-pillar. Common sense told me, they all had to play well with each other.
Driver's side.
Passenger side.
While trying in the valance it was always harder to get the driver's side in than the passenger side. After staring at it a while I noticed that the driver's side frame bracket of the inner valance was welded on crooked.
The frame bracket should be welded flat across the entire width of the valance.
The original bracket was welded on differently than the green one. Compare the overlap of the green to original. Slanted overlap (original) to even overlap (green). The crooked welding pushed the arched valance up, so it pushed against the headlight support panel making it hard to get in and possibly twisting it. So, a few modifications of the inner valance were needed.
|
|
Back to top |
|
 |
Kb65single Samba Member
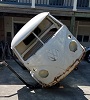
Joined: July 24, 2019 Posts: 273 Location: Obxnc
|
Posted: Sun Feb 11, 2024 2:31 pm Post subject: Re: Rusty 65 SC restoration |
|
|
Decided to call the Gerson representative to voice my concerns. Sent him pictures and the normal response was again " I can refund the money and you can send it back. He said that he could send another one but couldn't guarantee that it would be any better than the one I had. He voiced some concerns about the quality of the workers at the Columbia facility. He suggested that I should buy the same part from another vendor. Maybe he was having a bad day?
So, although it would be a lot of work, I asked him to send me new brackets because I had to move the holes for the bumper brackets, and I could weld the brackets on straight myself. Long story, but I also wanted more spring brackets for the engine lid and treasure chest doors so I could have two on each door(more on that later). He sent the valance and spring brackets at no charge.
Cut the old bracket off. Note: no primer or paint behind. Minor rust starting to form.
Welded the new one on with paint between.
Changing the valance frame bracket made the valance easier to take in and out but did not change the arched contour. Marked the plywood pattern of the front skin on my work table (load bed of SC).
Pie cut the valance to match the front skin contour.
The passenger side needed less adjustment.
Pie cut the valance 2 more times to get both sides to match the contour of the outer skin. With all that, the valance would still extend past the outer skin. The last resort was to cut the end of the frame back. Reluctantly I did that. I could have moved the flange that supports the outer valance toward the rear of the bus, but two five-foot welds and all that grinding was too much. Moved both drivers and passengers frame ends.
With that decision made, I bolted the inner valance along the top to the headlight support panel. I used five 5mm bolts and nuts to secure it temporarily before final welding. I bolted the inner valance frame brackets to the frame with the same size nuts and bolts. Those bolts fit snugly in the holes with minimum movement. I could then fit the valance "ends" with confidence that the valance would not move. I then fit the valance ends and secured them with machine screws and nuts. I still wasn't confident that what I was doing was right, especially the shortening of the frame ends. Bolting was reversible and if I needed to move the positions of things I could. I wanted to get the outer valance fit to check that the front skin would fit all the way (a-pillar to a-pillar) outside of the outer valance.
|
|
Back to top |
|
 |
Kb65single Samba Member
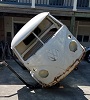
Joined: July 24, 2019 Posts: 273 Location: Obxnc
|
Posted: Tue Feb 13, 2024 4:22 pm Post subject: Re: Rusty 65 SC restoration |
|
|
Fitting the a-pillar bottoms/inner valance ends.
Initial try-in of the passenger valance end. Both the top and bottom of the flange that mates to the outer valance were way to far forward. The top flange that pushes against the a-pillar would not allow the valance end to fit into the entire length of the inner valance.
The bottom triangle of the a-pillar didn't match up very well.
Cut off the top and bottom flanges of the "ends" that weld to the outer valance. Bottom was cut at the black line. Cutting the top one allowed the body of the "end" to fit all the way inside the inner valance. Then machine screws and bolts to hold it in place.
Sectioned the triangle so it would mate up to the hinge side of the a-pillar properly.
Welded and smoothed all the cuts. The top flange of the valance end was difficult to fit because it did not have a blending point at the end of the a-pillar. I would finish fitting that when the outer valance was close to its final placement.
Did the same thing to the drivers side. Initial try-in was again way to far forward.
Cut both top and bottom flanges off and welded the bottom on; blending it, on the inside with the inner valance flange and on the outside, to where the outer valance plug welds to the a-pillar. Now I could fit the outer valance and modify the top flange to blend in.
|
|
Back to top |
|
 |
chrisflstf Samba Member

Joined: February 10, 2004 Posts: 3450 Location: San Diego
|
Posted: Tue Feb 13, 2024 6:39 pm Post subject: Re: Rusty 65 SC restoration |
|
|
Looks great  |
|
Back to top |
|
 |
Kb65single Samba Member
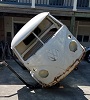
Joined: July 24, 2019 Posts: 273 Location: Obxnc
|
Posted: Sat Feb 17, 2024 3:59 pm Post subject: Re: Rusty 65 SC restoration |
|
|
chrisflstf
thanks again
Outer valance try-in...
