Author |
Message |
4Gears4Tires Samba Member
Joined: October 08, 2018 Posts: 4130 Location: MD
|
Posted: Mon Jul 07, 2025 8:33 am Post subject: Re: Big engine + NOT downshifting.... damages 4th gear |
|
|
With a Subaru motor, a Subaru trans is a pretty easy option. A WRX trans + adapter kit ends up being what a built Vanagon trans costs. If I knew I was going to end up spending $7k on my trans I would have sold it and used that money to fund a Subigears/Reversaru trans. _________________ '87 Syncro Ferric Oxyhydroxide Superleggera Edition
'85 Westy Sciuridae Domus Edition |
|
Back to top |
|
 |
GoEverywhere Samba Member

Joined: December 13, 2020 Posts: 859 Location: Portland, OR
|
Posted: Mon Jul 07, 2025 8:36 am Post subject: Re: Big engine + NOT downshifting.... damages 4th gear |
|
|
4Gears4Tires wrote: |
With a Subaru motor, a Subaru trans is a pretty easy option. A WRX trans + adapter kit ends up being what a built Vanagon trans costs. If I knew I was going to end up spending $7k on my trans I would have sold it and used that money to fund a Subigears/Reversaru trans. |
I put 540HP to the wheels on my last dyno pull so a standard WRX trans actually isn't strong enough for my build, I have to go with an STi 6 speed. That pushes the Subigears trans to $11k or so. Hefty chunk of change! I wish it had been an option when I built my 091, wouldn't have stung quite so badly to do it twice. But thats the price I pay for building stupidly overpowered vehicles I guess! |
|
Back to top |
|
 |
Sodo Samba Member
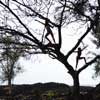
Joined: July 06, 2007 Posts: 10613 Location: Western WA
|
Posted: Mon Jul 07, 2025 9:16 am Post subject: Re: Big engine + NOT downshifting.... damages 4th gear |
|
|
This thread has a very specific technical topic.
Its purpose is to help those who are trying to get more miles from their expensive (over-driven) Vanagon transaxles.
Big engine + NOT downshifting.... damages 4th gear
It's kind of a complicated subject, and rather important to those with smokin' wallets.
I tried to find/post a cross-link where the problems (or longevity successes ) with the Subaru car-gearboxes (pushing Bricks) is being discussed.
But I don't know if anyone is actually discussing that.
That subject needs a thread doesn't it?
Longevity at this stage when nobody has any miles or forensics is unlikely anyway. They probably don't have 150,000, 250, 300k like our Vanagon gearboxes (yet) to discuss.
Longevity theory would likely disturb installation and fitment discussions.
If anyone knows where technical or forensics on the Subaru trans is being discussed please link. _________________
'90 Westy EJ25, NEW oil rings (!) 2Peloquins, 3knobs, SyncroShop pressure-oiled pinion-bearing & GT mainshaft, filtered, cooled gearbox.
'87 Tintop w 47k 53k, '12 SmallCar EJ25, cooled filtered original gearbox
....KTMs, GasGas, SPOT mtb
Last edited by Sodo on Mon Jul 07, 2025 9:59 am; edited 1 time in total |
|
Back to top |
|
 |
MarkWard Samba Member
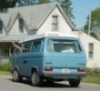
Joined: February 09, 2005 Posts: 18688 Location: Retired South Florida
|
Posted: Mon Jul 07, 2025 9:35 am Post subject: Re: Big engine + NOT downshifting.... damages 4th gear |
|
|
I enjoy these discussions, but don’t practice it personally. Much of my background knowledge is from road racing. There is never a free ride. Up power and torque, something else is going to require additional service.
The problem with the Vanagon transmission is there are only a handful of reputable rebuilders, wait times, shipping costs, new and used parts availability. Even worse with a syncro.
Adding pumps, fans, coolers, filters, seems like over engineering and more points of failure. Shifting out of forth to let the gear and bearing face relax just doesn’t fit in to our use. More frequent oil changes sure but if I have to go through my transaxle every 60,000 miles, for me it’s not a big deal. Not so much for others.
Racing, I had a transmission I had to go through every weekend. Once every 5 or so years not such a big deal. I’m not trying to derail this thread, just offering another point of view/use.
Lastly, while I have gobs of power and torque over stock, I don’t necessarily use it full time. And I’d like to know more about the main bearing retaining plate pictured above. Was that out of a syncro? If so, what accommodations had to be made? Member Alika I believe used to sell a better designed bearing retainer. |
|
Back to top |
|
 |
Sodo Samba Member
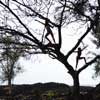
Joined: July 06, 2007 Posts: 10613 Location: Western WA
|
Posted: Mon Jul 07, 2025 10:15 am Post subject: Re: Big engine + NOT downshifting.... damages 4th gear |
|
|
MarkWard wrote: |
Shifting out of forth to let the gear and bearing face relax just doesn’t fit in to our use. |
I agree that if I tried to get my mom "to lube 4th gear," I would be awarded with a blank stare.
It's not to relax 4th gear,
it's a lubrication "effort" to counter a 4th gear lubrication deficiency that's been known for 20, 30 years (hence the creation of "VW South Africa oiling plates")
What conditions the deficiency occurs.... is lesser known. It's a STORM of oil vapor in there,
and YET,
an erosion phenomena occurs
....one that can only happen in the absence of oil.
We're certain its dry otherwise there would be no erosion.
I suspect the oiling plates (a popular mod) do throw oil up, but this oil only gets in upon downshift or decel.
And the oiling plates logically only throw oil at certain speeds + temperature-viscosities anyway,
two factors that we know nothing about.
This is mostly a long-distance, cruise-control steady-conditions problem.
There has to be a steady condition for the oil to deplete (to dry).
Steady, like "throttle mashed, no decel, no downshift"
Subject title says "Big Engine...."
If you have a WBX, this is of less importance because maybe you drive the van slower, and have to downshift often anyway.
But this lubrication deficiency was appearing back in the day long before big engines. It's just WORSE with big engines,
The owners mainly interested in this are those who have spent big bucks and somewhat understand gearboxes, metallurgical phenomena, or maybe they have a big engine & enjoy 80MPH in spite of their good sense.
Or had un-satisfactory longevity from a quality rebuilder.
The rebuilders themselves "should" be interested.
80mph is for short periods is OK..... but after lubrication has depleted, bad things are happening at any speed where any contact surfaces are dry (inside your gearbox).
The evidence is there. This type of erosion only happens when dry.
I suspect electricity increases the rate because more electricity is conducted when dry. _________________
'90 Westy EJ25, NEW oil rings (!) 2Peloquins, 3knobs, SyncroShop pressure-oiled pinion-bearing & GT mainshaft, filtered, cooled gearbox.
'87 Tintop w 47k 53k, '12 SmallCar EJ25, cooled filtered original gearbox
....KTMs, GasGas, SPOT mtb
Last edited by Sodo on Mon Jul 07, 2025 4:37 pm; edited 1 time in total |
|
Back to top |
|
 |
khughes Samba Member
Joined: July 13, 2013 Posts: 867 Location: Phoenix AZ
|
Posted: Mon Jul 07, 2025 12:00 pm Post subject: Re: Big engine + NOT downshifting.... damages 4th gear |
|
|
Sodo wrote: |
MarkWard wrote: |
Shifting out of forth to let the gear and bearing face relax just doesn’t fit in to our use. |
I suspect the oiling plates (a popular mod) do throw oil up, but this oil only gets in upon downshift or decel.
