Author |
Message |
lmar Samba Member
Joined: September 18, 2014 Posts: 76
|
Posted: Thu Nov 30, 2023 12:40 pm Post subject: How To: Welding Floor Pans with what you got (120VAC Mig Welder) |
|
|
I am not a welder.
Just a DIY that has been self taught.
My first set of full pans did not turn out the way they should have. I will have to rework them.
Decided not to have a repeat with the second set of pans.
I've never seen this method explained so I will attempt to do so here.
Note - I am using a Lincoln MIG 140 with .030 wire I purchased from Crappy Tire in Canada. It is the ubiquitous 120 VAC welder. Don't try to do this with anything but solid core wire and shielding gas.
By all accounts it does not have the ability to dial in the amperage (You are given letters for current settings and numbers for wire feed).
Problem: You are trying to weld 1-1.2 mm pans to multi-ply sheet metal that forms the rigid backbone of the VW Beetle Frame (3-4mm). Heat control (or lack thereof) will be the major issue.
Step 1 - Make sure your holes in the pan are the correct size. 1/4 too small - weld fills hole before sufficient penetration. 5/16 seems to be the minimum size required. Don't go bigger or you will melt the edge of your pans. Most of the "flange/hole" tools I've seen come with a 1/4 diameter hole. Use it to position holes and then open them up using a Unibit (step/tree) drill.
Step 2 - Make sure you have sufficient edge distance such that the welds will not "bleed" off of frame edge. All bets are off. You want consistent geometry to minimize errors - not maximize them.
Step 3 - Make sure the edge of the new pan and frame are tight - no gaps. use any means possible to get the parts consistently tight. There are a plethora of ways to do this on the internet. I used jack stands on the outside edge of the pan (25-50mm higher) to support it and then rested my bodyweight (knees) on the pan as needed.
Step 4 - My Method - You need to to dump sufficient heat to allow for proper penetration of the frame ledge. Your only option is to select the highest letter setting (greatest current) and then adjust wire feed accordingly. Build a mock-up of the frame/pan and test your settings before attempting on the car.
Step 5 - Clip the MiG wire to remove the "ball" on the end of it. If you don't, each time you attempt to get to the bottom of the "hole" it will arc to the side and fill up the pan hole with minimal penetration. Note - if you start hearing pings as the welds cool - you are in trouble as this is the sound of the non-penetrating weld popping. (i.e. there are now two part instead of one).
Step 6 - I do not like weld thru primer at the bottom of the hole. I will spray both parts with it but remove the primer in the holes so that it is bare metal. I get better control of the arc starting at the center of the hole instead of where it wants to based on thickness/location of paint.
Step 7 - With the welder gun perpendicular to the pan aim for the center of the hole. When you pull the trigger make sure the wire hits the bottom of the hole (frame) - the object of the exercise is to get enough heat to melt the thicker frame. I do not move the gun but allow it to build up a volcano that protrudes 1-2 mm above the pan sheet metal.
Step 8 - If done correctly, you will suddenly see the volcano flatten and drop level with the pan sheet metal. Depending on how you biased the position of the wire - one side might be part of the puddle.
Step 9 - Once the puddle drops, immediately note where the edge of the hole hasn't melted and expand (move) the puddle in that direction. Think cloverleaf. As soon as you melt that area you need to get out before you overheat the thin sheet metal of the pan (and have to start chasing the weld).
Step 10 - It is important to get over the weld (position your helmet accordingly) so you can see what part of the weld puddle hasn't melted the edge of the pan hole. The cloverleaf motion allows you to move the puddle to the next area without overheating the thinner metal. Usually 2-3 cloverleafs are required to get a solid bead that has penetrated the frame and welded the thinner pan without burning through.
You have to move fast or you will build up weld material that won't add to the weld strength - but will have to be ground off. Its like drywalling, you only put as much on to fill the hole and blend the patch, while minimizing the amount of sanding required to get a blended surface).
I will pick every 3-4 hole to do this to. I will then come back later when things cool down and fill alternating holes. If I attempt to do every hole in sequential order - the residual heat build up and changes the process as time goes by.
The object is to have things consistent as possible for every welded rosette. This is especially important if you don't have the welding skills to compensate on the fly (that is why they are professionals).
This method works on cold frames/pans holes so it shouldn't matter where you start. It is all about heat control using what you have to get in and out as fast as you can with a proper rosette weld that fully penetrates the frame while filling in the hole without burning through the pan.
If you burn through the pan move the puddle to the other side to allow things to cool down and then move back. Gaps at the edges of your pan will guarantee burn through.
Once you get the hang of things - pan welding can be very therapeutic.
Again, before attempting this, mock things up and practice until you get the hang of the timing. You have to move fast once things are started. |
|
Back to top |
|
 |
beetlenut Samba Member
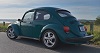
Joined: May 27, 2009 Posts: 2983 Location: RI
|
Posted: Thu Nov 30, 2023 4:44 pm Post subject: Re: How To: Welding Floor Pans with what you got (120VAC Mig Welder) |
|
|
That's exactly how I did my pans. Worked great. It's called plug welding. I used a Lincoln MIG 140 with .023 wire. _________________ scrapyards are for quitters
---------------------------------------
Wetstuff wrote: |
... I spend more time shaking it than directing it?! I get a pretty decent blast for 8sec. then have to shake it again. |
- Words to live by right there!
My 74 Super rebuild thread: http://www.thesamba.com/vw/forum/viewtopic.php?p=6507104#6507104 |
|
Back to top |
|
 |
Kafer_Mike Samba Member
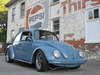
Joined: June 23, 2004 Posts: 348 Location: Noblesville, IN
|
Posted: Fri Dec 01, 2023 1:07 pm Post subject: Re: How To: Welding Floor Pans with what you got (120VAC Mig Welder) |
|
|
beetlenut wrote: |
That's exactly how I did my pans. Worked great. It's called plug welding. I used a Lincoln MIG 140 with .023 wire. |
Same here, but with a Hobart Handler 140. _________________ Kafer_Mike
Build 'em fast...or let 'em sit. |
|
Back to top |
|
 |
|