The bumper brackets helped center the valance and allowed me to start bending the ends at the a-pillar. The outer valance was a bit long (that's a good thing) so I had to trim the 90-degree piece that eventually gets welded to the bottom of the nose skin. When I cut the original outer skin, I measured up from that lip across the entire width of the bus. I kept the same measurement when using the green metal (measuring up from the 90-degree piece to the edge of the cut nose skin).
Used clamps at first but that wasn't repeatable. Switched to sheet metal screws starting at the midline and working my way evenly toward both a-pillars.
As I was adjusting/fitting the outer valance I noticed that the ends of the valance were acting like the piece was getting crooked. Turns out that, although the width of the outer valance was the same from a-pillar to a-pillar, the 90degree flange that is spot welded to the valance changed height from one side to the other.
Passenger side measurement from 90deg piece to top of valance was 63mm.
Drivers side 66mm.
3mm is a lot when I am working with metal. I'm pointing this out, so others won't make the same assumption that I did. I guess I'm just old school and never thought that anyone would do that kind of work.
I'm glad I didn't fit that piece using the top of the valance and the cut nose skin. I would have been pissed. I did not change the spot welds on this part. The mistake in production will probably get hidden by the front bumper. With the outer valance fit the front skin metal was now forward of the outer valance from a-pillar to a-pillar. Next is welding it all together and never assume aftermarket parts are correct even if they are painted green,silver,red or black.
|
|
Back to top |
|
 |
blacka1vw Samba Member

Joined: September 11, 2013 Posts: 89 Location: N. Central PA
|
Posted: Sat Feb 17, 2024 5:38 pm Post subject: Re: Rusty 65 SC restoration |
|
|
Dang! Good catch. I have the same green parts. I’m gonna take some extra measurements now! _________________ 64 SC truck.
71 Beetle -Skyy
71 Super -Sweet pea
73 Bus
79 Bus -Tic Tak
86 Cabriolet |
|
Back to top |
|
 |
pyrOman Fire Master
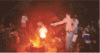
Joined: July 21, 2003 Posts: 12410 Location: Over 2002 posts deleted!
|
Posted: Sat Feb 17, 2024 6:03 pm Post subject: Re: Rusty 65 SC restoration |
|
|
I’ll say it again! No two buses are exactly alike, even if they have serial numbers just one apart! You will always have to make some adjustments. The last front skin I replaced had missed contacts on over half the weld spots between the inner and outer valances. Not to mention the kind of life these buses had before you got to them.  _________________ Some people are so busy being clever they don't have time enough to be wise. |
|
Back to top |
|
 |
70bus  Samba Member
Joined: July 15, 2004 Posts: 581 Location: P.O.
|
Posted: Sat Feb 17, 2024 6:32 pm Post subject: Re: Rusty 65 SC restoration |
|
|
You could open a shop and make a fortune doing concours work like that. Who notices 3mm? You do! _________________ Craig K
70 Neunsitzer
65 Pritschenwagen
"If Von Dutch was alive, he'd walk in there with a pistol and shoot these people."
-Robert Williams |
|
Back to top |
|
 |
Kb65single Samba Member
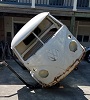
Joined: July 24, 2019 Posts: 273 Location: Obxnc
|
Posted: Tue Feb 20, 2024 9:24 am Post subject: Re: Rusty 65 SC restoration |
|
|
blacka1vw
Yes, good on measuring, it could save you some do overs and hair loss.
pyr0man
I agree with you 100%
70 bus
Thanks for the kind comments. Just trying to get things to fit.
Now that the outer valance is close, I can add the top flange of the inner valance end/part 3 of the 3-piece a-pillar. Had to thin the width of the tab that welds to the a-pillar so that it could move toward the door hinge. A lot of trial grinding to get it to fit. Hard to get a picture with the outer valance in place.
With the outer valance gone it's a lot easier to see the passenger side modifications.
Had to do the same thing on the driver's side.
Welding the inner valance in place.
Kept the nuts and bolts in place during the welding. Sandblasted the areas where I had to reshape the flange that mates to the outer valance. The green paint tends to crack and peel when using a Vice-grip on it. Applied Eastwoods Afterblast to those surfaces. Painted the mating surfaces of the headlight support panel and inner valance and the frame ends and inner valance frame brackets. Drilled into the frame ends with a 3/16" bit to ensure good weld penetration just like the treasure chest floor and I-beams. Kept the inner valance ends on while welding.
Frame brackets needed a lot of welding. It was easier to put the welds on than it was taking them off. Tried to replicate what was previously there.
Easier was a relative term. Not my best side but getting to the driver's side top frame bracket was a challenge.
|
|
Back to top |
|
 |
Kb65single Samba Member
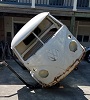
Joined: July 24, 2019 Posts: 273 Location: Obxnc
|
Posted: Thu Feb 22, 2024 9:11 am Post subject: Re: Rusty 65 SC restoration |
|
|
Next was welding the inner valance ends in. Painted the mating surfaces before welding.