And the oiling plates logically only throw oil at certain speeds + temperature-viscosities anyway,
two factors that we know nothing about. |
Have you, or any other member, actually seen this problem arise with a tranny rebuilt using the oiling plates? _________________ '86 Westy FAS GenV Turbo (Marvin) |
|
Back to top |
|
 |
dougnlina  Samba Member

Joined: January 19, 2016 Posts: 296 Location: San Francisco, CA
|
Posted: Mon Jul 07, 2025 12:10 pm Post subject: Re: Big engine + NOT downshifting.... damages 4th gear |
|
|
khughes wrote: |
Have you, or any other member, actually seen this problem arise with a tranny rebuilt using the oiling plates? |
See my earlier post with photos specifically showing the 4th gear to bearing faces worn, this was in a tranny that has the oiling plates. _________________ "Grover" a '87 Syncro Poptop 1.8T
"Olive" a '60 Ragtop Beetle (retired) |
|
Back to top |
|
 |
AndyBees Samba Member
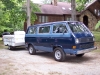
Joined: January 31, 2008 Posts: 2620 Location: Southeast Kentucky
|
Posted: Mon Jul 07, 2025 12:35 pm Post subject: Re: Big engine + NOT downshifting.... damages 4th gear |
|
|
Below, is a pic of the Front Main Shaft bearing (thrust side) after 90k miles and 14 years from the DK that was in my TDI Van. It doesn't appear to have been starved for oil.
Below, is a pic of the 4th Gear from the transmission. I never took a close-up pic of the bearing area inside the gear or the main shaft journal.
No doubt, this transmission would have benefitted from a cooling and filter system. _________________ '84 Vanagon Tin-top, ALH TDI, two trips to Alaska, 2014 & 16. 1989 Tin-top unmolested.
1983 Air-cool, 225k miles, 180k miles mine, seven trips to Alaska from 1986 thru 2003. 1975 Bay hopeful.
Last edited by AndyBees on Mon Jul 07, 2025 4:11 pm; edited 1 time in total |
|
Back to top |
|
 |
khughes Samba Member
Joined: July 13, 2013 Posts: 867 Location: Phoenix AZ
|
Posted: Mon Jul 07, 2025 4:02 pm Post subject: Re: Big engine + NOT downshifting.... damages 4th gear |
|
|
dougnlina wrote: |
khughes wrote: |
Have you, or any other member, actually seen this problem arise with a tranny rebuilt using the oiling plates? |
See my earlier post with photos specifically showing the 4th gear to bearing faces worn, this was in a tranny that has the oiling plates. |
I was afraid that was the answer. I missed mention of you having oiling plates. Thanks. _________________ '86 Westy FAS GenV Turbo (Marvin) |
|
Back to top |
|
 |
raygreenwood Samba Member
Joined: November 24, 2008 Posts: 23091 Location: Oklahoma City
|
Posted: Tue Jul 08, 2025 12:22 pm Post subject: Re: Big engine + NOT downshifting.... damages 4th gear |
|
|
Sodo wrote: |
MarkWard wrote: |
Shifting out of forth to let the gear and bearing face relax just doesn’t fit in to our use. |
I agree that if I tried to get my mom "to lube 4th gear," I would be awarded with a blank stare.
It's not to relax 4th gear,
it's a lubrication "effort" to counter a 4th gear lubrication deficiency that's been known for 20, 30 years (hence the creation of "VW South Africa oiling plates")
What conditions the deficiency occurs.... is lesser known. It's a STORM of oil vapor in there,
and YET,
erosion phenomena occurs
that can only happen in the absence of oil.
We're certain its dry otherwise there would be no erosion.
I suspect the oiling plates (a popular mod) do throw oil up, but this oil only gets in upon downshift or decel.
And the oiling plates logically only throw oil at certain speeds + temperature-viscosities anyway,
two factors that we know nothing about.
This is mostly a long-distance, cruise-control steady-conditions problem.
There has to be a steady condition for the oil to deplete (to dry).
Steady, like "throttle mashed, no decel, no downshift"
Subject title says "Big Engine...."
If you have a WBX, this is of less importance because maybe you drive the van slower, and have to downshift often anyway.
But this lubrication deficiency was appearing back in the day long before big engines. It's just WORSE with big engines,
The owners mainly interested in this are those who have spent big bucks and somewhat understand gearboxes, metallurgical phenomena, or maybe they have a big engine & enjoy 80MPH in spite of their good sense.
Or had un-satisfactory longevity from a quality rebuilder.
The rebuilders themselves "should" be interested.
80mph is for short periods is OK..... but after lubrication has depleted, bad things are happening at any speed where any contact surfaces are dry (inside your gearbox).
The evidence is there. This type of erosion only happens when dry.
I suspect electricity increases the rate because more electricity is conducted when dry. |
This is a great thread! I have been meaning to post an answer here.
This will be a little long but Please bear with me...
I do not own a Vanagon. However, a lot of the issues and problems and solutions the vanagon guys get into are some of the same I have been diagnosing and working for my VW 411's and 412's that have manual transmissions.
So, I have been lurking here for a couple of years because a couple of people have suggested that you are working along some of the same lines I have been working on.
The type 004 transmission in my 412 has a pair of 18mm x 20mm needle bearings, one at each end on a fixed 18mm shaft supporting a single one piece counter shaft with all four counter gears rotating around that fixed solid shaft. The gear has a single oiling hole in the center and blind ends against thrust washers. In other words...shit for oiling.
Some observations:
1. Going back a page to where you were calculating and worrying about needle bearing speed and load...while you may definately be onto something (meaning the needle bearing application may be under engineered or engineered improperly), unless you are willing to totally change that bearing and shaft at 4th gear out to something this is known to be properly engineered....I say do not worry that much about the load factors.
You have more important fish to fry here.
First, in your calculations you noted you used a tolerance of 50 microns. I hope that was not shaft to needle tolerance. Because, 50 microns...which is only 0.8 microns short of 0.002"...would be a huge and massive failure tolerance for the vast majority of needle bearings we "should" be finding in our transmissions.
Of course, to know what the tolerance should be between needles and shaft you need to ask the bearing mfg and tell them the shaft hardness, the housing diameter, precise shaft diameter, lubrication type, shaft speed and temperature range....and probably more.
All of that said, most small needle bearings like you are finding on your 4th gear and I find in my counter gear....will usually have advertized tolerances LESS than 25 microns in the whole stack up. So, between needles and shaft there is usually ~0.0005" (about 12.7 microns) or LESS on each side.
Also keep in mind that a great many needle bearings that have tight tolerances, actually have "crowned" needles....meaning they are not perfect straight rods. It also means that the center of the needles are usually a dead fit to the shaft and the outer race. At temperature you may find a tolerance of ~0.0001" or 2.52 microns.
2. looking at your picture a page back of the highly polished 4th gear needle bearing shaft race area....I am wondering if your applications have what I have seem in some other VW/Audi transmissons (especially like mine)....which is shafts that are softer than they should be.
Yes, with any bearing (just like lifters and cams) one surface has to be softer. Usually it is the less easily replaceable part like the shaft...that will be harder. But in most transmission I have seen, the shafts are softer than the bearings.
You find this on shaft assemblies in transmissions because the hardening process typically creates a "cast" or bend to the linear part making it no longer straight enough. You cant really remachine something straight after its been surface hardened. So, the parts are not really hardened except maybe some case hardening.
My point....the shaft area should NOT be super polished like that in your picture. While it IS evenly polished and SEEMS to be free of imperfections, you can see that single line near the middle of the polished area (no, you cannot feel that but if I can see it, chances are my surface profile gauge can FEEL it) this also may point to slightly crowned needle bearings wearing a line in the center.
Any burnishing or polishing over and above what it came with from the factory....is metal loss. Even if its only 0.00005" (~about 1.27 microns) on each side, thats a total loss of 0.0001"....or 2.54 microns....which is a LARGE change for a needle bearing.
That goes toward your statement of "slop" in needle bearings and this WILL wear them out fast.
More on why and how the shaft gets super polished below.....
Some of the things I think you Vanagon guys are really onto in my opinion....
1. Yes!!!!....the occasional downshift can probably save your needle bearings!
I will have to go through the Vanagon diagrams but in my 004 transmission, constant long hours of running on the highway will NOT allow oil to get into the single 0.095" hole in the hollow counter shaft that feeds both needle bearings.
Yes, my countershaft shaft has a 20mm hollow center with an 18mm shaft in it and that hollow space around the shaft fills up with oil when you sit still....but...while running...with gear thrust....keeping the counter gear up hard against the thrust washer at one end...THERE IS NO EXIT FOR THE OIL IN THE NEEDLE BEARING.......NO FLOW TRHOUGH OR REPLENISHMENT.
AND...SO....the microscopic bits of metal that get worn off the softer shaft just keep recirculating around the needles and...ARE...."the abrasive" that polishes the shaft and causes it to be probably 0.0005" UNDERSIZED....which will cause chattering and spalling.
So if you have no flow through of oil in these areas, you are trapping oil and the impurities that will be the abrasive that kill your shaft and bearing.
The main reason why I lurk in this forum is the vanagon guys ideas about forced lubrication for locations like this....and you guys are spot on!
2A. The poor ground situation....electrolytic damage of the bearings. I can tell you for sure that while this IS possible, it would be EXCEEDINGLY rare on an automotive transmission...except in one situation which I will explain in a moment in part 2-B.
Aside from working on a lot of cars over the years I work in a LOT of industrial enviroments. Over the years (I am 62 now) I have been in over 4000 factories working on things that are wide ranging.....lots of oils and lubricants and heat and chemicals. I have SEEN electrical damage to ball and roller bearings....under specific conditions ONLY. More in a moment.
So, the transmission case is a magnesium alloy... right? The ground strap is attached to either a steel stud embedded in the magnesium case or a steel through bolt clamping on the magnesium case....right?
First, in order of best to worst electrical conductivity:
Silver
copper
annealed copper
gold
aluminum
brass with 5% zinc....
....and 11 steps below brass...is carbon steel. Other steels are even lower than this. The differences....magnesium is only about half as conductive as aluminum....and is twice as conductive as Iron. Iron is easily more conductive than steel by an order of magnitude.
RULE....electrons...electricity...follows the path of least resistance...ALWAYS.
Think about this: If your ground strap is attached to a bolt embedded in the magnesium (or aluminum) alloy case that fully encloses the steel inner workings....why would the electrons NOT flow all aroudn that case first to reach the mating surface of the engine case.
The magnesium case and the aluminum engine case are orders or magnitude higher electrical conductivity than the shafts in your transmission and ....the bolt that attches the ground strap to that case is not attached to the steel shafts directly. There would be no propensity whatsoever for the current to travel through the mainshaft and bearings.
If it were the other way around (just for conversation)....a steel case transmission with aluminum or magnesium shafts and gears....sure....that would be the path of least resistance electrically.
If you have a bad joint between the ground strap and the steel stud or boltr and the transmission case....the joint is the point of resistance and its the joint that heats up.
Most important point in this electrical ground damage issue:
Virtually every oil used anywhere in automotive but especially gear oils and motor oils....have a pretty high dielectric constant. Meaning, they are insulators. They do not easily conduct electricity. While nowhere near as dielectric as a silicone dielectric grease, they certainly resist electrical flow.
2B. So back to where electrical ground damage and where and how it happens.
A few days back in another post in this forum were some picture from the SKF catalog describing "electrical damage" to bearings. The top picture was NOT from electrical current flow. It was from mechanical "precession" and is spalling.
However, the lower picture where you see distinct marks from rollers or balls...IS from electrical contact and flow and is mostly happening when the system, machine, transmission etc....is sitting idle....oil pressure or flow is gone...oil has drained or dripped down...and its metal to metal...and auxilliary systems are still pulling power from ground through the chassis.
But again, on our transmissions...there are too many places with orders of magnitude higher electron flow potential...other than the steel bearings and shafts...where ground would flow.
3. To the black oil found inside of cases in relatively short amounts of time. This IS actually ELECTROLYTIC action and not caused by grounding issues.
This is especially prevalent in high magnesium content cases. What is happening is more common in "four seasons" gegraphic areas. As temperatures in spring and fall go up during the day and drop down at night and you have high humidity....air inside teh case expands during the day and breathes out through the vent. Later, as things cool it breathes in. This sucks in humidity, dew point drops and it condenses inside.
You may only get a handful of drops of actual condensed moisture per day....but over say a year....thats a lot of water. It gets "shear blended " into the oil...and no...it will not cook off.
That water causes oxidization of the sulfur in both GL-4 and 5 gear oils creating a dilute sufuric acid. This causes a blackening of aluminum/magnesium alloys and will cause greenish corrosion to copper parts (not likely you have any) and also make the oil black in appearance.
IMPORTANT NOTE: this also depletes/neutralizes the sulfur which is one of the extreme pressure additives in gear oil....and can make the oil fail to lubricate certain parts.
Anyway...sorry for the length. Great thread! Ray |
|
Back to top |
|
 |
Sodo Samba Member
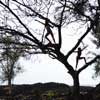
Joined: July 06, 2007 Posts: 10613 Location: Western WA
|
Posted: Tue Jul 08, 2025 3:35 pm Post subject: Re: Big engine + NOT downshifting.... damages 4th gear |
|
|
raygreenwood wrote: |
This is a great thread! I have been meaning to post an answer here.
This will be a little long but Please bear with me...
excellent. I have been hoping you would reply.
You're a pig in the mud (me too)
I will delete some comments but that doesn't mean I'm not interested.
Ray I would chat with you at the campfire all night.
1. Going back a page to where you were calculating and worrying about needle bearing speed and load...while you may definately be onto something (meaning the needle bearing application may be under engineered or engineered improperly), unless you are willing to totally change that bearing and shaft at 4th gear out to something this is known to be properly engineered....I say do not worry that much about the load factors.
Not worrying about load or bearing speed. 32 RPM.
The effort is to prove that bearing speed is NOT ZERO while the idler is locked to the input shaft.
That the needles do NOT contact the shaft in one line when you're "in 4th gear".
The needles roll slowly while you're "in 4th gear", burnishing the shaft to a mirror-shine.
The shaft center is NOT coincident to the idler gear center.