I just guessed at the number of welds that attached the ends to the a-pillar and the inner valance. A lot of that area was damaged from rust. (Page 15) What was left of the original had quite a few. Since these attach the cab to the frame, I erred on the side of many vs few.
Painted the cavity created by welding the inner and outer valances together. Didn't grind any of the welds that were hidden in the cavity.
Put a gray topcoat on the inside.
And as usual you can never have enough clamps and vice-grips.
Weld the outer to the inner and the a-pillar. Front cab floor and lower 6 inches left
|
|
Back to top |
|
 |
Kb65single Samba Member
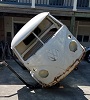
Joined: July 24, 2019 Posts: 273 Location: Obxnc
|
Posted: Sun Feb 25, 2024 2:38 pm Post subject: Re: Rusty 65 SC restoration |
|
|
Preparing for the lower 6-inch front skin replacement.
Decided to try to make my own 6-inch replacement panel. If it didn't work out, I could always contribute to the green panel research development fund. Sandblasted my original lower 6-inch piece where the V gets completed. There were a few pinholes and thin areas below the V. Using this part of the panel will help with matching the top part of the existing V. Will probably need to replace the metal below the V.
Cut out some flat stock 20-gauge metal that will compete the rest of the lower 6-inches on both sides of the V. Bent that flat stock 90degrees and will eventually use the shrinker/stretcher to form the matching arch of the top panel hopefully.
Then I started to think....
Welding the lower 6" of the front skin was going to potentially require some form of manipulation of the metal outward. (Hammer and dolly along the seam) Wouldn't it be better if the front floor was welded in. The only way that I could push out was if the headlight support panel was welded securely to the floor. With the inner-outer valances and doglegs welded to each other the door gaps shouldn't change. Fitting and welding the front floor first would allow me to push outward if needed and I could paint the back side of the headlight support panel before closing in the front skin. Sounded like a good idea to me so...
Out came the bracing in the cab. When the bracing came out the door gaps didn't change . and a lot easier to get into the cab.
|
|
Back to top |
|
 |
Kb65single Samba Member
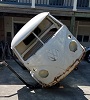
Joined: July 24, 2019 Posts: 273 Location: Obxnc
|
Posted: Mon Mar 04, 2024 7:31 am Post subject: Re: Rusty 65 SC restoration |
|
|
Last major panel dissection; the front floor.
A lot of spot welds to grind out. The area around the shifter and emergency brake was really hard to locate the position of the spot welds. The floor area around the shifter is sunken below the rest of the floor height. Heavy rust hid those spot welds.
Cleaning up the mating surfaces on the frame and perimeter areas that the floor will get welded to. Three areas of rust through to deal with on the perimeter. One on the headlight support panel and two on the wheel well panels close to the doglegs. Used some citric acid after reading some of the info in a samba topic about rust remediation. I liked the idea of it not being as toxic as other methods. Agitating the solution with a wire brush helped speed up the process. Using a soaked paper towel helped keep the solution on the metal. No chance I was going to sandblast, there are just too many hiding spots and hard areas to try to tape/seal up. Next time I'll know better.
Initial try in of the front floor. It was too big, and the presence of the heater/defrost pipe was complicating things. With the very real possibility of multiple try ins, it needed to go. 4 small welds to free up. 2 were visible and 2 were there when the front nose skin wasn't there. Used a mirror to direct a small grinding disk on the Dremel tool.
Fitting the floor will be a lot easier now.
|
|
Back to top |
|
 |
Kb65single Samba Member
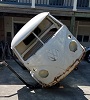
Joined: July 24, 2019 Posts: 273 Location: Obxnc
|
Posted: Tue Mar 19, 2024 7:28 am Post subject: Re: Rusty 65 SC restoration |
|
|
A little R&R with my wife's favorite place Aruba, led me to a shop along the water and a hat that I could not pass up. Bought the hat a couple of years ago but we went back recently, and I was hoping to buy another. Unbelievable machine stitching and two pockets on the sides, one zippered and one with Velcro. Pocket big enough for a credit card, door card or cash. Perfect hat for the beach. The shop was there but unfortunately no hats.
Time to get back to the SC.
Repaired the window that I created to fix the higher-than-expected rust on the a-pillar. Brushed some paint behind and as far up as I could reach.
Saved the piece that I cut out to fill it back in.
Weld grind and smooth.
Repairs to the perimeter borders of the front floor. Pin holes around the area where the dimmer switch wires enter the cab area.
Rust damage to the drivers wheel well flange needed repair.
Passenger side wheel well. Included the little dimple on the bottom edge. Now on to the front floor
|
|
Back to top |
|
 |
|