The two centers are "OFF" by 50 microns diametral slop (50 being an example of bearing clearance).
This causes a precession.
The needles roll slowly on the shaft like a hula-hoop even though the gear and the shaft are locked together at identical RPM.
The 50micron 'slop' was an average number plucked from an SKF bearing specs table for a 40mm bearing (20-70 microns).
50 microns clearance on a 40mm bearing with 2.5mm rollers mathematically produces a cage rotation of 32rpm at 3600rpm (65mph).
The cage rotates once every 2 seconds. But so what?
Choose a different slop, get a different cage RPM.
The 32 RPM dispels the notion that the needles are stationary when the idler is coupled to the shaft.
The slow precession (rolling) around the shaft produces that mirror-finish.
Only when they are stationary can the needles "false-brinnell' the shaft.
If they get 'chocked' by break-in trash, they can become stationary.
Then while chocked, AND upon oil-depletion after a LONG gas-pedal-mashed event,
erosion commences,
and you have false-brinnelling.
Once you have brinnelling, the needles may fall into the slot next time, and unable to climb out,
and then as the bearing dries (at next extended-pedal-mashed-event),
erosion commences again,
and the needle-lines get deeper.
This is why I say DO NOT drive a new trans on a long trip, pedal mashed, especially with a big engine.
Change the oil a few times first, and while it's "NEW", shift often between 3rd &4th to burnish the new shaft & bore.
Once burnished, the surface will become tougher (work-hardened, forged).
A new shaft & bore, and especially in the contaminated environment of bedding-in-oil
is MOST vulnerable to "brinnelling".
I suspect very mild brinnelling can be healed, or burnished away, but deep brinnelling is a PERMANENT injury to a new gearbox.
here is a pic where you can see minor brinnelling
I have seen mainshafts with a very smooth mirror shine,
with an 'undulating pattern' in the mirror shine that could be early brinnelling that has "healed" over time.
....in your calculations you noted you used a tolerance of 50 microns.
(the 50 microns fish was fried ^^above^^)
Also keep in mind that a great many needle bearings that have tight tolerances, actually have "crowned" needles....meaning they are not perfect straight rods. It also means that the center of the needles are usually a dead fit to the shaft and the outer race. At temperature you may find a tolerance of ~0.0001" or 2.52 microns.
Interesting.... I measured a USED 4th gear needle and it's not much crowned. It appears the same tenths of inches end-to-end. Perhaps crowned in tenths of tenths, but that could be wear on the ends which are loaded higher due to the helical gear-cocking forces.
Some of the things I think you Vanagon guys are really onto in my opinion....
We're ON IT because we over-engine. Everybody over-engines, but we do it a little differently.
We hang a big engine on an undersized gearbox.....and then we submit it to a high continuous duty (the brick). It's not like a race car that pushes real hard for a bit - then lets up.
It's continuous duty, for hours.
Then next week it has Kayaks ontop.
And then a Hi-Top camper top is added.
And soon after, a tube-rack and solar panels. then kayaks ontop of that.
And then the ECU is chipped and bigger tires added.
1. Yes!!!!....the occasional downshift can probably save your needle bearings!
Yes, my countershaft shaft has a 20mm hollow center with an 18mm shaft in it and that hollow space around the shaft fills up with oil when you sit still....but...while running...with gear thrust....keeping the counter gear up hard against the thrust washer at one end...THERE IS NO EXIT FOR THE OIL IN THE NEEDLE BEARING.......NO FLOW THROUGH OR REPLENISHMENT.
Not sure i understand that arrangement... I'm very specifically focused on the Vanagon trans 091/1 and 094 and a little on the 091.
Lubrication simply has to be "sufficient".
Accelerated wear occurs when lubrication is insufficient.
So we want to remain in the "sufficient" category.
Not sure how 'occasional' that is.
Every 5 minutes? 15 minutes? 30 minutes? Who could know?
OK
...with that.... if oil cannot get in, while centrifugal forces "deplete" and oppose re-entry of oil, its a one-way ticket to accelerated wear.
Some time ago I calculated that the forces expelling oil from a 40mm bearing @3600 RPM are something like 300 times the force of gravity.
AND...SO....the microscopic bits of metal that get worn off the softer shaft just keep recirculating around the needles and...ARE...."the abrasive" that polishes the shaft and causes it to be probably 0.0005" UNDERSIZED....which will cause chattering and spalling.
So if you have no flow through of oil in these areas, you are trapping oil and the impurities that will be the abrasive that kill your shaft and bearing.
Metal-to-metal (asperities touching in the lack of oil-film-separation) under conditions of micro-motion is where 'fretting corrosion' erodes steel. at some pressure, the asperities actually 'weld' momentarily but the movement breaks each 'weld' almost immediately. Sometimes the particles remain welded (material transfer) other times they break off.
These steel particles are very active and quickly pick up oxygen,
especially if the oil is old & oxidized.
Here is a pic where you can see the red Fe2O3 on the mainshaft bearing thrust surface. (MsTaboo!!)
The mating surface on 4th gear looks similar. This can only occur in the absence of lubrication.
The particles either become Fe2O3 or Fe2O4.
Fe2O3 is non-magnetic, red, and very abrasive, one of the most abrasive compounds known.
Fe2O3 crystals are sharp and triangular.
Jeweler's Rouge polishing compound is Fe2O3,, it's called Hematite ('cuz it's red like blood).
Fe2O4 is magnetic, black, and mildly abrasive. It's crystals are rectangular, not as sharp.
Fe2O4 is called Magnetite.
It blackens the oil and piles up on the drain magnet.
The main reason why I lurk in this forum is the vanagon guys ideas about forced lubrication for locations like this....and you guys are spot on!
I've had forced splash since 2016 and then drove 80mph as if my gearbox was invincible.
We found brinnelling and evidence of dry conditions at 40k miles.
Forced splash, while likely better, was clearly not sufficient.
But this gearbox had the additional assault of "no engine ground"
because the "conversion installer" felt that the forward transaxle ground was all that was necessary.
Around 2021 we started to study 'corrosion fretting' a wear phenomenon that occurs under micro-motion where there is no oil separation.
In 2022 I started pumping oil into the mainshft, and the oil comes out into the input idler bearings of the 3rd & 4th idlers.
And the oil is continually re-supplied at the 4th-gear thrust interface where you see the erosion on DougnLina's pics.
I am hopeful.
Taking it apart to see if the 4th gear wear has been solved is a BIG DEAL.
Who pays for this research?
I am very interested though.
=================================
2A. The poor ground situation....electrolytic damage of the bearings. I can tell you for sure that while this IS possible, it would be EXCEEDINGLY rare on an automotive transmission...except in one situation which I will explain in a moment in part 2-B.
......
RULE....electrons...electricity...follows the path of least resistance...ALWAYS.
My RULE would be like this "....electrons...electricity... will divide current among all available paths, where each path takes as much current as the other paths have rejected".
As the case stackup assembly increases in resistance due to the dissimilar metals, outdoor environment, and lack of maintenance, the internal shiny steel takes more and more and more (over the 40 years).
Think about this: If your ground strap is attached to a bolt embedded in the magnesium (or aluminum) alloy case that fully encloses the steel inner workings....why would the electrons NOT flow all around that case first to reach the mating surface of the engine case.
....
EXAMPLE: A Subaru gearbox is a split-case design. The starter is bolted to the left side case-half. At the front of the transmission, the ground-strap could logically ground to that same left-side case half. That continuous casting will conduct a monumental amount of current. Even so, Subaru grounds the starter to the chassis directly, not burdening the gearbox case with "gearbox duty PLUS electrical duty'".
On our VWs, it's NOT one continuous casting from the starter
(a high-amperage electric machine)
to the front of the gearbox.
It's a stack like a wedding cake.
Perhaps your 412 is similar.
Aluminum starter to
steel nut(s)
to steel stud(s)
to magnesium bellhousing
to steel bolt(s)
to magnesium main case
to steel bolt(s)
to magnesium gear carrier
to steel bolt(s)
to magnesium steel nose
to steel bolt(s)
to steel transmission bracket to copper groundstrap
to steel chassis.
Every connection's resistance is additive.
Dissimilar metals of less than desirable compatibility,
in an outdoor environment,
and non-maintained
for 40 years.
The ground path employs the assembly as a current path explicitly.
Could a slightly longer copper cable from the starter to chassis....
really add so much cost?
It's really sort of stupid.
Or MFR smart like a "lifetime fluids" ( a planned obsolescence scheme to fail old cars).
Luckliy it can be nullified with a $15 direct copper ground.
Everyone should "just do it" even if you think your van cranks OK.
Perhaps ESPECIALLY if "some condition" made you want a faster starter,
and thus installed one.
Shiny transmission bearings, and shafts going from one end to the other could easily compete with a corroded bolted case assembly
as additive series-resistance increases over the YEARS.
That dry interface of 4th gear at the mainshaft bearing
(=the subject of this thread)
could be the electron's favorite connection.
Which draws even more amperage across the other subpaths, bearings, gears.
More experienced mechanics have been known to focus on the ONE copper-to steel strap at the front transmission mount.
I never hear of mechanics tending to the other (seven?) UPSTREAM connections that supply the strap.
Most important point in this electrical ground damage issue:
Virtually every oil used anywhere in automotive but especially gear oils and motor oils....have a pretty high dielectric constant. Meaning, they are insulators. They do not easily conduct electricity. While nowhere near as dielectric as a silicone dielectric grease, they certainly resist electrical flow.
yeah the power has to cross where the steel asperities touch.
Its logical that electricity accelerates the micro-erosion but I have not found any study of this on the internet.
Possibly becasue it's just "too stupid", no fool would risk electricity crossing a bearing.
Steel, brass and magnesium particles in the oil can be a bridge piercing the oil film.
2B. So back to where electrical ground damage and where and how it happens.
A few days back in another post in this forum were some picture from the SKF catalog describing "electrical damage" to bearings. The top picture was NOT from electrical current flow. It was from mechanical "precession" and is spalling.
I am curious which damage you say was due to precession.....
The pic of my bearing referring to page 38.
(more info on this image)
And here's the SKF "Bearing Failure and Analysis.pdf" document
However, the lower picture where you see distinct marks from rollers or balls...IS from electrical contact and flow and is mostly happening when the system, machine, transmission etc....is sitting idle....oil pressure or flow is gone...oil has drained or dripped down...and its metal to metal...and auxilliary systems are still pulling power from ground through the chassis.
In general when the gearbox is not turning, there's not much electrical power. That's the mainshaft bearing.
If the alternator is turning, the clutch must be pressed down to stop the mainshaft bearing, clutch disengaged is a fairly short event in vehicle lifetime.
I'm curious in the industrial eqpt you have seen, how often do you see gearbox cases,
full of expensive, mission-critical precision rolling elements
used double-duty as a high amperage current-carrying path?
I would think only a fool would do that,
when a simple copper cable from the large electric machine ISOLATES ,
the other expensive precision bits from any possible electrical damage.
In the above-linked SKF doc, there are hundreds of pics of bearing surface failures, but only one pic on p38 looks like electrical.
Electrical damage is easily identified.
Probably should take a look at the SKF document.
But again, on our transmissions...there are too many places with orders of magnitude higher electron flow potential...other than the steel bearings and shafts...where ground would flow.
Orders of magnitude higher amps flow on a new trans case with new bolts, maybe for 10 or 20? years.
But not for an old transaxle, sitting outdoors under a van for 40 years, and many in wet environments.
I say,
Ground the starter and the alternator with a direct copper cable.
ISOLATE the gearbox purposefully to minimize risk that errant electricity can (ever) damage internal precision rolling elements.
Here's a Question for you.... why do you think the reverse light switch has two wires?
Why didn't VW just ground the switch to the (grounded) transmission case?
On the Syncro, the locker-light switches are isolated, with two wires too.
3. To the black oil found inside of cases in relatively short amounts of time. This IS actually ELECTROLYTIC action and not caused by grounding issues.
This is especially prevalent in high magnesium content cases. What is happening is more common in "four seasons" gegraphic areas. As temperatures in spring and fall go up during the day and drop down at night and you have high humidity....air inside teh case expands during the day and breathes out through the vent. Later, as things cool it breathes in. This sucks in humidity, dew point drops and it condenses inside.
You may only get a handful of drops of actual condensed moisture per day....but over say a year....thats a lot of water. It gets "shear blended " into the oil...and no...it will not cook off.
Very small amounts of water in oil causes a significant loss in film strength. Thats another reason for shorter intervals.
You say the water doesn't boil off....hmmm.
I have read that 150F-to 180F is an ideal gearbox temperature range, one of the reasons stated - that its high enough to expel condensation.
That water causes oxidization of the sulfur in both GL-4 and 5 gear oils creating a dilute sufuric acid. This causes a blackening of aluminum/magnesium alloys and will cause greenish corrosion to copper parts (not likely you have any) and also make the oil black in appearance.
IMPORTANT NOTE: this also depletes/neutralizes the sulfur which is one of the extreme pressure additives in gear oil....and can make the oil fail to lubricate certain parts.
Anyway...sorry for the length. Great thread! Ray |
"sorry for the length", he says.....heh _________________
'90 Westy EJ25, NEW oil rings (!) 2Peloquins, 3knobs, SyncroShop pressure-oiled pinion-bearing & GT mainshaft, filtered, cooled gearbox.
'87 Tintop w 47k 53k, '12 SmallCar EJ25, cooled filtered original gearbox
....KTMs, GasGas, SPOT mtb |
|
Back to top |
|
 |
raygreenwood Samba Member
Joined: November 24, 2008 Posts: 23091 Location: Oklahoma City
|
Posted: Thu Jul 10, 2025 12:20 pm Post subject: Re: Big engine + NOT downshifting.... damages 4th gear |
|
|
Sodo...great response. Thank you!
Quote: |
EXAMPLE: A Subaru gearbox is a split-case design. The starter is bolted to the left side case-half. At the front of the transmission, the ground-strap could logically ground to that same left-side case half. That continuous casting will conduct a monumental amount of current. Even so, Subaru grounds the starter to the chassis directly, not burdening the gearbox case with "gearbox duty PLUS electrical duty'". |
Oh yes! We (the automotve public) were starting to see this even in VW's by the late 80's and early 90's in the watercooled cars. You could see this in Mk1 and mk2 rabbit and jetta with ground cables coming from chassis to engine and from chassis to transmission.
From working on enough of them and seeing ground cables left out and seeing what it caused, I "speculate" that it was not really for carry starting amperage but to create a more electrically "clean" supply for items like the digifant injection (which was very problematic with grounds) and for chassis and cockpit electronics etc.
This is not saying that it did not help amperage flow for starting and charging but the immediate effects from having a poor ground connection or a missing cable were on electronics.
Quote: |
Not worrying about load or bearing speed. 32 RPM.
The effort is to prove that bearing speed is NOT ZERO while the idler is locked to the input shaft.
That the needles do NOT contact the shaft in one line when you're "in 4th gear".
The needles roll slowly while you're "in 4th gear", burnishing the shaft to a mirror-shine.
The shaft center is NOT coincident to the idler gear center.
The two centers are "OFF" by 50 microns diametral slop (50 being an example of bearing clearance).
This causes a precession.
The needles roll slowly on the shaft like a hula-hoop even though the gear and the shaft are locked together at identical RPM. |
Ah!...got it! More clear what you were getting at.
But...I persist....you should NOT have a mirror shine like that on the 4th gear shaft. They are not that polished from the factory. When they are that polished....there is no micro-tooth to hold lubricant. While something like a crankshaft is polished with 360 to 600 grit and a needle bearing surface maybe a little finer......it should be smooth with general polih but not bright with "mirror" polish.
On one hand...looking like that....it does seem to be running evenly...but to get to that state of polish, enough high points from thesurface profile have been removed that you have changed the tolerance. Its wear.
It gets this way because the needle bearing is harder than the shaft. This is an issue that is too common in transmissions and even more so if flow through oiling is not great.
Quote: |
Only when they are stationary can the needles "false-brinnell' the shaft.
If they get 'chocked' by break-in trash, they can become stationary. |
Yes....and when they are stationary....oil is squeezed out....AND...if there were an abnormal amount of current being pulled through the shaft from a grounding issue...this is when the surface of the shaft would be the most susceptible to electrolytic erosion.
OK...a couple of things:
1. Burnishing is not the same as polishing. Polishing always removes material. Burnishing works by smoothing over the edges of the scratches and closing pores in the metal (quote stolen from NAWCC website because its good).
Burnishing creates a smoother measurable (not always visible) profile, many times without changing the tolerance very much at all. It does not remove metal peaks in the profile, it bends them over and is directional.
Also.....rarely will it increase polish or luster. I totally agree...burnishing in of a bearing is a good thing. This is precisely why for instance that you have two different tolerances listed for setting pre-load on something like a differential bearing. One for brand new and one looser one for bearings with 30 miles or more on them. They have been burnished in.
BUT....when you see POLISH...like mirror polish...you are seeing thermeoval of metal.
The question of when it becomes significant on a needle bearing tolerance will typically matter depending on what type of needle bearing.
For instance: on my transmission and in 091's and many others used on must of the gears....are large free floating needle bearings that snap into a nylon ring. Typically these needles are maybe 1/2" long and something like about 0.070" diameter.
These are almost alwasy "straight" needles. really they act more like a roller bearing. The nylon ring is just a spacer.
In other transmissions and in racing you can see this nylon ring being removed and if the spacing is just right you can use what they call "hand packed" needles with no spacer ring.
BUT....then you come to rigidly caged needle bearings usually without an outer race (meaning they are not inside of a tube or can). These have a steel cage holding the needles spaced. Many of these are "crowned" needle bearings.
The tolerances on alot of these caged/crowned needle bearings are EXTREMELY tight. They are usually a DEAD FIT...with no "feelable" gap to the shaft once they are installed in the bore that surrounds the shaft. The shaft to needle crown tolerance is maybe 0.0001"-ish...or just a couple of microns.
The taper to the needles means that the real oil gap is at the ends.
These kind of needle bearings tolerate NOTHING. No dirt...no debris...and no wear. When they start wearing out the shaft....they start bouncing....which causes BRINELLING.....which brings me to...
2. Brinelling does not heal. Brinelling is caused by repeated pounding, creating dents which compacts the metal and creates spots that are not only harder but havea new dimension and tolerance within those spots. It only gets worse.
So...Question...what kind of needle bearing is your 4th gear shaft using? Rigidly caged or plastic spacer ring?
Quote: |
Not sure i understand that arrangement... I'm very specifically focused on the Vanagon trans 091/1 and 094 and a little on the 091.
Lubrication simply has to be "sufficient".
Accelerated wear occurs when lubrication is insufficient.
So we want to remain in the "sufficient" category.
Not sure how 'occasional' that is.
Every 5 minutes? 15 minutes? 30 minutes? Who could know?
OK
...with that.... if oil cannot get in, while centrifugal forces "deplete" and oppose re-entry of oil, its a one-way ticket to accelerated wear.
Some time ago I calculated that the forces expelling oil from a 40mm bearing @3600 RPM are something like 300 times the force of gravity. |
Just having sufficent oil is not enough IF there is not any flow through and replenishment....because...and this is another thing that the Vanagon guys understand and you are the ONLY forum in this entire site that discusses or understands this.....the oil gets hot....it thins....it breaks down.
You guys have actively been working on force fed oil and cooling and worry about temperature. I cannot tell you how many discussions in other forums have stated (and this is very type 1 centric thinking)...."manual transmission oil does not get very hot). Uh...yeah...it does....and I have measured it in my 004 transmissions.
On long highway drives in 100* weather, I have clocked 200* F constant and peaks over 250*F on my gear oil. That is TOO HOT. Over the years I have lost about four of these 004 transmissions (which are far more rare even than synchro transmissions). The autopsy's always pointed to a combination of not enough lubricant in specific places (design issue of the needle bearings) and overheated and thinning oil in others.
While 250* is not THAT extreme....it is when there is less than a thimble full of oil on each needle bearing in a dead end bore at each end of a shaft with no flow through. If one could just occasionaly get another thimble full in there to displace what is over heated and shear thinned....damage could be avoided.
I do not want to clutter up your thread. It IS about Vanagon transmissions.... but just so you have a mental picture of why I am interested in some of the same tech you guys are and why my type of transmission has some of the same issues....I invite you to look at this transmission rebuild thread. This one is on ice right now submerged in oil. I hope to get back to final rebuild early next year.
The 004 transmission is pretty unique. While it looks a little like the 091 from the outside...its totally different from any of the types 1,2,3 transmissions inside and is a true hypoid with more mesh and much higher final drive. It actually shares more in design with some early watercooled Audi transmissions.
https://www.thesamba.com/vw/forum/viewtopic.php?t=639756&highlight
The needle bearings that are the most problematic to my transmission (the countershaft needle bearings) I start into at the top of page 2 in that thread.
Ray |
|
Back to top |
|
 |
Sodo Samba Member
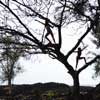
Joined: July 06, 2007 Posts: 10613 Location: Western WA
|
Posted: Fri Jul 11, 2025 9:11 am Post subject: Re: Big engine + NOT downshifting.... damages 4th gear |
|
|
raygreenwood wrote: |
Sodo...great response. Thank you! |
I'm glad someone likes it.
You're looking at about 8 hours (^^above reply^^).
I enjoy this because it forces me to clarify my own understanding of these wormholes.
Everyone says "someone should figure out why VW gearboxes last only 150k while Toyota gearboxes last 400k."
Indeed.
SyncroShop and I are very interested.
We don''t always agree on 'every detail' ....
For example he likes Synthetic oil, I'm not yet convinced.
I do agree synthetic is superior if driving style overheats your gearbox.
Those with big engines who drive fast, sustained should add a temperature gauge.
Quote: |
We (the automotive public) were starting to see this even in VW's by the late 80's and early 90's in the watercooled cars. You could see this in Mk1 and mk2 rabbit and jetta with ground cables coming from chassis to engine and from chassis to transmission.
From working on enough of them and seeing ground cables left out and seeing what it caused, I "speculate" that it was not really for carry starting amperage but to create a more electrically "clean" supply for items like the digifant injection (which was very problematic with grounds) and for chassis and cockpit electronics etc. |
Starting amperage and alternator amperage.
Alternator amp-hours is by far the largest.
Erosion is caused by big amps for short periods and small(er) amps for long periods.
The alternator puts out smaller amps but the amp-hours is much much larger.
It's like the "tortoise (alternator) and the hare (100Amps starter)".
If the van has a hungry LiFePO4 battery the alternator amps are pretty big, and hard-charging can sustain "for hours".
raygreenwood wrote: |
This is not saying that it did not help amperage flow for starting and charging but the immediate effects from having a poor ground connection or a missing cable were on electronics. |
Continual electrical gearbox erosion does not put the vehicle on a flatbed like an electronic grounding fault.
But accumulation of electrical gearbox erosion over years eventually disappoints the antiquer.
If you have a big house battery, it's faster.
I had mainshaft bearing that grumbled after 20,000 miles.
If you make sure your gearbox is grounded for big starter amps, and your alternator case
is grounded for lesser amp numbers (but much higher amp-hours)...
there's
by default,
sufficient current capacity for all the milliamp ground demands of sensors and electronics.
Not to mention diagnosis efforts being more conclusive, and shorter.
The big grounds need to be qualified "under load" though (the voltage drop test), not static (the ohm-meter micro-volts test).
Little grounds, sensor grounds, generally don't need to qualify "under load",
especially if the big grounds have less than 0.2volts drop "under their big loads".
Incidentally, little sensor grounds, added willy-nilly, are at risk to burning up if the high-current grounds are the actual fault.
If you add little sensor grounds (for testing purposes) it's wise to NOT bundle them against other important wires.
Suspend them where they can burn up (fuse) without melting other insulations, and no secured with plastic cable ties.
If you understand the why this is a risk, then focus instead, upon making your high-amperage grounds "proper".
And omit the little sensor grounds.
Quote: |
Quote: |
Not worrying about load or bearing speed. 32 RPM.
The effort is to prove that bearing speed is NOT ZERO while the idler is locked to the input shaft.
That the needles do NOT contact the shaft in one line when you're "in 4th gear".
The needles roll slowly while you're "in 4th gear", burnishing the shaft to a mirror-shine.
The shaft center is NOT coincident to the idler gear center.
The two centers are "OFF" by 50 microns diametral slop (50 being an example of bearing clearance).
This causes a precession.
The needles roll slowly on the shaft like a hula-hoop even though the gear and the shaft are locked together at identical RPM. |
Ah!...got it! More clear what you were getting at.
But...I persist....you should NOT have a mirror shine like that on the 4th gear shaft. They are not that polished from the factory. When they are that polished....there is no micro-tooth to hold lubricant. While something like a crankshaft is polished with 360 to 600 grit and a needle bearing surface maybe a little finer......it should be smooth with general polish but not bright with "mirror" polish.
On one hand...looking like that....it does seem to be running evenly...but to get to that state of polish, enough high points from thesurface profile have been removed that you have changed the tolerance. Its wear.
It gets this way because the needle bearing is harder than the shaft.
This is an issue that is too common in transmissions and even more so if flow through oiling is not great. |
The 4th gear idle needle bearing race gets mirror-burnished and you can't measure a difference between the shiny part and the un-touched part.
Quote: |
Only when they are stationary can the needles "false-brinnell' the shaft.
If they get 'chocked' by break-in trash, they can become stationary. |
Quote: |
Yes....and when they are stationary....oil is squeezed out....AND...if there were an abnormal amount of current being pulled through the shaft from a grounding issue...this is when the surface of the shaft would be the most susceptible to electrolytic erosion. |
Not stationary though, it's dynamic.
And more importantly, it's not accidental.
It's electrical erosion due to amps crossing precision rolling elements.
By design, because the gearobx hasn't been "ISOLATED from the two biggest (attached) electrical machines".
Alternator and Starter. A sustained high-amps-Producer and a periodic 100Amp consumer.
Direct grounds from the housings of these two machines is the best bet to protect wayward amps from crossing precision rolling elements.
It's easy and $15 to reverse this poor design.
Everyone who understands ground-cable installation, should change grounding on their van to gearbox case ISOLATION.
Quote: |
OK...a couple of things:
1. Burnishing is not the same as polishing. Polishing always removes material. Burnishing works by smoothing over the edges of the scratches and closing pores in the metal (quote stolen from NAWCC website because its good).
Burnishing creates a smoother measurable (not always visible) profile, many times without changing the tolerance very much at all. It does not remove metal peaks in the profile, it bends them over and is directional. |
Agreed. It's more like forging than grinding.
Burnishing toughens the surface!
The shaft and gear are vulnerable to Brinnelling when 'new & raw'
Brinnelling commences when 4th gear dries out (sustained load in 4th gear).
Even worse when it's a big engine in the meat of it's torque curve (70-75mph) if pushing 2x harder on it than it was designed for.
For hours.
Quote: |
Also.....rarely will it increase polish or luster. I totally agree...burnishing in of a bearing is a good thing. This is precisely why for instance that you have two different tolerances listed for setting pre-load on something like a differential bearing. One for brand new and one looser one for bearings with 30 miles or more on them. They have been burnished in.
BUT....when you see POLISH...like mirror polish...you are seeing thermeoval of metal.
The question of when it becomes significant on a needle bearing tolerance will typically matter depending on what type of needle bearing. |
Dunno about that. Look at AnyBees lustrous mainshaft.
Quote: |
When they start wearing out the shaft....they start bouncing....which causes BRINELLING.....which brings me to...
2. Brinelling does not heal. Brinelling is caused by repeated pounding, creating dents which compacts the metal and creates spots that are not only harder but havea new dimension and tolerance within those spots. It only gets worse.
|
Brinnelling is from pounding. Material is displaced.
False Brinnellng looks like brinelling but has no raised edge.
False brinnelling is from erosion. Material has 'departed'.
I have a shaft here that appears like it 'rolled out' some early brinnelling to a lustrous, undulating shine.
Quote: |
So...Question...what kind of needle bearing is your 4th gear shaft using? Rigidly caged or plastic spacer ring?
|
Original is plastic caged.
Steel caged aftermarket are often substituted.
I don't know that I agree with the steel cage substitution.
Perhaps for a gearbox that will be driven while overheated,
yes that solves the problem of the melted plastic cage by an overheated (dry) 4th gear.
But steel may have higher friction than the plastic cage.
I worry that steel cage can can increase the chance of halting the VITAL precession.
Constant precession, constantly rolling over 'strings of new oil' is vital to avoid brinnelling.
In my case ( never overheating 4th ! ) I suspect plastic caged is better.
Quote: |
you are the ONLY forum in this entire site that discusses or understands this.....the oil gets hot....it thins....it breaks down.
You guys have actively been working on force fed oil and cooling and worry about temperature. I cannot tell you how many discussions in other forums have stated (and this is very type 1 centric thinking)...."manual transmission oil does not get very hot). Uh...yeah...it does....and I have measured it in my 004 transmissions.
On long highway drives in 100* weather, I have clocked 200* F constant and peaks over 250*F on my gear oil. That is TOO HOT. Over the years I have lost about four of these 004 transmissions (which are far more rare even than synchro transmissions). The autopsy's always pointed to a combination of not enough lubricant in specific places (design issue of the needle bearings) and overheated and thinning oil in others.
While 250* is not THAT extreme....it is when there is less than a thimble full of oil on each needle bearing in a dead end bore at each end of a shaft with no flow through. If one could just occasionaly get another thimble full in there to displace what is over heated and shear thinned....damage could be avoided. |
250F is NOT too hot for oil, especially not too hot for synthetic.
But it's definitely too hot for a gearbox case of white-metal that holds bearings by thermal-fit alone.
The Vanagon mainshaft bearing loosens at 180F when all is "new".
The bore wears, and many have become loose at room temperature.
A split-case, with preloaded steel bolts holds the steel bearings better at high temperatures.
The Vanagon gearbox relaxes it's thermal fit at the mainbearing bore at around 180F.
So above 180F, bad things are happening.
The shafts are moving apart as the case expands, and the gear pitch circles are no longer in alignment, thus tooth face contact is sliding, not rolling.
Lots of un-desirable things are happening.
Now there's "sliding at tooth faces" .... which have thinning oil.
There's a long list.
Sustained, fast, peak-HP-curve usage is where you want 85w140 oil.
If you like to drive like this, you should then "accommodate" the laborious shifting when cold.
Incidentally, as the mainshaft bearing bore loosens, then less electricity flows across the mainshaft bearing, protecting it somewhat in its old age.
A new, tight bore will logically pass more errant electricity to the front groundstrap, lessening as the bore wears.
Quote: |
The 004 transmission is pretty unique. While it looks a little like the 091 from the outside...its totally different from any of the types 1,2,3 transmissions inside and is a true hypoid with more mesh and much higher final drive. It actually shares more in design with some early watercooled Audi transmissions.
https://www.thesamba.com/vw/forum/viewtopic.php?t=639756&highlight
The needle bearings that are the most problematic to my transmission (the countershaft needle bearings) I start into at the top of page 2 in that thread. |
I'm quite interested in this wormhole, as you may have noticed, but have to be away from TheSamba for the next week or so, dangit....
This subject of 4th gear has two forks.
Electrical, and Lubrication.
They are both assaults, but one is easily solved with $15 of proper grounding.
The discussion of why to invest in this grounding change does take a lot of effort.
I think it should be a very short discussion culminating in a $15 investment and install. Better yet $30 and ground the alternator case too.
The lubrication discussion is in need of a genuine lubrication engineer. _________________
'90 Westy EJ25, NEW oil rings (!) 2Peloquins, 3knobs, SyncroShop pressure-oiled pinion-bearing & GT mainshaft, filtered, cooled gearbox.
'87 Tintop w 47k 53k, '12 SmallCar EJ25, cooled filtered original gearbox
....KTMs, GasGas, SPOT mtb |
|
Back to top |
|
 |
Howesight Samba Member
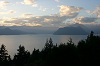
Joined: July 02, 2008 Posts: 3400 Location: Vancouver, B.C.
|
Posted: Fri Jul 11, 2025 11:18 am Post subject: Re: Big engine + NOT downshifting.... damages 4th gear |
|
|
Sodo:
Thanks for you unceasing work on addressing this Syncro transaxle set of conundrums!
Regarding:
"Sustained, fast, peak-HP-curve usage is where you want 85w140 oil.
If you like to drive like this, you should then "accommodate" the laborious shifting when cold."
I run Swepco 210 (it is 80W-140) on Darryl Christiansen's advice received 14 years ago and so far, so good. I only want to comment on the cold shifting issue. This phenomenon, in my experience, lasts no longer than 5 minutes and, in winter, maybe ten minutes. It's easily addressed with double clutching. So, for those selecting less viscous oils to address this "problem", I say it is no problem at all. _________________ '86 Syncro Westy SVX |
|
Back to top |
|
 |
GoEverywhere Samba Member

Joined: December 13, 2020 Posts: 859 Location: Portland, OR
|
Posted: Sun Jul 13, 2025 8:22 pm Post subject: Re: Big engine + NOT downshifting.... damages 4th gear |
|
|
Well... This thread might have just become an lesson for my high powered Vanagon. Just lost my 4th gear. I'm curious when I pull it out if its gonna be a failure like you've all been talking about here, or if something else let go! |
|
Back to top |
|
 |
AndyBees Samba Member
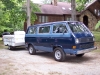
Joined: January 31, 2008 Posts: 2620 Location: Southeast Kentucky
|
Posted: Sun Jul 13, 2025 8:34 pm Post subject: Re: Big engine + NOT downshifting.... damages 4th gear |
|
|
GoEverywhere wrote: |
Well... This thread might have just become an lesson for my high powered Vanagon. Just lost my 4th gear. I'm curious when I pull it out if its gonna be a failure like you've all been talking about here, or if something else let go! |
If you still have 3rd gear, likely that "high powered" engine ripped the teeth off 4th gear. Is the transmission OE?
I rebuilt one for a guy about two years ago that all the teeth on 4th gear were gone. He drove it many miles in 3rd gear on secondary roads to get home. I upgraded 3rd & 4th gears with the Weddle racing gears that have heavy teeth and lots of nose. _________________ '84 Vanagon Tin-top, ALH TDI, two trips to Alaska, 2014 & 16. 1989 Tin-top unmolested.
1983 Air-cool, 225k miles, 180k miles mine, seven trips to Alaska from 1986 thru 2003. 1975 Bay hopeful. |
|
Back to top |
|
 |
GoEverywhere Samba Member

Joined: December 13, 2020 Posts: 859 Location: Portland, OR
|
Posted: Sun Jul 13, 2025 8:52 pm Post subject: Re: Big engine + NOT downshifting.... damages 4th gear |
|
|
AndyBees wrote: |
GoEverywhere wrote: |
Well... This thread might have just become an lesson for my high powered Vanagon. Just lost my 4th gear. I'm curious when I pull it out if its gonna be a failure like you've all been talking about here, or if something else let go! |
If you still have 3rd gear, likely that "high powered" engine ripped the teeth off 4th gear. Is the transmission OE?
I rebuilt one for a guy about two years ago that all the teeth on 4th gear were gone. He drove it many miles in 3rd gear on secondary roads to get home. I upgraded 3rd & 4th gears with the Weddle racing gears that have heavy teeth and lots of nose. |
The transmission was upgraded with various weddle bits before this engine by my local trans shop. But I'm 100% absolutely exceeding even those gears power capacity(I had it built for my previous 170HP engine.) . I drove mine home about 50 mile in 3rd on back roads to get it home. 1-3 seem totally fine.
So if 3rd gear was still there its not the under oiling issue they're hunting here? Maybe its just reading this thread recently but thats right where my brain went.
So if I had the 4th under oiling issue 3rd |
|
Back to top |
|
 |
|